Features to Look for in a Safety Inspection App: Report and Resolve Issues
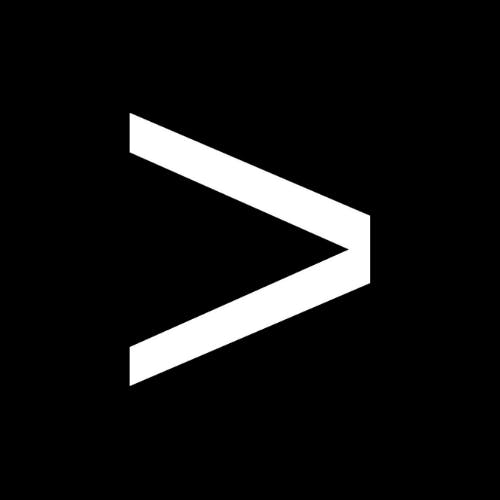
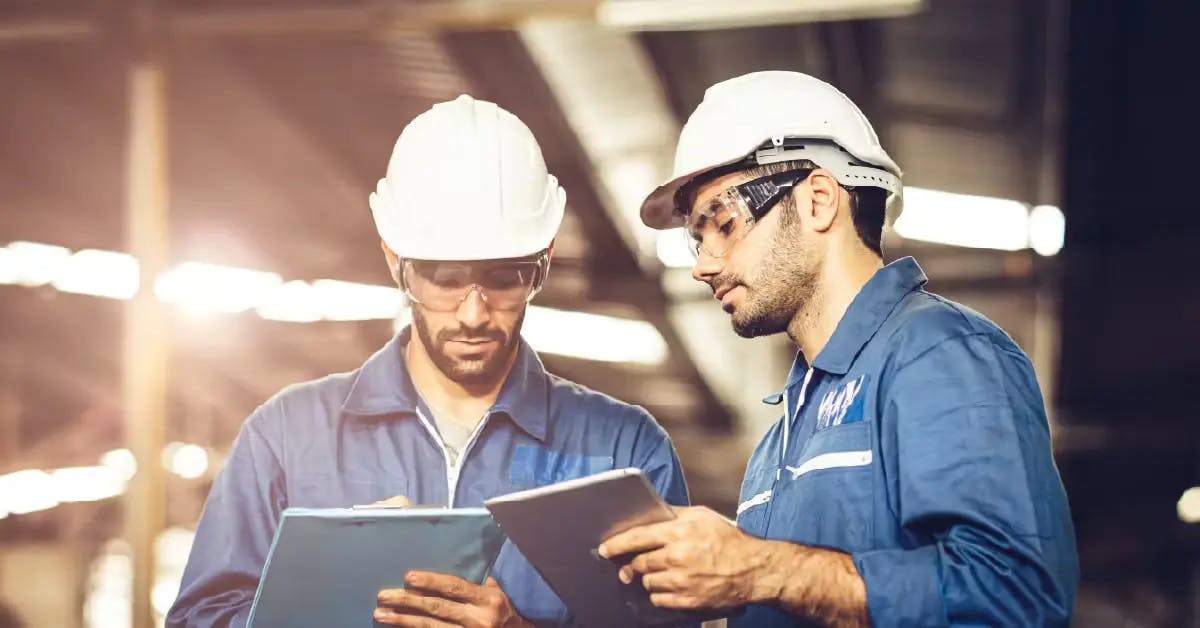
According to the U.S. Occupational Health and Safety Administration (OSHA), an average of 15 workers are fatally injured on the job every day. This is a sharp drop from the average of 38 when OSHA was created in 1970, yet it still leaves room for improvement.
While safety training is important, safety professionals recommend that you also monitor whether workplace safety protocols are followed by regularly conducting inspections.
Regular safety audits are essential for reducing incidents, risks and costs. Using a safety inspection app can help maintain compliance with relevant safety regulations, analyze trends, and provide insights to maximize results.
To help you choose the right mobile inspection app for your plant, we’ve put together a quick guide on what to look for and what to expect as you navigate the process.
Download your free Digital Safety Inspections whitepaper for more tips and best practices for reducing incidents with a safety and compliance inspection app
Read more on connected worker safety
Why Use a Safety Management and Inspection App?
