Using Layered Process Audits to Close the Loop on Safety
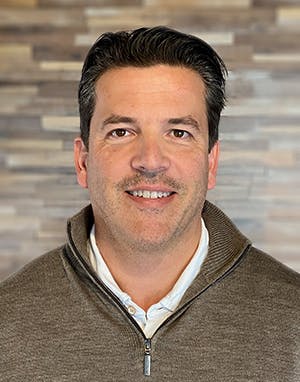
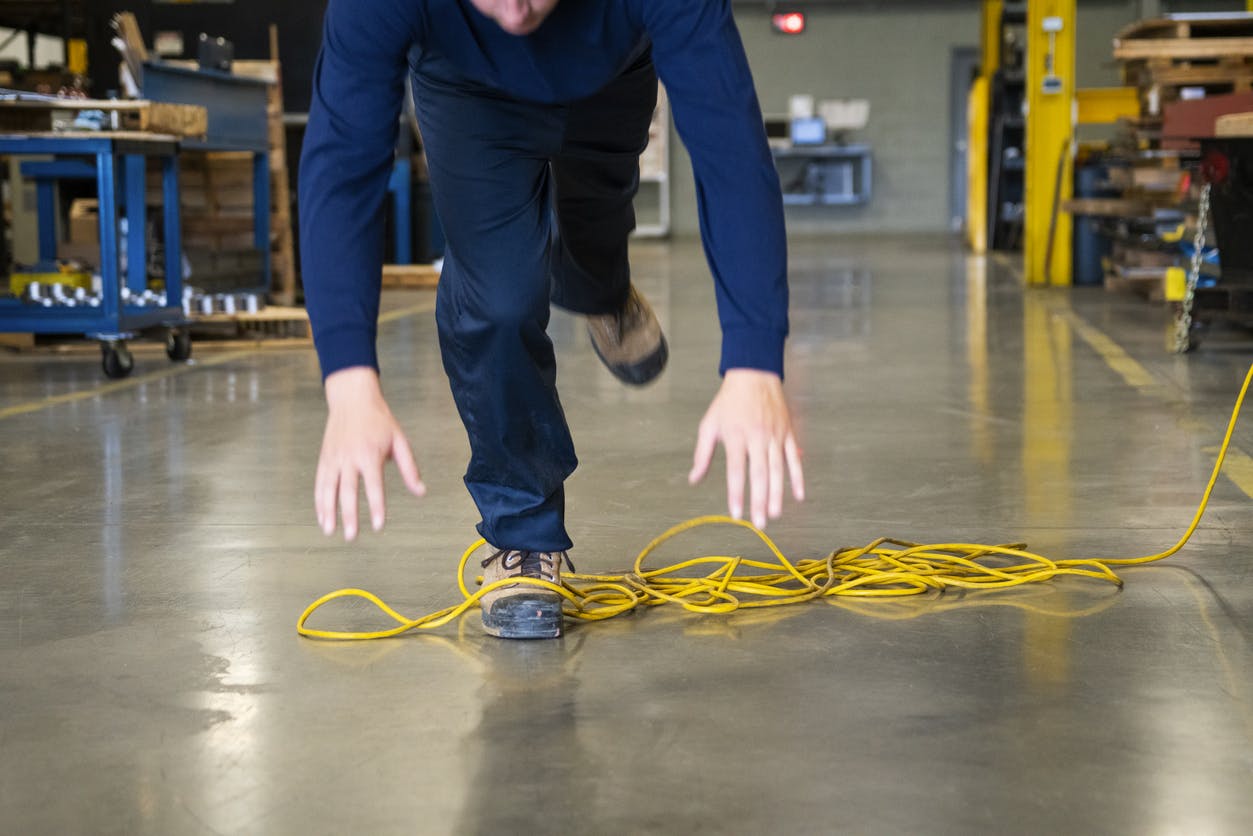
According to the National Safety Council, the rate of preventable workplace fatalities per 100,000 workers has flattened or risen slightly since 2009 after decades of steady improvement in occupational safety.
Companies conducting layered process audits (LPAs) can help get the United States get back on track reducing workplace fatalities by conducting daily checks to help identify safety nonconformances and fix them before they cause safety incidents.
With daily checks of high-risk processes, layered process audits lead to more conversations about safety, also demonstrating leadership prioritizes safe work—both critical to creating a culture of safety.
Achieving this level of reliability, however, doesn’t happen overnight. Organizations must first make a key mindset shift, also taking a strategic approach to uncovering and resolving instances where people don’t follow standards.
Download our free LPA checklist template for quick ideas on getting started with LPAs
The Quality-Safety Link
Quality and safety may occupy two different departments in the average manufacturing organization, but the reality is that safety is itself an aspect of quality.
For instance, it’s unlikely that an operator who is careless about safety procedures is going to pay close attention to job instructions, just as someone who is lax about quality is also more likely to be involved in a safety incident. Conversely, when people are focused on doing things right, they’re more likely to follow both quality and safety standards.
And ultimately, taking shortcuts doesn’t just put product quality at risk. Any time someone isn’t operating to standard, there’s the possibility for danger. This simple fact underscores a clear imperative for manufacturers: to improve quality, you also must also focus on safety.
Writing Safety-Focused LPA Questions
It’s not uncommon for manufacturers that conduct LPAs to devote a section of checklist questions to safety. One common mistake is having overly simple or generic questions, something that’s also a problem when it comes to writing quality-related LPA questions.
For instance, asking whether an operator is wearing safety goggles doesn’t add much value. Everybody knows they need to wear goggles. Instead, it’s important to drill down into more specific issues relevant to the work area, such as:
- Are there any tripping hazards in the work cell?
- Is there any guarding missing from the machine?
- Is the operator wearing arm guards, and are they comfortable?
There are lots of places cross-functional LPA teams can get ideas for questions. First and foremost, you want to look at previous safety incidents and OSHA findings. Near-misses are also an important source of questions and are essential to look at in terms of taking a proactive approach to preventing problems. Observations of unsafe behaviors, perhaps logged as part of a behavior-based safety program, can provide other good ideas for questions.
Finally, you want to make sure you’re adding questions from corrective actions related to all of the above, so you can be sure you’re sustaining your gains.
Ensuring Safety Problems Are Fixed
A closed-loop corrective action process is critical to protecting workers from safety problems. This type of process requires:
- Linking safety nonconformances identified during audits to corrective action requests
- Making sure corrective action requests have all the information needed to resolve them effectively, including due date, who’s responsible, action plan and any visual data such as photographs
- Following up on corrective actions during management reviews to ensure safety risks don’t fall through the cracks
- Adding new questions to LPA checklists once corrective actions are complete to make sure people aren’t backsliding
Taking it one step further, companies must look at safety problems and ask where similar deficiencies might exist elsewhere in the plant. For example, if you receive an OSHA finding for a machine not being properly grounded, adding an LPA question related to machine grounding could uncover more instances of ungrounded equipment.
By providing the opportunity to check on high-risk processes every day, LPAs can become a key tool for closing the loop on known (and as yet unknown) safety problems. Getting there means recognizing that safety and quality are one and the same, writing specific, relevant questions and instituting a corrective action process that doesn’t allow problems to snowball.