What the New OSHA COVID-19 Standard Means for Manufacturers
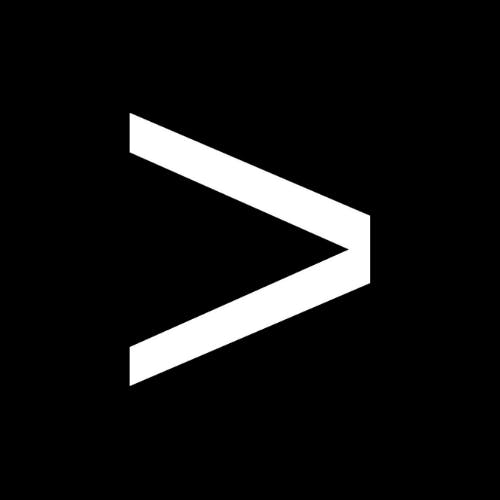
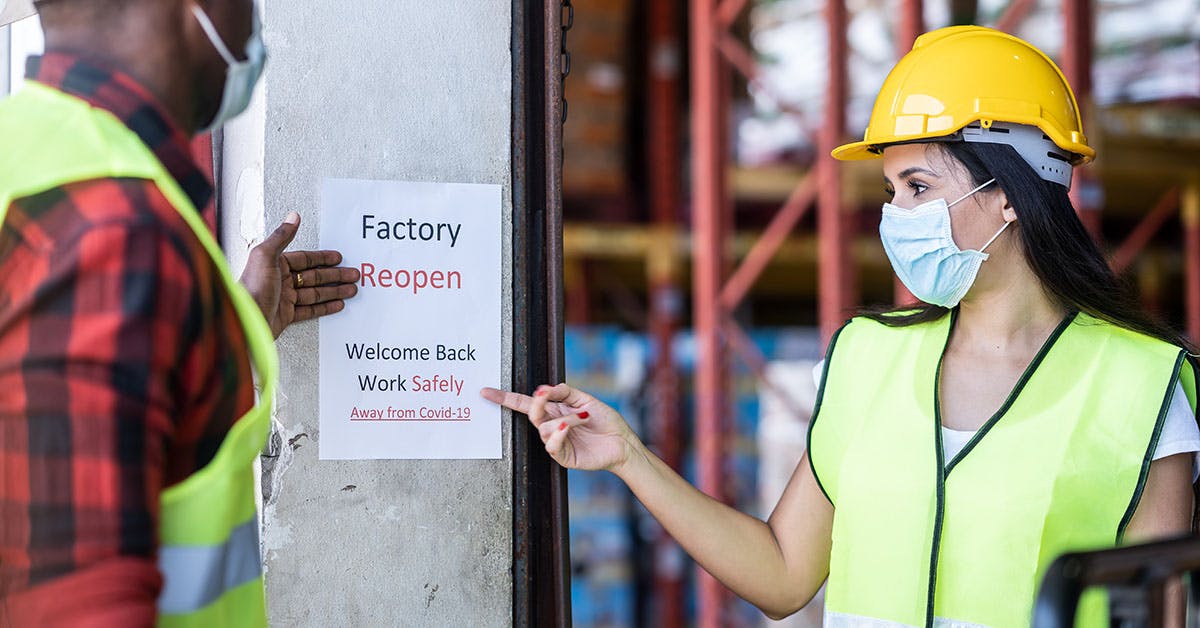
A new OSHA COVID-19 standard soon to take effect could have big implications for manufacturers and how they monitor plant floor safety.
In April, the U.S. Occupational Safety and Health Administration (OSHA) sent a draft emergency temporary standard on COVID-19 to the Office of Management and Budget.
The standard goes further than previous actions, putting new “shall” requirements in place as opposed to “should” recommendations found in existing guidance.
The new OSHA COVID-19 standard is the latest move aimed at strengthening protections against coronavirus transmission in the workplace, but many manufacturers are uncertain of the standard’s impact on operations and regulatory risks.
Within this context, today’s post examines what the new standard means for manufacturers and how to use short, simple checks on the plant floor to help ensure compliance.
