Why Manufacturers Should Focus on Quality During Tough Economic Times
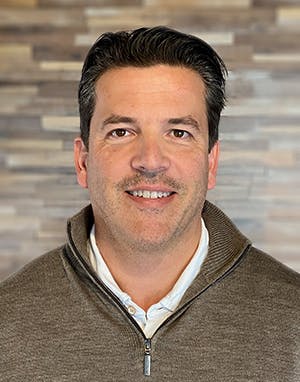
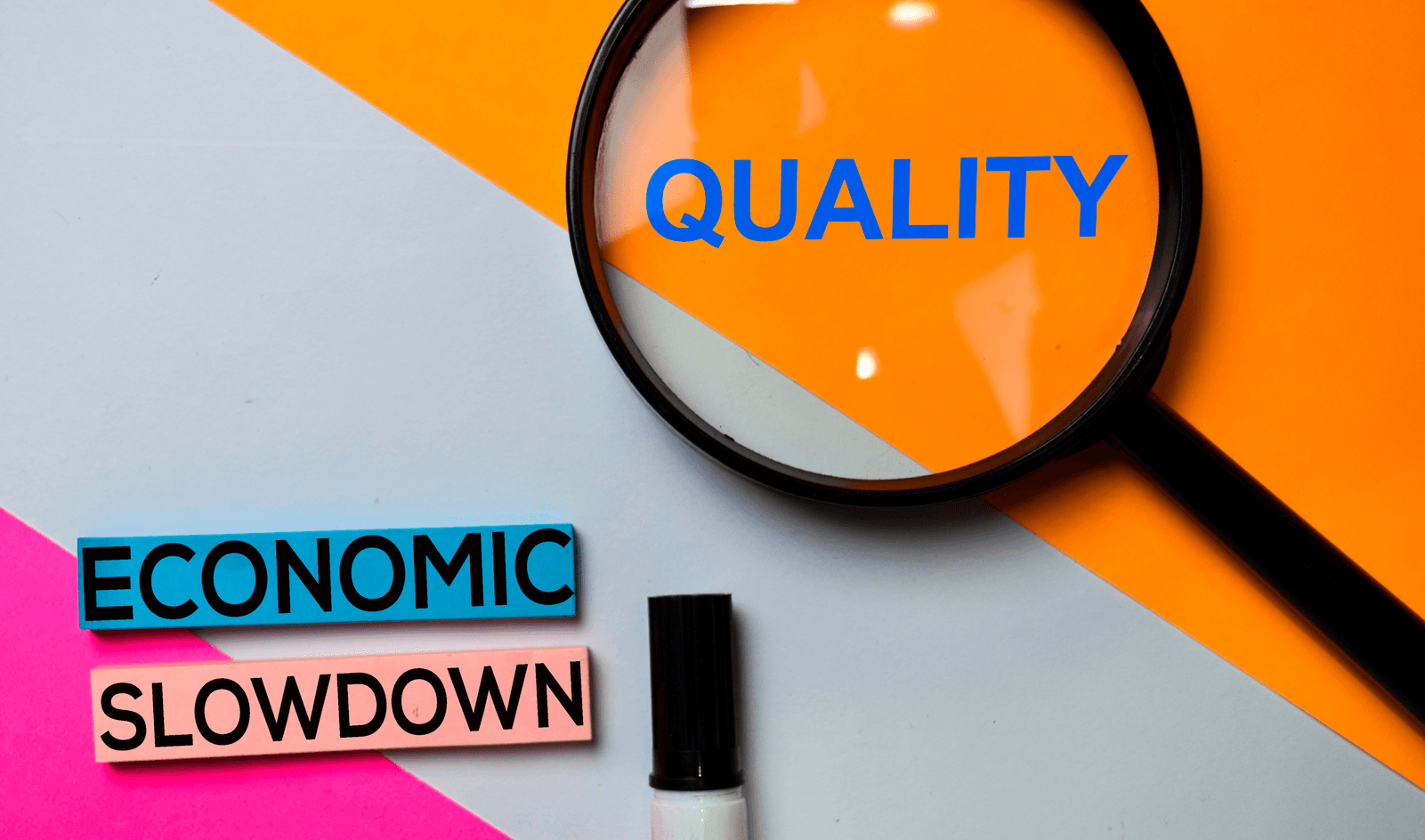
Facing difficult choices, a focus on quality in a recession could mean the difference between thriving and getting left behind. For proof, we need look no further than the origins of quality management as we know it today.
