Safety Lessons from the National COSH Dirty Dozen
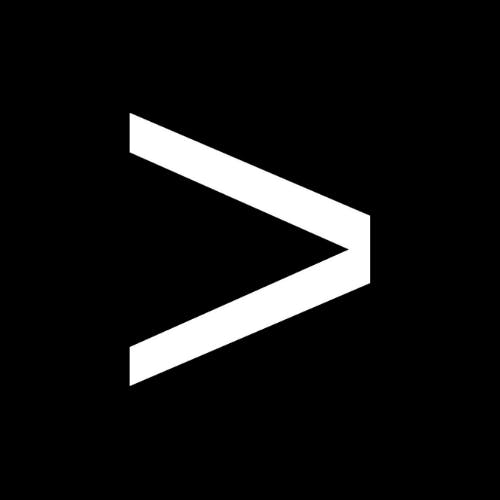
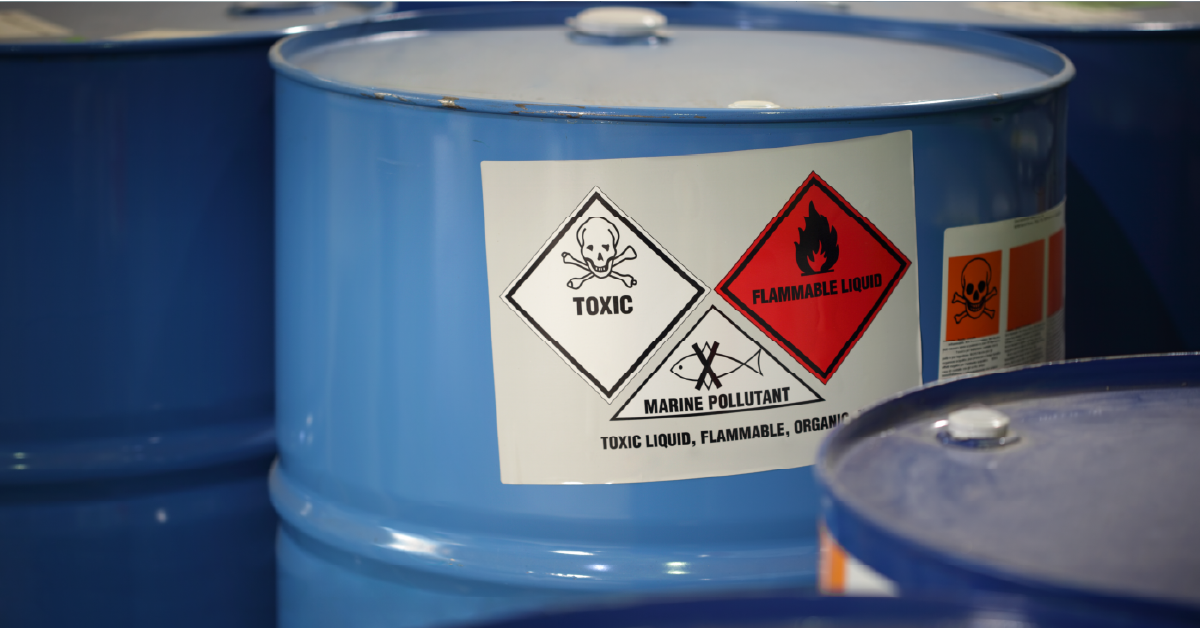
Every year, the National Council for Occupational Safety and Health (COSH) releases a list of its “Dirty Dozen” unsafe employers. The list represents 12 examples of what the organization calls the most egregious behavior in exposing employees to preventable hazards. Appearing on the COSH Dirty Dozen list this year are household names like Amazon, Hilton, Starbucks and Dollar General.
So what can manufacturers take away from the report to avoid safety issues and protect workers?
In today’s article, we look at lessons from this year’s COSH Dirty Dozen, and how manufacturers can prevent similar safety problems.
