Will Quiet Quitting Affect Quality and Safety?
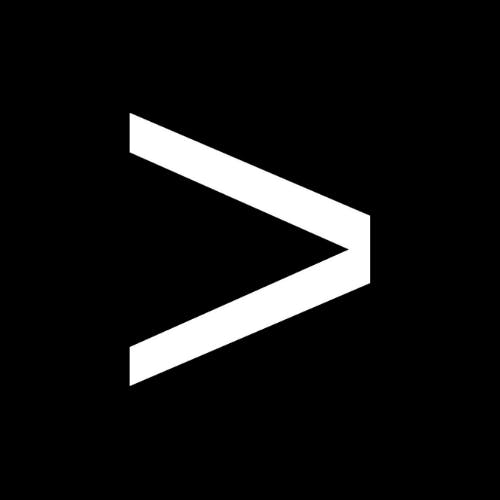
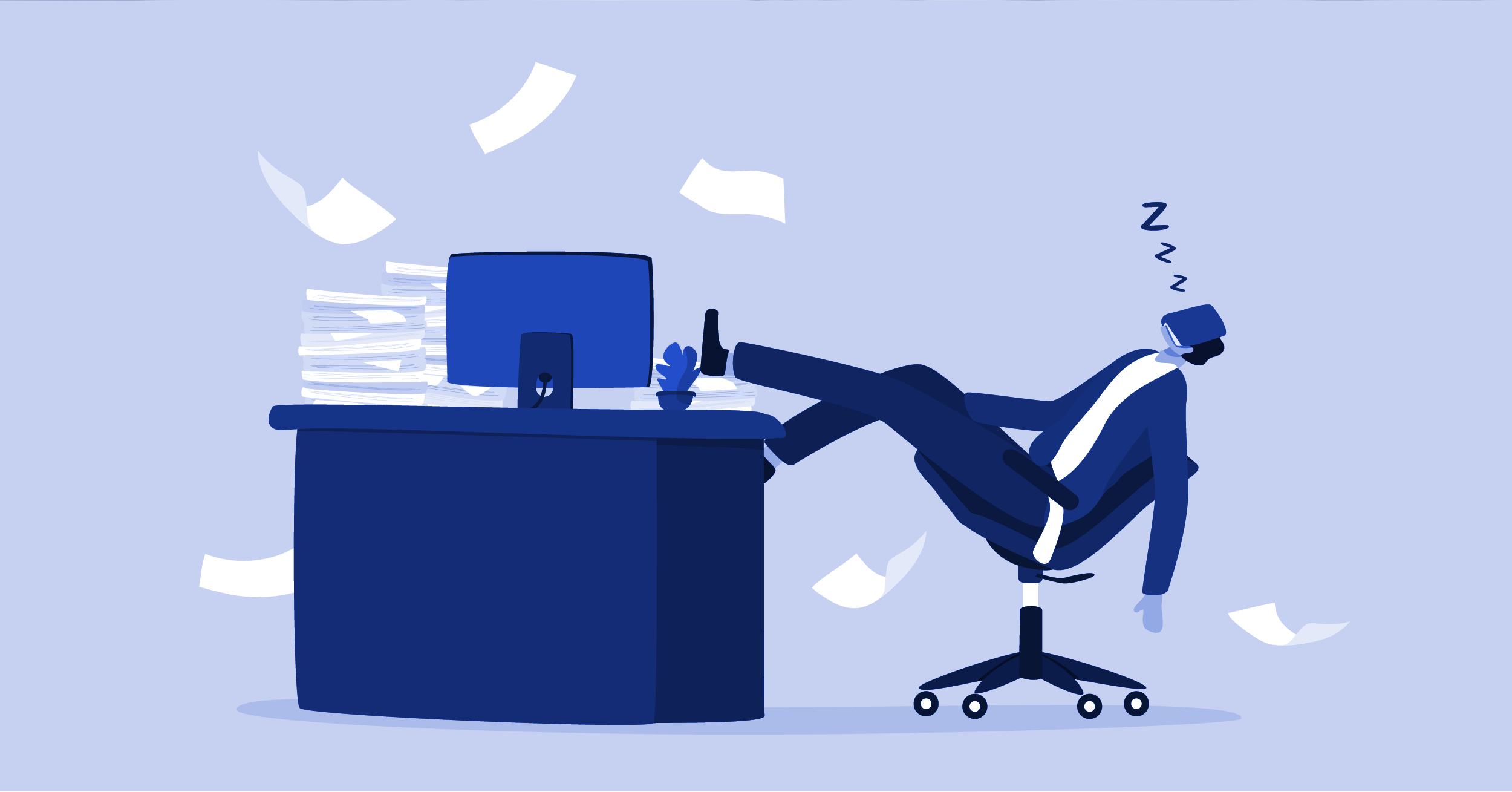
A recent Gallup poll revealed at least 50% of the U.S. workforce is quiet quitting, a trend defined as being psychologically detached and doing the bare minimum at work.
