The Connected Workforce: Using Technology to Empower Frontline Workers
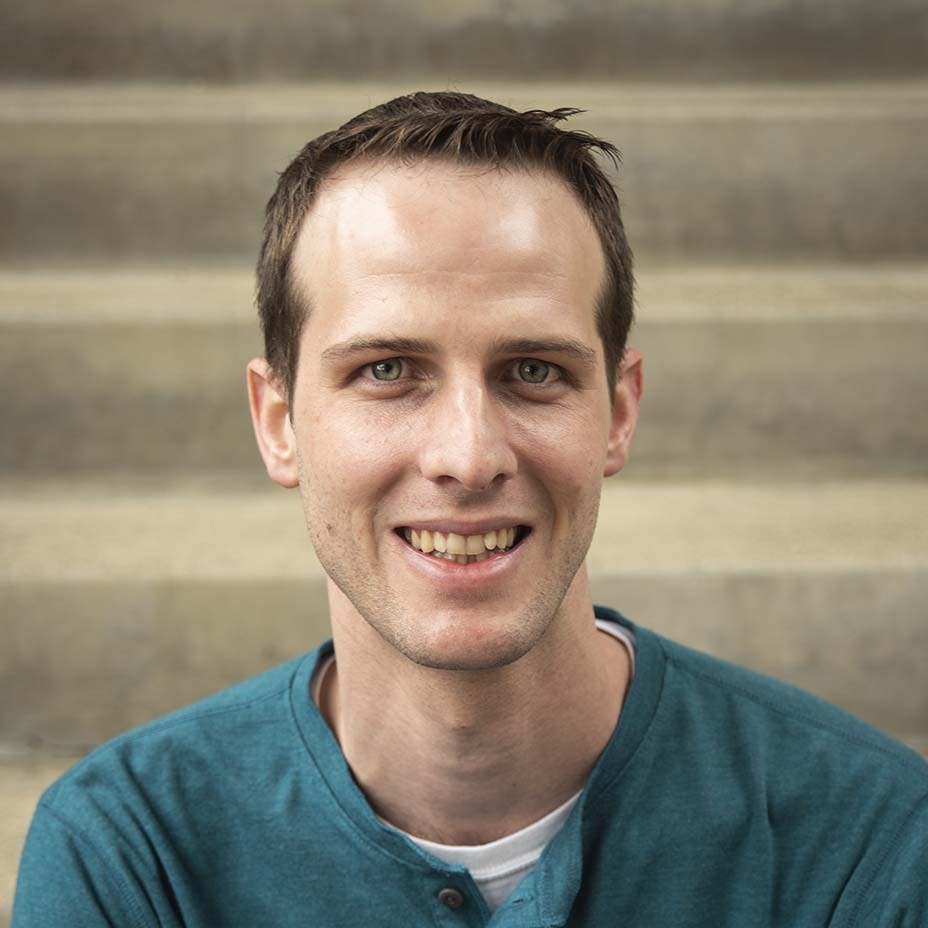
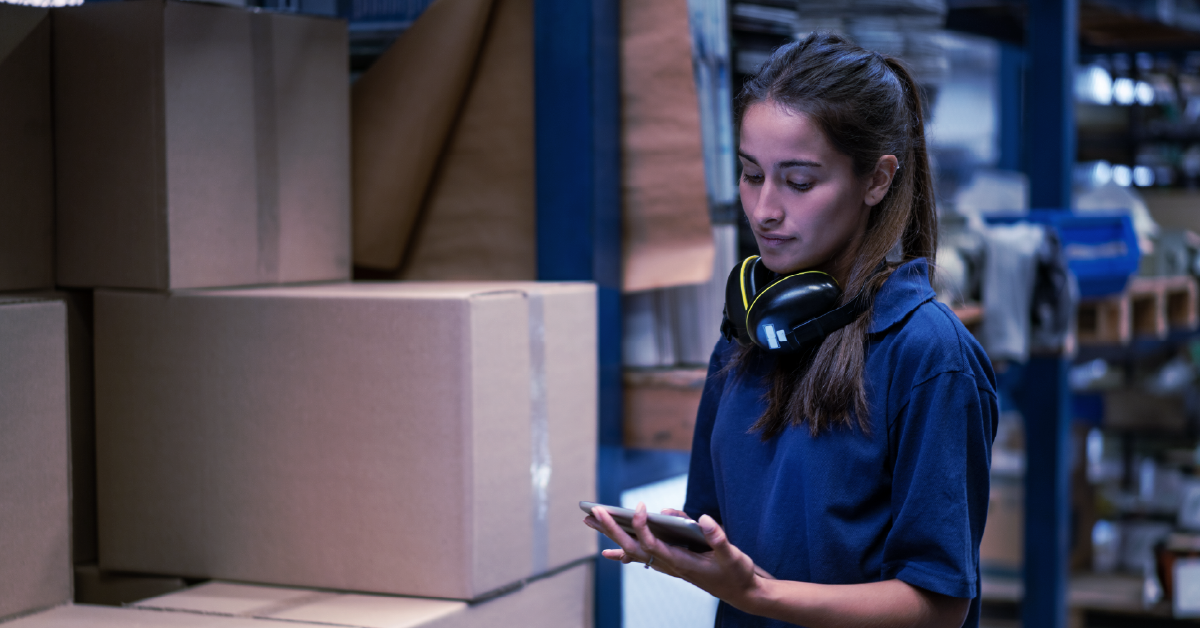
According to LNS Research, more than 40% of manufacturers today use technologies like connected workforce solutions to manage plant floor knowledge.