The success of quality management experts W. Edwards Deming and Joseph K. Juran overseas proved that quality drives significant returns, at a time when their theories struggled to gain traction in the U.S.
Since then, we’ve seen time and again that investing in quality pays off, and that doubling down on quality during an economic crisis can help insulate against its worst effects.
Here we look at the quality-profitability link, how to build resilience under difficult economic conditions and how suppliers can leverage layered process audits to satisfy and even delight customers.
The Secret to Profitability in Tough Economic Times
The cost of quality—roughly 15-20% for most organizations, according to the American Society for Quality (ASQ)—is too high even in prosperous times. In times of recession, that cost is simply unacceptable.
For some manufacturers, scrap and rework cost up to 2.2% of annual sales, according to the American Productivity & Quality Center (APQC), while Warranty Week data shows warranty claims totaling as much as 2.7% of sales in certain industries.
If your company generates $100 million in revenue annually, that could mean losing $5 million in scrap, rework and warranty claims. The real cost is much higher when you consider hidden costs that aren’t accounted for in that $5 million, including loss of productivity and wasted money due to inefficiency.
Push production defects down by even 10%, and that immediately adds $500,000 to the bottom line in the above scenario. What’s more, it allows companies to grow revenue because they are wasting fewer resources on bad products, instead shifting them to manufacturing more products that customers actually pay for.
The result: increased productivity, production capacity and sales, all of which add directly to revenue that can be otherwise difficult to grow in the face of economic headwinds.
Quality Breeds Corporate Resilience in a Recession
Multiple studies have found a relationship between quality management and corporate resilience.
One UK study noted that robust communication, detection of change and rapid decision-making add up to better ability to overcome challenges. Another research paper focused on recession recovery strategies found that quality management is an integral part of how successful companies withstand economic trouble. Other insights from the paper’s review of quality literature include:
- Quality management issues can lead to corporate collapse, according to a survey of 120 companies
- Cost control strategies alone aren’t enough to gain a firm footing during and after a recession
- Strong companies will exploit opportunities to disrupt weaker competitors
- Teams that act strategically can expand market share during an economic downturn
- Long-term survival requires allocating more resources to quality analysis to find areas of potential improvement
- Given that it’s up to seven times cheaper to retain a customer than it is to acquire a new one, investing in customer satisfaction is an important part of reducing costs
Standing Out as a Supplier
There’s no question that in a recession, many companies tighten their belts and reevaluate relationships with suppliers. Some will ultimately get squeezed out, and companies with a history of quality problems can expect to find themselves in the hot seat.
Within this context, having a reputation for quality can literally make or break a business. In times of economic uncertainty, successful companies are those that focus on the core of quality management: satisfying and delighting customers.
For automotive suppliers, that means taking appropriate steps to prevent production defects, leveraging quality tools such as layered process audits (LPAs) to:
- Proactively identify potential sources of quality risk based on audit findings
- Ensure multiple levels of verification for high-risk processes and known problem areas
- Fix problems permanently to avoid recurrence and customer frustration
LPA software like EASE can help manufacturers build reliability into LPAs, ensuring accountability while providing hard data to improve customer satisfaction in the long run.
As a side note, in a world of global supply chains, your customers are likely not just going to be looking at your quality track record but may have questions as to how you are managing COVID-19 risk too. Having to shut down a manufacturing plant due to a coronavirus outbreak could be equally damaging to customer retention as quality issues. Therefore a solution for automating all of your plant floor audits including LPAs and COVID-19 audits is even more critical.
In tough economic times, it’s a natural reaction to want to trim the sails. The COVID-19 recession is no different. Many companies, particularly automotive and aerospace manufacturers, face difficult choices that will dictate how they weather this storm.
Quality is more important than ever, with research showing companies that focus exclusively on cost-cutting measures are ultimately putting their future at risk. That’s because quality is not a cost, but an investment that brings significant returns in terms of improved efficiency, competitiveness and corporate resilience.
Companies that fail to invest in quality in a recession do so at their own risk. As they fall further behind due to quality problems that arise from short-term cost-cutting, competitors who value quality claim an increasing proportion market share. The result: laggards are sidelined, while leaders see accelerating gains and are positioned for even bigger growth during economic recovery.
It’s a strategy that paid off for Japanese manufacturers in the later part of the 20th Century, and one that we’re likely to see repeated in modern times as well.