In the manufacturing industry, this trend raises important questions: how does employee disengagement impact quality and safety, and how can companies address the problem?
Today we’re looking at quiet quitting in the context of manufacturing quality and safety, and how manufacturers can use plant floor checks to minimize its impacts.
Download a free whitepaper on Why and How Digital Safety Inspections Help Manufacturers Work Safer
Quiet Quitting: A Productivity Risk or Just Work-Life Balance?
Quiet quitting is another way to describe disengagement, which creates problems when extra effort is required to come up with solutions or ensure customer satisfaction.
What should be troubling for companies today is that the number of actively disengaged employees rose 18% in the second quarter of 2022. What’s more, the decline in engagement started in the second half of 2021, around the same time companies began losing many experienced employees to the Great Resignation.
Some employees who have been sharing their experiences on social media say they’re just setting boundaries to create better work-life balance. It’s not hard to see why, especially in an era where many are expected to work nights and weekends. Others report taking a step back due to lack of opportunities or recognition in the workplace.
For their part, many companies are concerned about quiet quitting causing a loss in productivity. In fact, another report by Gallup cited $7.8 trillion in productivity lost worldwide in 2021 due to disengagement.
Quiet Quitting, Quality and Safety
When examining the implications of disengagement, there are several factors that manufacturers should consider:
- Details matter: Maintaining high quality standards requires focus and attention to detail. When operators just phone it in, they’re likely to miss things like quality alerts, changes to work instructions or the need to perform an operation in a specific way.
- Employee safety is at risk: Research shows a strong correlation between employee engagement and safety attitudes. Anytime people aren’t actively focused on what they’re doing, safety incidents are more likely to occur. Safety problems can also contribute to employee turnover, further worsening labor shortages.
- Managers need help: The Gallup survey shows just one in three managers are engaged at work, pointing for a need for company leadership to find ways to better engage this group.
- Conversations are critical: Researchers say the most useful habit for minimizing disengagement and burnout is for managers to have one meaningful conversation weekly with each team member.
Using Plant Floor Checks to Mitigate the Effects of Quiet Quitting
Given what we know about quiet quitting, manufacturers should examine ways to combat disengagement and the potential effects on quality and safety. Plant floor checks are one potential strategy to help maintain standards while boosting employee engagement.
According to Gallup, the decline in engagement relates to problems with unclear expectations, not feeling cared about and a lack of connection to the organization’s purpose. Plant floor checks such as layered process audits address these issues in several ways:
- Clarifying expectations: Checking in frequently to verify that operators are performing work to standard helps employees know that they are doing their job right.
- Showing respect: Being present on the plant floor, soliciting feedback and giving employees recognition shows them that the company genuinely cares about them.
- Commitment to quality: Taking the time to check that people are doing things right demonstrates an authentic commitment to quality. This is important for showing that that production isn’t prioritized over quality.
- Engaging managers: Quality isn’t something that happens in the office. It’s something that happens on the plant floor, and plant floor checks help managers go to where the work is done.
Quiet quitting is clearly a risk when it comes to protecting manufacturing quality and safety. Given current labor shortages and economic headwinds, companies need to find ways to address disengagement to ensure adherence to standards and minimize quality costs.
Plant floor checks are a relatively simple way to boost engagement, with mobile audit software like EASE helping make checks faster, simpler and more engaging. By verifying critical processes frequently, manufacturers can help minimize quality and safety risks while building a culture of engagement and communication.