It’s just one way digital transformation is creating a more connected workplace, giving frontline workers a leading role in continuous improvement efforts.
In this article, we take a look at this emerging quality trend, how it’s changing the face of manufacturing and things to consider before jumping in.
Download a free white paper to learn How Digital Safety Inspections Help Manufacturers Work Safer
What Is a Connected Workforce?
The connected workforce refers to technology that empowers frontline workers with real-time data, communication and information on the plant floor. Connected workforce technology in manufacturing focuses on applications such as:
- Digital Lean training, troubleshooting guides and work instructions
- Cloud-based forms and checklists for audits and inspections
- Instant messaging and real-time collaboration tools
- Automated issue management and documentation
- Wearable and mobile devices, augmented reality (AR) and Industrial Internet of Things (IIoT)
Benefits of a Connected Workforce
Creating a connected workplace as part of your plant’s digital transformation strategy offers many potential benefits that we detail below. These include:
- Flexible learning
- Better teamwork and collaboration
- Reduced defects and costs
- Improved employee engagement
Flexible Learning
Connected worker solutions provide digital tools for more operator-centric employee training that meets people where they are. Flexible, targeted on-the-job learning reduces shadow days and training costs, while also helping standardize processes.
For example, these platforms can provide customized procedure checklists that meet the needs of operators new to a process as well as those already familiar with it. Initially, new operators may need to check off each step in a 10-step process, eventually graduating to just checking off three critical-to-quality steps. Once fully certified, the operator may only need to confirm the final quality check.
Compared with traditional training processes, this approach gets new workers productive faster. It also makes training more interactive and engaging, so workers aren’t just endlessly clicking through computer modules but rather learning through practice.
Better Teamwork and Collaboration
Connecting your workforce digitally—both among your team and to plant floor data–enhances collaboration and communication to identify and solve problems faster.
Factory feed apps, for example, can provide targeted quality alerts and production updates to the plant floor. Real-time communication with engineering and management also gives operators needed support when there’s a call for help on the plant floor.
A connected workplace can also unlock significant value in resource-intensive processes requiring multiple steps and handoffs. McKinsey researchers point to two big opportunities here for manufacturers: maintenance and root cause analysis. They point out that investigating the root cause of problems can take more than 90 days, with delays and added costs arising from:
- Not capturing data effectively
- Having to coordinate multiple schedules and sometimes bring experts onsite
- Redundant fixes that don’t leverage previous solutions to similar problems
Connected workforce solutions change the equation by enabling more efficient data capture, for example by uploading photos of plant floor conditions or accessing equipment data to diagnose problems. Experts can also collaborate remotely, while the resulting fix is more easily shared across the organization.
All in all, McKinsey estimates that digital collaboration on root cause analysis can add $70 million to the bottom line for a manufacturer with $10 billion in revenue. For maintenance, where the challenges are similar, digital collaboration has the potential to add $110 million in revenue.
Fewer Defects and Customer Complaints
A primary driver for implementing connected worker solutions in manufacturing today is the potential to drive down defects, complaints and costs. Examples include:
- Identifying malfunctioning equipment with IIoT sensor data to automatically notify maintenance and guide operator response
- Using digital plant floor checks such as layered process audits and 5S audits to standardize processes, find teachable moments and address non-conformances that cause defects (e.g., tools needing repair)
- Automating autonomous or operator-driven maintenance checklists to remind workers of key checks to complete at specific steps
- Providing live engineering support, digital troubleshooting guides, and faster responses to plant floor needs (e.g., requests for additional components)
McKinsey research suggests faster problem-solving with digital tools can reduce scrap by 25%, which equals $50 million in savings for a $10 billion company. More than just hypothetical savings, one automotive manufacturer was able to reduce internal PPM by 73% with digital process audits alone.
Improved Engagement
Employee retention and engagement are critical priorities for manufacturers today given that the manufacturing skills shortage shows no sign of easing.
Connected workforce solutions improve employee engagement in several ways:
- Workers know that any issues raised will receive the proper follow-up, giving them more ownership of quality and safety and making them feel valued
- Operators have confidence they are doing their jobs right—a central element of job satisfaction and employee retention
- Improved collaboration and real-time communication builds a sense of teamwork and collective responsibility
- Ongoing training opportunities give workers the chance to build new skills and advance their careers
- Enhanced safety monitoring shows employees that leadership truly cares about them
Bringing Your Workforce Together with the Right Platform
If your organization is thinking about implementing connected worker technology, there are a few factors to consider as you begin your journey.
First, one issue that can be a barrier to success is not having well-established standards. The problem is that trying to deploy technology without the basics in place is like trying to build a house with no foundation—it’s destined for failure.
Instead, you need to invest the upfront effort in developing standards like work instructions and standard operating procedures (SOPs). Only once you have standards established can you apply connected workforce technology to upholding those standards and streamlining production.
Next, you need to identify the problem you want to solve and compare it to the cost of implementation. Connected workforce initiatives can range from focused Lean projects such as digitizing plant floor checks to large-scale IIoT implementations requiring significant IT resources. The key is choosing a problem that, once solved, will deliver a positive return on investment.
Connected workforce technology is becoming a leading driver of industrial transformation that’s changing the face of how manufacturing teams work together. Improved engagement, dynamic learning, and reduced quality costs are all potential upsides, with a few caveats. Companies must take the time to ensure they have standards in place, choosing a high-value project worth the effort required for digital transformation.