Top Industry 4.0 Trends for Manufacturers to Keep an Eye on in 2020
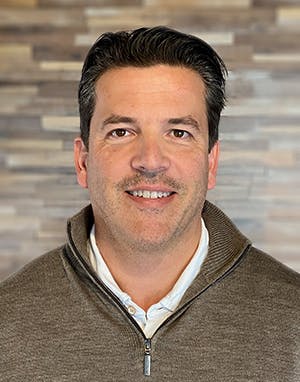
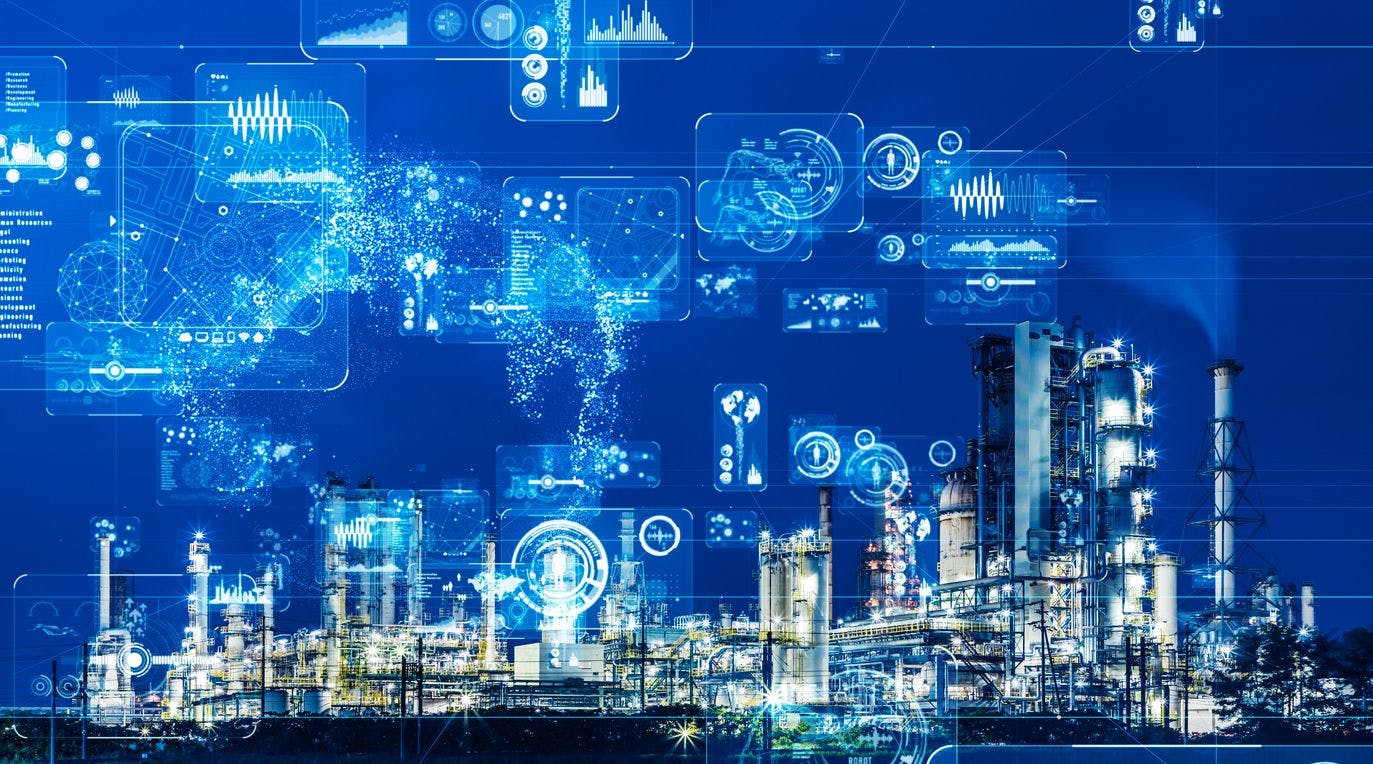
According to a 2019 BDO benchmarking survey, 99% of middle market manufacturing executives consider themselves somewhat familiar with Industry 4.0 trends, despite the fact that only 5% have an Industry 4.0 strategy.
Dubbed the fourth industrial revolution, Industry 4.0 centers on connected cyber-physical manufacturing systems that leverage advanced technologies like artificial intelligence (AI), cloud computing and the internet of things (IoT).
As these technological developments proliferate every year, companies must carefully evaluate which investments have the biggest potential to improve productivity and profitability.