A digital safety and inspection app provides several advantages over pen-and-paper inspections, including the ability to:
- Gather more and better data for making safety-related decisions, particularly around root cause analysis and remedial measures
- Quickly complete inspections on a mobile device instead of having to create, distribute and manually enter findings from paper checklists
- Customize checklists and questions to address a broad range of process-specific risks while keeping inspections short
- Add photos to inspection questions and findings to clarify safety standards and accelerate corrective action
- Create a closed-loop process for addressing findings and keeping your inspection program on track
These tools also help empower your workers to take proactive safety measures and promote a culture of accountability and collaboration.
Below, we examine these points more closely, also looking at crucial elements of setup and support when comparing software vendors.
Safety Risk Reporting and Insights
Real-time reporting and analytics are critical to developing leading safety indicators for proactively reducing workplace incidents. Here, you’ll want to look for key capabilities and safety data such as:
- Graphic outputs such as Pareto charts showing safety failures by work area and identifying trends over time
- Custom dashboards for different users, whether it’s a safety manager, plant manager or executive
- Non-conformance metrics to show where issues aren’t being closed out in a timely manner
Configurable Inspection Checklists to Support Compliance
Customizable checklists and questions are a key function to look for in inspection software. Instead of fixed inspection templates, look for inspection forms that can be tailored to the situation, to give you comprehensive inspections in less time.
Custom tags combined with question randomization are particularly helpful, allowing you to:
- Tag questions by work area, for example, to verify compliance with process-specific personal protective equipment (PPE) requirements
- Create randomized lists to cover a broad range of workplace safety standards
- Rotate in questions related to known hazards or previous incidents
Conditional questions are another feature that can help capture more detail when an inspection reveals a safety issue or potential accident risk.
Inspection Photos
When evaluating workplace safety apps, consider a solution that allows you to add photos to questions and findings. This capability saves time and improves results by making it simple to:
- Include photos of what is and isn’t acceptable, so auditors can quickly spot when conditions don’t meet safety standards
- Require a photo to be included with the inspection report to verify that it took place
- Upload photos of inspection findings to accelerate corrective action, providing a clear visual of the problem rather than a lengthy written description
This visual observation tool makes inspections more effective and actionable.
Request a personalized EASE safety demo today!
Closed-Loop Scheduling and Issue Mitigation for a Stronger Safety Program
An effective safety program goes beyond merely answering questions and checking off items on a list. To reduce incidents, implement a closed-loop process to ensure inspections are conducted, and issues are promptly addressed for continuous improvement. Therefore, scheduling and resolving issues are vital tools to assess and utilize.
What should plants be looking for here?
- Utilize automated scheduling to quickly develop your safety inspection plan.
- Implement email reminders and notifications to help individuals stay on schedule with their assigned inspections.
- Enable the capability to document immediate mitigations or initiate comprehensive corrective actions when further investigation and additional steps are required.
Intuitive App
Choosing a safety inspection management software that people actually want to use is essential to success. If it’s not an easy-to-use solution, people will avoid using it. That means fewer inspections, less data and lower overall value from your investment.
Look for a platform where usability, visibility, and productivity are top priorities. The right software allows your team to complete inspections quicker and capture more useful data.
Setup and Support of Workspace Safety and Mobile Apps
Two final elements to consider when looking at safety reports inspection apps for inspection are setup and support processes. The vendor you choose has a significant impact on the ultimate success or failure of your implementation, so you’ll want to ask questions like:
- What do customers say about the vendor’s support?
- How long does it take to get a response to a question?
- Does the vendor incorporate user feedback into the platform?
- What is the typical implementation time?
- Does the vendor have a streamlined process for getting your program up and running?
- Do they provide ongoing training and office hours to make sure you’re getting the most from the app?
Our Final Thoughts On Safety Audit Software
Digital apps for safety reports inspections can help you complete more plant floor checks and generate more data to improve safety. Avoiding even a single incident can deliver a significant return on investment (ROI), but you need the right tools to make that happen. A configurable, intuitive platform backed by robust support is key, fostering buy-in while ensuring that the app fits your plant’s unique processes and needs. When your team members are equipped with a solution they trust, they are more likely to excel in maintaining compliance and keeping safety and compliance a priority.