New OSHA COVID-19 Standard Timing and Context
Previous OSHA guidance was released in 2020 clarifying steps employers should take to prevent the spread of COVID-19 in the workplace. In early 2021, the new administration directed OSHA to update this guidance, as well as to consider drafting a new COVID-19 standard and step up enforcement and outreach.
In March 2021, OSHA created the COVID-19 National Emphasis Program (NEP) to help reduce risks to workers in high-hazard industries and work processes through outreach, compliance assistance and inspections.
The Department of Labor sent the new OSHA COVID-19 emergency temporary standard to OMB on April 26, 2021. Discussions of the proposed rule were scheduled through May 5 between the administration, unions and business groups.
Once the review is complete, the new standard will immediately go into effect for up to six months, at which point it will be replaced by a permanent standard.
What to Expect from the New OSHA COVID-19 Standard
The actual content of the OSHA’s COVID-19 standard hasn’t been released yet. However, the National Law Review reports that the standard may include different rules for different industries, with requirements in areas such as:
- Developing a written COVID-19 prevention plan
- Providing masks to employees
- Ensuring social distancing in the workplace
- Cleaning and disinfection protocols
- Worker training requirements
Virginia and California have already issued their own COVID-19 prevention standards, which may provide some insight on what manufacturers can expect to see in the new OSHA standard.
Manufacturers have had to negotiate requirements in these areas in the course of returning to work over the past year, but ahead of the release of the new standard, leaders should be planning for the changes that they may need to make. For example, ensuring social distancing with a full staff may require more shifts or even a redesign of the plant floor. Likewise, new training requirements mean planning for increased downtime. Preparing for any disruptions to existing processes is the key to adapting quickly to the coming changes.
Current OSHA Compliance Requirements Still in Place
For manufacturers who meet the requirements for a high-hazard workplace under OSHA’s COVID-19 NEP, prevention is critical to reducing health and regulatory risks.
Until the new OSHA COVID-19 standard is in place, manufacturers are still subject to inspection and enforcement under the COVID-19 NEP. That means they should follow current CDC guidance as well as comply with applicable OSHA standards.
The most basic of these is the General Duty Clause, which requires employers to provide a workplace “free from recognized hazards that are causing or are likely to cause death or serious physical harm.”
Other OSHA standards relevant to preventing COVID-19 in the workplace include:
- Respiratory Protection (29 CFR 1910.134)
- Personal Protective Equipment (29 CFR 1910.132)
- Sanitation (29 CFR 1910.141)
- Bloodborne Pathogens (29 CFR 1910.1030)
- Hazard Communication (29 CFR 1910.1200)
Why You Need to Verify and Document Compliance
While OSHA has come under fire for a perceived lack of enforcement of COVID-19 safety, that may be changing with the new administration. The agency handed out its largest fine to date within days of the NEP’s issuance, slapping a Massachusetts tax preparation firm with a $136,000 penalty for prohibiting workplace mask usage.
To avoid this type of enforcement action, companies should have a documented COVID-19 prevention plan that includes:
- A COVID-19 hazard assessment
- Controls identified to prevent transmission
- Documented evidence that your team is following the plan
It goes without saying that manufacturers will need to confirm that all of their facilities have an adequate system for assessing COVID-19 hazards and controls in place for preventing transmission. If there have been any confirmed transmissions at a facility, now is the time to revisit the incident reports to understand what work areas may have had a close contact occur and verify that the plans have been updated to prevent future transmissions in those areas.
One way to protect workers and document compliance is by using fast, frequent plant floor audits to verify safety measures such as PPE use, sanitation protocols and social distancing. Mobile plant floor audit software such as EASE makes this process simple, allowing companies to:
- Easily add or update questions based on evolving regulatory requirements
- Create custom checklists specific to the work area
- Require photo evidence to document compliance and demonstrate due diligence
Automation can help make safety plans more effective, but protecting workers ultimately requires going beyond basic compliance. Recognizing this fact is the first step towards reducing risks, both to the employees who depend on a safe workplace as well as to business operations as a whole.
Daily checks of safety controls place are critical, helping companies avoid compliance risks, take care of team members and minimize business disruption due to COVID-19 transmission.