A 3-Step Method for Writing LPA Questions
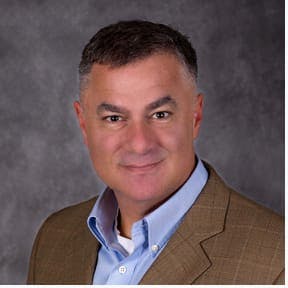
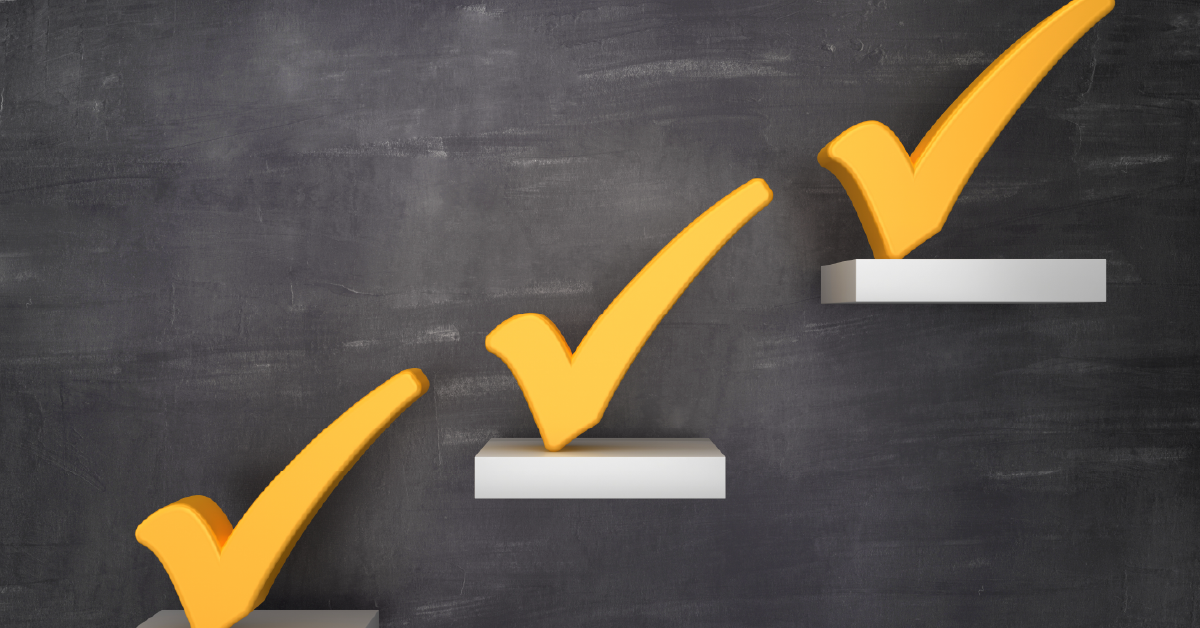
Layered process audits (LPAs) are a simple, cost-effective way for manufacturers to minimize defects, customer complaints and scrap costs. But when it comes to achieving real results with these fast, frequent plant floor checks, there’s one area where plants consistently struggle: writing LPA questions.
The problem is that, without effective LPA questions, these audits can quickly become an exercise in paperwork or just “checking the box.” Pencil-whipping is common, with people rushing through the questions without stopping to truly look at what’s happening in front of them.
The result is less visibility, less value from these audits and, ultimately, less buy-in from the entire team.
At The Luminous Group, we’ve developed a three-step process for writing LPA questions we encourage clients use to avoid these problems and get better insights into plant floor risks. In this article, we examine this process for writing questions and some examples and tips for putting it into practice.
Download your free Ultimate Guide to Layered Process Audits for more LPA question best practices, examples and tips
Stronger LPA Questions in 3 Steps
We often hear organizations starting with LPAs ask how they can generate an entire question library. In reality, it’s not as hard as it looks. The process we focus on with manufacturers follows a simple format where each question covers the three fundamental elements of what, how and why:
- What: Can the operator explain the step or process in question? This part is about naming the specific element of the process you want to evaluate and whether the operator understands it.
- How: Can the operator demonstrate the step correctly according to the work instructions, and how does the auditor know the operator is performing it correctly? This part should direct the auditor to a specific standard or criteria for evaluation.
- Why: Can the operator explain why this step is important to quality and/or safety?
This approach ensures you’re not just checking paperwork, compared with LPA questions that ask things like whether or not work instructions are posted. Questions designed in this way get to the heart of LPAs, helping verify whether those standards are actually being held in place on the plant floor.
Examples of How to Write LPA Questions
Let’s look at some examples of how to write LPA questions that incorporate elements of what, why and how.
Example #1: Specialized PPE
- Can the operator tell you the location of the black rubber gloves and boots that need to be worn in this area?
- Can the operator demonstrate how to correctly don and doff the personal protective equipment (PPE)?
- Can the operator explain why it is important to wear this specific type of PPE in this work area?
Example #2: Welding
- Can the operator explain the critical locations where to clean weld spatter from the work cell?
- Can the operator demonstrate how to clean the weld spatter according to the work instructions?
- Can the operator explain why it is important to clean the weld spatter in these specific locations?
Example #3: Equipment Setup
- Can the operator identify which gage on the machine must be checked prior to startup to ensure the correct water temperature?
- Can the operator demonstrate how they know the machine is ready for startup based on the standard?
- Can the operator explain why having the correct water temperature setting on the machine is important?
LPA questions should include details on why the item is being audited, giving the auditor and operator context on why it is important to quality and/or safety.
Other Key Elements for LPA Questions
As you write these questions, there are several elements you should consider incorporating into checklists. First, auditors should solicit feedback from operators, such as if they have a more efficient way to complete the process or if there are any specific barriers (such as uncomfortable PPE) that lead to a failed question.
Each question should also refer to a standard or clear criteria for verification. This is important because not all auditors will be experts in plant floor processes. Audit photos can help clarify what’s acceptable versus what is not, or to verify that an audit took place on the plant floor.
Finally, you need a way to initiate any mitigations that are required should an audit question fail. If you use automated LPA software like EASE, you can link failed questions to specific action items and responsible parties, as well as escalate issues to management.
With LPAs, the results you get are only as good as the quality of your questions. Using this three-step process, manufacturers can move beyond basic paperwork checks to look deeper into plant floor risks and verify that standards are actually being followed.