Watch a free webinar on Why 2022 Is the Year to Take Safety Inspections Digital
COVID Safety
Covid safety failures are a key focus of this year’s Dirty Dozen, with the report noting an estimated 20 percent of infections, or 9.7 million adults, attributable to workplace transmission.
Examples of employer behaviors cited in the report include:
- Not providing masks or other personal protective equipment (PPE) to workers
- Overcrowded work areas
- Inadequate ventilation in work areas
- Punitive policies towards workers who must quarantine
Despite the fact that no national occupational health standard exists around COVID-19 safety, infections have a huge impact on employers and employees. Beyond the significant human toll, outbreaks can disrupt operations and increase employee turnover, impacting quality and safety.
How to prevent: Manufacturers should have COVID-19 safety protocols in place, and a system for verifying they are followed on the plant floor. Frequent safety inspections can help identify PPE noncompliance, as well as safety concerns employees may have.
Workplace Violence
Employers often consider workplace violence a random occurrence. As the COSH report points out, however, leadership has the responsibility to take action when aware of potential problems.
The organization points specifically to a string of violent crimes at a national chain of dollar stores where workers have been punched, stabbed, and even fatally shot. Safety failures noted include understaffing and inadequate security, which investigative journalists at ProPublica say have made dollar stores “magnets for crime”
How to prevent: While manufacturers don’t face the same workplace violence risks as retail or industries that deal with the public, worker-on-worker violence and spillover from domestic violence are significant risks. Companies should have a workplace violence program to train employees to identify the warning signs. They should also include protocols for responding to workplace violence within emergency plans.
Emergency Response Plans
The COSH report notes an incident where a tornado struck a manufacturing plant and killed nine workers, attributing the tragedy to failure in emergency response planning.
Employees report managers ordering workers to stay onsite or risk being terminated when tornado warnings first happened. COSH co-executive director Jessica Martinez told the Louisville Courier Journal, “Were they thinking about their wages or survival? If there was a plan in place, those discussions would not have been taking place.”
How to prevent: Manufacturers are required to have an emergency action plan under CFR 1910.38. In addition to requirements around establishing procedures, companies are required to train employees on the plan and review it with each employee. This must happen when:
- The plan is created and/or changed
- When an employee is first assigned to a job
- When a worker’s responsibilities change under the plan
Manufacturers should periodically verify that people understand what to do in an emergency, both by exercising the plan and through safety inspections.
Toxic Exposures
Several employers are called out in the COSH report for exposing workers to toxic chemicals. One chemical plant accounted for three fatalities after multiple incidents spanning two years. The fatal incident occurred due to multiple failures, including failure to:
- Provide appropriate PPE
- Follow safe work practices during equipment maintenance activities
- Perform air monitoring for chemical exposures
- Provide written procedures identifying the necessary level of respiratory protection
- Communicate chemical hazards to employees
Six more workers died after a deadly nitrogen leak at a separate food manufacturing facility, with a toxic ammonia release occurring just two months later.
How to prevent: OSHA’s Process Safety Management standard requires employers to ensure appropriate use of respiratory protection and PPE when working around hazardous chemicals. Employers also have an obligation to make sure employees follow process safety management procedures, making ongoing verification of safety activities a critical prevention tool.
Training Failures
One sad case highlighted in the COSH Dirty Dozen is of a worker who died of heat exposure and dehydration. The company had last provided training on extreme heat hazards a month before the worker died.
How to prevent: While heat exposure isn’t a typical risk in manufacturing plants, this incident shows the importance of making sure all workers receive the appropriate training. Using safety inspections to verify training effectiveness can help ensure there aren’t gaps that could lead to a safety incident.
In many instances, companies have landed on the Dirty Dozen due to repeat occurrences of incidents. Again, this is an area where frequent, even daily safety inspections can make a difference in proactively preventing incidents.
A digital safety inspection platform like EASE can help by making it easier to complete checks, view findings and assign mitigations or corrections. By streamlining the inspection process, plants can conduct more checks and generate more data they can use to effectively prevent workplace injuries.