The Role of Quality Leaders in Supporting Business Continuity
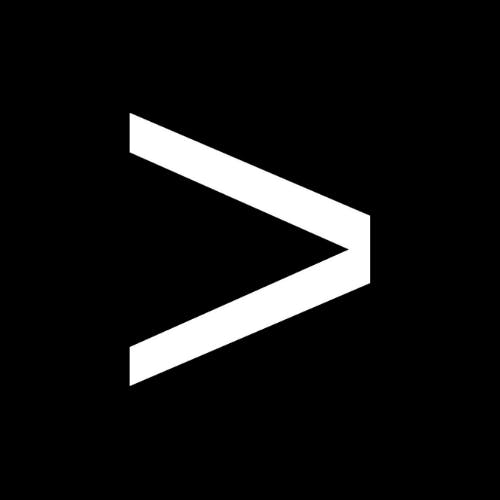
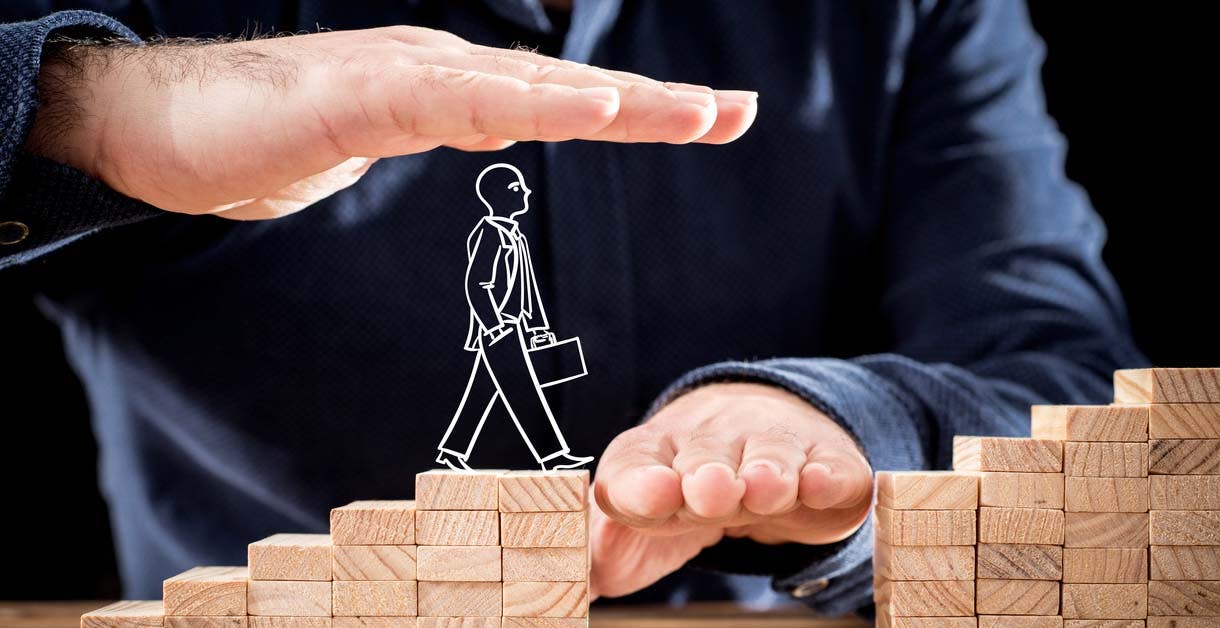
Quality management has earned an unfair reputation over the years, treated as a mere formality or compliance obligation to get out of the way.
The COVID-19 crisis, however, has revealed the truth about quality’s strategic role in the organization.
More than just paper-shuffling and statistical analysis, quality management is directly linked to business continuity, ensuring consistent operations and product quality despite external challenges.
In this post, we take a look at how the pandemic has flipped the script on quality management, as well as a unique auditing method to help quality leaders verify process adherence amid industry change and disruption.
Quality Management’s Image Problem
Most quality leaders got into the profession due to a genuine interest in helping companies make better products. Despite these good intentions, however, quality management tends to get a bad rap.
They’re the sticklers for details. The enforcers of policies. The ones raising red flags when a plant is pushing hard to complete a big order.
Whether deserved or not, quality is often seen as something that happens in an office, concerned more with paperwork than plant floor operations. This image problem has made it very difficult for quality leaders to make an impact in the way that many had hoped to do when they started their careers.
But like it has done so many other places, the coronavirus crisis has changed the equation. Quality is an increasingly critical line of defense, helping keep businesses on a steady course as the manufacturing industry adapts to changing conditions.
Pandemic Puts Quality in the Spotlight
Manufacturing saw some of the biggest changes in decades in 2020 as a result of the pandemic, with wide-ranging effects across different industries.
Automotive manufacturing plants shut down for eight weeks in the spring, followed by a restart unlike any seen before and a stronger than expected rebound. As restaurant traffic dwindled or stopped altogether in some areas, retail food sales grew 85% last year while the food industry strained under fast-growing demand. Still other companies shifted production to critical medical supplies like ventilators and personal protective equipment (PPE).
On top of changes in demand, companies had to adjust production lines to accommodate social distancing requirements, added shifts and missing workers. Supply chain disruption has been a pervasive problem, with many organizations having to rely on different suppliers with whom they have less experience.
In all of these situations, businesses face the same question:
How can we make sure quality is consistent amid such rapid change?
Verify Processes, Not Just Products
Given these challenges, companies need a way to ensure process adherence to root out defects when processes and lines are undergoing change. Compared to product inspections, process audits are a more effective way to do this.
For example, Auto News reported an instance where Subaru recently learned the hard way what can happen when even a single operator strays from standardized processes. In this situation, an operator using an incorrect torque wrench technique ultimately required the company to recall hundreds of vehicles.
So which approach would have been more likely to catch the problem, a process audit or a product inspection? Clearly, a process audit would be the only way to find this issue prior to manufacture.
Layered Process Audits as a Business Continuity Driver
Layered process audits (LPAs) put process verification on steroids. LPAs provide multiple levels of verification for high-risk or critical to quality process inputs. High-risk processes are audited on a daily basis, with auditors participating at a frequency based on their job role.
In essence, you have multiple individuals doing daily checks of process inputs known to cause quality problems, for example equipment settings or specific procedure steps. This provides more opportunities to catch defects before product gets shipped to the customer.
Benefits of this unique approach include:
- Leverage down the cost of quality by finding problems before they cause complaints
- Ensuring compliance with standards when there are changing setups and team members involved with a process
- Preventing quality escapes and audit findings that threaten business reputation
- Reducing rework that accounts for important operating capacity
Mobile audit software like EASE is key to getting the most value from LPAs. This type of platform manages scheduling and administration details so quality leaders can focus on analyzing audit findings and following up on problems.
At the end of the day, quality professionals have always known that the work they do is essential to business continuity. Today’s industry challenges, however, are making that truth more visible, providing quality leaders the opportunity to make an impact as never before.