In this post, we examine Industry 4.0 trends at the forefront of manufacturing in 2020, including artificial intelligence of things (AIoT), Quality 4.0, 5G and virtual reality (VR).
Learn how a global automotive supplier cut defects 73% with a digital audit platform.
AIoT is the New Frontier
One of the biggest Industry 4.0 trends that manufacturers should have on their radar is the convergence of Internet of Things (IoT) and Artificial Intelligence (AI), also known as Artificial Intelligence of Things (AIoT). According to Gartner, upwards of 80% of IoT initiatives will incorporate AI by 2022, compared to just 10% today.
AI takes IoT to the next level in two key ways. First, IoT sensors equipped with AI become smart sensors capable of not just collecting and sending data, but also making decisions. Second, AI allows companies to unlock insights faster from the vast troves of data supplied by IoT sensors.
AIoT leader SAS has used this technology both in the automotive and aerospace industries, using AI-enabled remote sensors for early detection and automatic diagnosis of impending part failures. In addition to reducing data cleanup times, applying AI to flight data has saved more than 1,400 hours of downtime over three months for its aerospace customer Lockheed Martin.
The Focus on Quality 4.0 Is Intensifying
Quality 4.0 applies the digital transformation tools of Industry 4.0 to quality challenges to improve reliability and performance. LNS Research has written extensively about Quality 4.0, noting that the field has matured to the point that it’s now a top use case for Industry 4.0.
Examples of how manufacturers at the forefront of this trend are leveraging digital transformation for quality improvement include:
- Using predictive quality analytics to forecast changes in production quality
- Equipping new products with sensors to monitor quality for improving new product introduction (NPI)
- Using AI to automatically detect out-of-specification material and make corrections
- Leveraging automated software to verify conformance to standards and analyze sources of process failures in real time
AR and VR Will Be Key to Bridging the Skills Gap
A 2018 report by Deloitte and The Manufacturing Institute Manufacturing projects that 2.4 million manufacturing jobs will go unfilled by 2028. Not only does the retirement of baby boomers leave positions empty, it also means an influx of less experienced workers. In fact, U.S. Bureau of Labor Statistics data shows the average tenure for manufacturing workers today is just five years.
For companies, this means spending more time and money on employee training to ensure workers have the skills to do their jobs safely and effectively. Augmented reality (AR) and virtual reality (VR) headsets that provide interactive, step-by-step instructions and live feedback can help bridge this gap and get workers up to speed faster, reducing costs while improving productivity for manufacturers.
The result, according to Control Engineering, is 37% shorter training times, 75% less time documenting work instructions and a full 50% reduction in assembly time.
Another example would be having maintenance technicians use AR devices like smart glasses that display key data such as last service date and overdue repairs. GE Aviation, for example, uses smart glasses combined with WiFi-linked torque wrenches to ensure optimal bolt tightening during manufacturing and maintenance, reducing errors while increasing efficiency 12%.
5G Will Unlock New Possibilities for the Smart Factory
5G promises to be a catalyst for digital transformation by combining ultra-reliable low-latency communication (URLLC) with connected devices in the manufacturing environment. However, extra hardware like signal boosters will be required since 5G’s high speeds come with a tradeoff of lower wavelengths that can’t penetrate walls.
As things stand today, many plants have spotty WiFi, making offline functionality essential for using digital tools like mobile plant floor audit software. As 5G continues to roll out to new areas, we should see this technology spark the next wave of Industry 4.0 adoption.
At the same time, concerns over intellectual property risks on the plant floor continue to grow. Manufacturers, especially those contracted with the U.S. government, can reduce risk by partnering with software vendors that offer enhanced cloud security through Amazon’s GovCloud platform and fedRAMP compliance.
Diving into Industry 4.0
Customer standards are vastly more demanding than they were even five years ago. Growing manufacturing complexity and the acceleration in digital transformation mean manufacturers must work harder than ever to meet customer expectations of perfect on-time delivery and zero defects. And while Industry 4.0 technology clearly holds the key to solving quality problems, many companies have yet to start on this mission-critical journey.
The challenge of Industry 4.0 is not just that it involves new capital investments. It also requires manufacturers to become experts in digitalization, which is a tall order for organizations that already must be experts in a wide variety of manufacturing processes. Fortunately, manufacturers can achieve the benefits of digital transformation with user-friendly quality software that provides deep insights on demand to drive improvements in plant performance.
It’s easy to recognize that pursuing digital transformation holds significant promise. It’s another challenge altogether to actually execute on these initiatives. The most important thing is to get started somewhere—even if it’s just a pilot project—making adjustments as you learn and grow.