The #1 Mistake in Layered Process Audit Programs
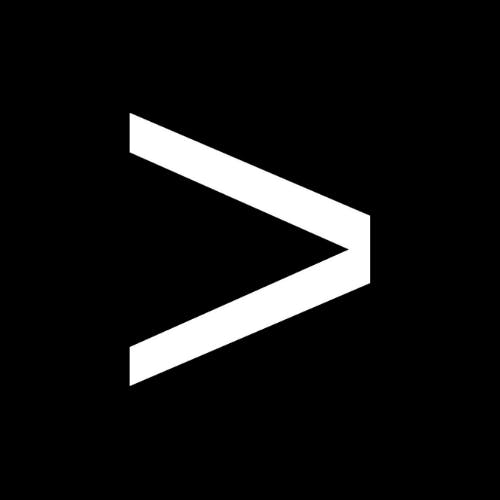
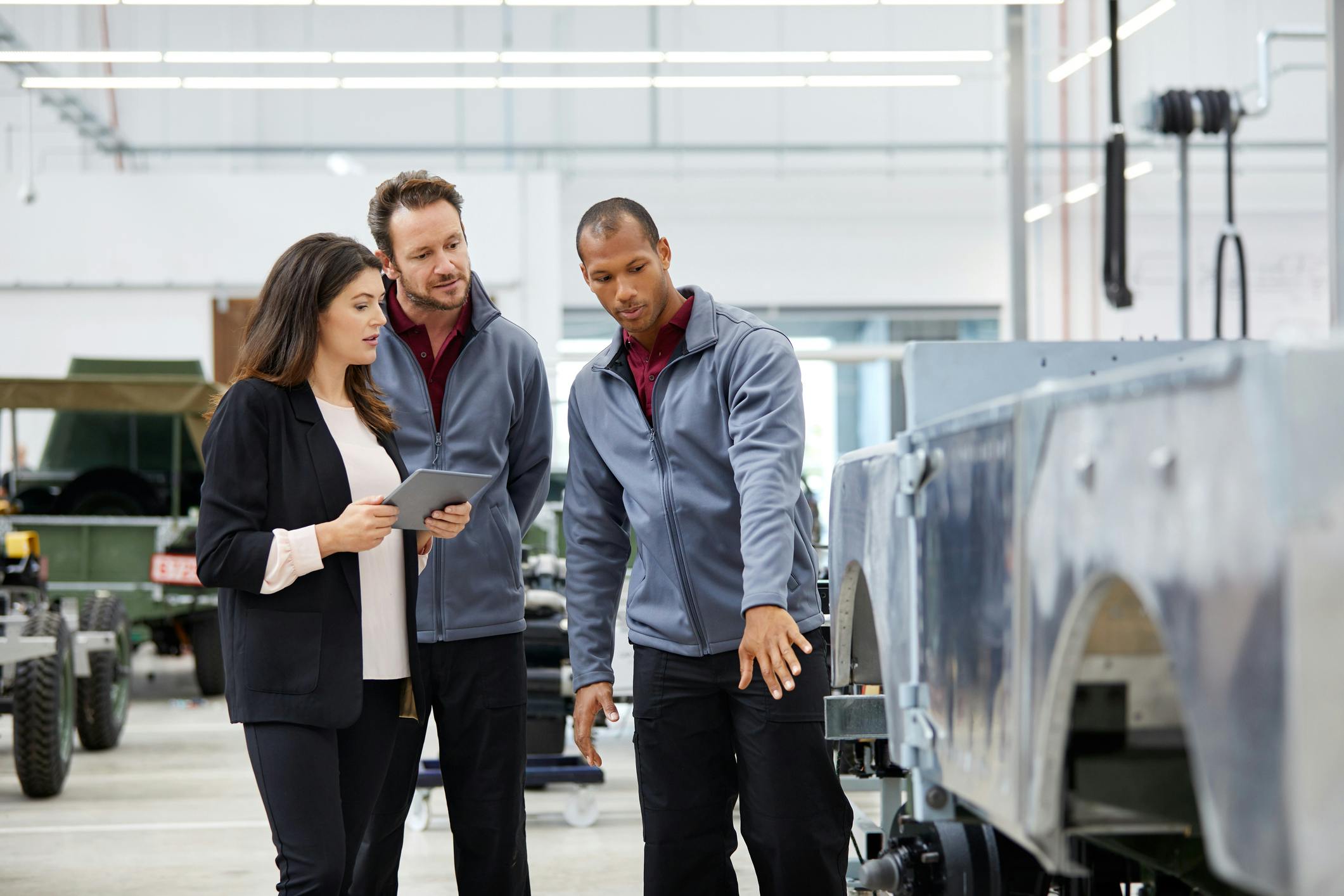
Layered process audits (LPAs) are a standard requirement in the automotive industry, which saw more than 53 million vehicles recalled in 2016, according to the U.S. Department of Transportation. The reality is that many companies struggle with implementing an LPA program effectively due to the overwhelming complexity of scheduling and data management.
