What’s Missing from Your 5S Audits?
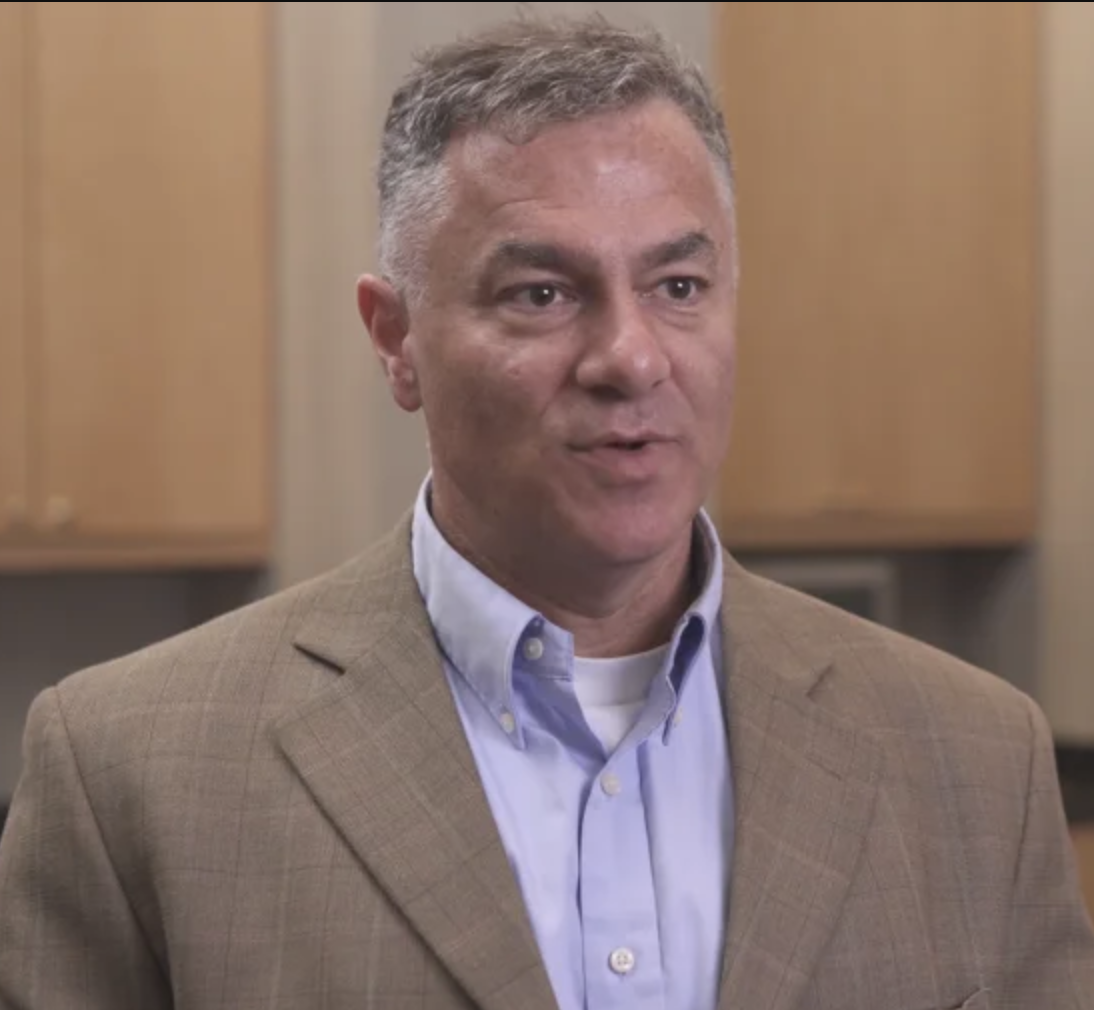
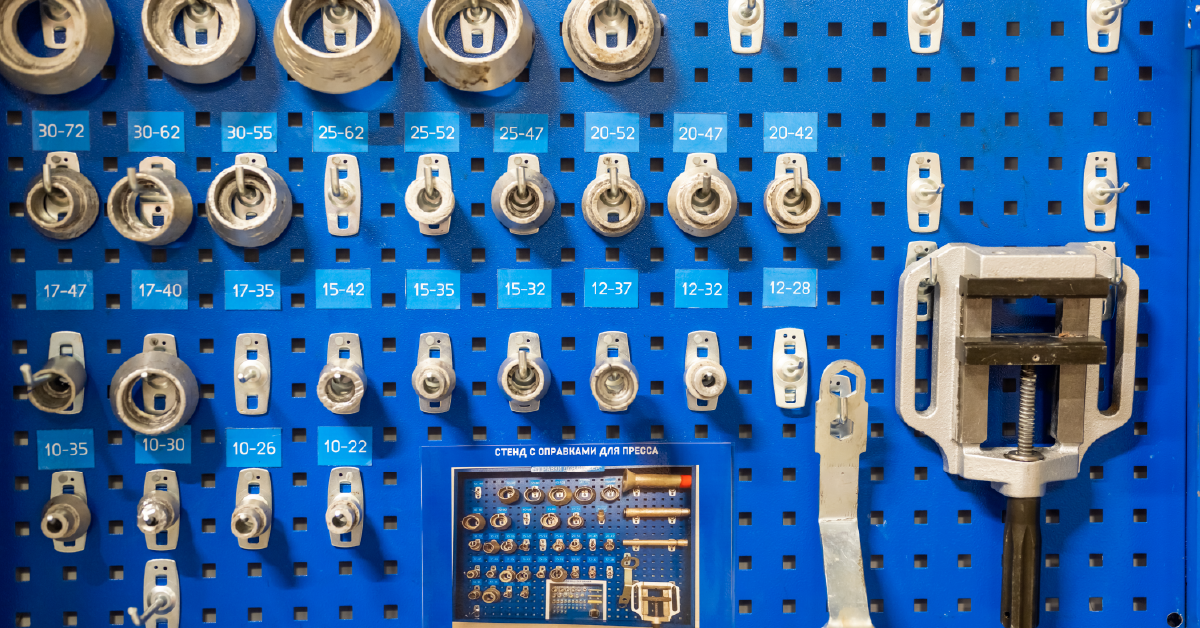
The 5S approach to workplace organization can help streamline workstations to minimize errors, but are your 5S audits helping you ensure that you sustain your gains and continue to meet your quality goals?