The number one mistake we see these companies make? Trying to manage LPA programs with paper-based and spreadsheet-based systems.
Executed properly, LPA programs require hundreds or even thousands of individual audits over the course of the year. It’s extremely difficult to do the multilayer scheduling correctly with spreadsheets alone, and next to impossible to fully analyze the results for meand aningful quality improvements with a paper-based system.
Automated LPA systems eliminate the burden of scheduling data analysis, eliminating two mindless, valueless activities that sap energy from a LPA program.
The True Definition of an LPA Program
LPAs are a method for frequently checking high-risk processes most likely to cause defects or safety issues. Compared to inspection based assurance procedures, LPAs are a way to catch process mistakes before they result in defective products.
LPA programs involve multiple layers of management, with audit responsibilities typically spread across at least 3 different levels of the organization.
The Reality of Manual LPA Programs Rough calculations show that this level of audit frequency can quickly add up in terms of number of audits. A facility with 100 workers would need to schedule well over 2,000 audits per year, with larger facilities requiring even more. These audits represent quality validations that enable continuous quality improvement and overall better market differentiation—that is, if you get it right.
So how many of these thousands of annual audits are automotive suppliers actually completing? Most companies are lucky to get 10% of them done, and those with better rates often suffer from a corresponding increase in pencil-whipped results.
The fact is, just passing all items for the sake of completing the audit does not mean you’re meeting the requirements of IATF 16949. Nor are you meeting them if you’re just filing away paper checklists in some binder or file cabinet. The entire purpose of LPAs is to systematically reduce risk, which you’re not doing if you take a passive “check the box” approach.
Here’s the sad part about it: companies running manual systems often have to devote 1-2 full-time employees just for scheduling alone, to say nothing of processing the data after the audits. What many companies have is a bottleneck, with insufficient numbers of audits completed, and significant lag time until the data is analyzed. Often it is never analyzed until a high-exposure failure prompts a review of the historical performance.
From this perspective, the difficulties of scheduling and analyzing results of 2,000-plus audits annually raise the question of whether manual systems qualify as LPA programs at all.
The Role of Automated LPA Management
Implementing LPA software addresses many of the problems associated with manual LPA management. These automated systems get to the heart of quality and IATF 16949 compliance, ensuring LPA programs are:
- Consistent: Companies can assign and schedule recurring audits to 50 staff members for an entire year in less than 10 minutes. Email reminders go directly to the staff member at the time of the audit, with a link right to the audit questions so there’s no searching for checklists.
- Robust: Automated software protects data integrity with randomization, question pooling, pattern alerts and timed audits. Preventing pencil-whipping helps make the transition from a compliance-based culture to a more proactive, engaged quality culture.
- Data-driven: Data is available while it’s still actionable, as opposed to reviewing it weeks or months later when an auditor is onsite. Daily, weekly and monthly reporting helps you keep the team informed and identify important trends that could impact customers.
The fact that so many suppliers are not even close to where they need to be with their LPA programs should be a major concern for auto manufacturers. It’s also something that should concern suppliers, who are risking the very relationships that their businesses are built on.