Just as important, could the 5S process itself be introducing new risks into your plant?
The problem many organizations have with 5S is that they can’t see the forest for the trees, focusing on details at the expense of the big-picture perspective.
To help manufacturers get more from their 5S efforts, we explore some commonly overlooked problems with 5S, including the one element you need for 5S audits to work.
Get more plant floor audit best practices and strategies with our free Ultimate Guide to LPAs.
Timing of 5S Audits
One of the biggest mistakes we see our clients make is when plants do their 5S audits at the end of the shift. That means when an audit does find a missing tool or a safety hazard, an entire shift goes by before the problem is identified.
The result is increased risk, compared with using 5S audits at the beginning of a shift to check whether the workstation is set up correctly. One way to do this is to incorporate 5S questions into layered process audits (LPAs), which focus on verifying high-risk process inputs on every shift. Layer 1 auditors should be encouraged to perform their audits early, as well as subsequent auditors. This not only catches variations from the standard early, it communicates by action the importance of the audits. We do them early to ensure they are done and commit to quickly resolving any findings. This is akin to having a pre-flight checklist completed before take-off of an airplane, compared with trying to address problems when you’re already in mid-air.
Workstation Items
When trying to identify gaps in your 5S audit program, another common issue to look at is whether there is anything missing from the workstation. The Seiri (sort) step of 5S helps eliminate what you don’t need at the workstation. However, it’s critical to go back to check all the basic tools are still there.
It’s easy to see if there are too many materials in a work area, but it’s harder to identify when things are missing. One 5S tool that can make this easy to see is shadow boards showing where all tools should be stored, making it easy to pick out missing items. The 5S audit can then come along and quickly do a check for all tools being present.
Labeling Issues
As part of the Seiton (set in order) step of 5S, all materials in the work cell should be labeled correctly and located in the correct place. Why is this so important? Because if an operator reaches for a panel and instead grabs a bracket, the result is a nonconforming assembly. Setting operators up for success requires setting up the workplace for success, and the key is having everything where operators need it to be.
That means that 5S audits need to look at whether parts are labeled correctly and all the right parts are in the right place per the work cell layout. It’s important here not just to check paperwork, such as by asking whether the work cell layout is posted. A posted piece of paper does not tell us anything about the reality of our manufacturing. For audits to work, they must check the process—not the paperwork!
Safety Hazard Identification
A lot of manufacturers are adding a sixth element to 5S focused on safety. Safety is a foundational element of quality, since operators are unlikely to do high-quality, defect-free work while working in an unsafe environment—and the reverse is also true.
Plants recognize that safety should be part of everything they do, and this is an important consideration within the context of 5S. For example, in an effort to clean up the work cell, have you put heavy parts up high that could fall on the operator? Again, 5S can help make a cell neat and tidy, but you need to verify that the process itself hasn’t introduced new risks.
Sustaining 5S Audits
The fifth step of the 5S process is Shitsuke (sustain). Without this key element, the rest of your 5S efforts won’t matter, because 5S must be consistently held in place to actually work. 5S is a culture, not an event. Within this context, daily process audits like LPAs play a crucial role in sustaining 5S practices. People will respect what we inspect.
When starting out with 5S audits, many plants often use them as standalone audits. Over time, however, plants may incorporate 5S questions into LPAs. It’s particularly true at the supervisor or Layer 1 level. Here, supervisors don’t have enough time to complete separate LPA, 5S and safety audits. However, it is the high frequency and the fact that these people have intimate knowledge of the process that make these some of the most valuable audits. Layer 1 auditors are the ones most likely to catch variation from the standard, whereas other layers promote accountability and communication.
Instead, an LPA platform like EASE lets you incorporate multiple question types into a short ten-question audit, including 5S and safety questions by using question tags or categories. For example, an LPA checklist might include three questions each focused on safety and 5S, with four questions reserved for process verification. Rotating and randomizing these question tag categories means you’ll cover a broader range of risks, helping hold in place quality, safety and 5S standards.
Far too many organizations treat 5S as a one-time event. For it to be successful, however, it needs to be an ongoing process. LPAs are the best tool for sustaining that process and refining your process in the pursuit of continuous improvement.
One thing that LPAs and 5S share in common is that they are culture tools. They only work if the executive and management levels of the organization demonstrate commitment to them by their actions. Doing LPAs reinforces the 5S changes and give operators the opportunity to communicate further opportunities for improvement to plant leadership.