Behavior-Based Safety Questions for Your LPA Checklists
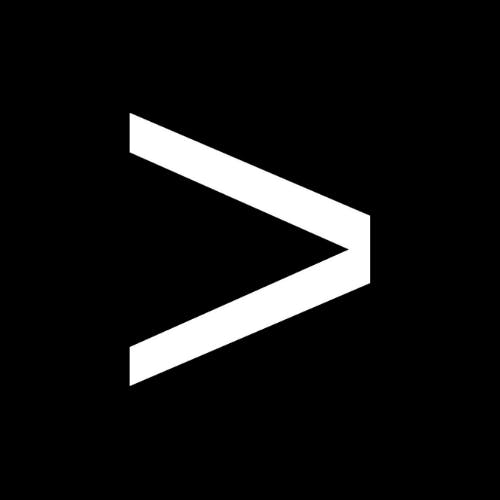
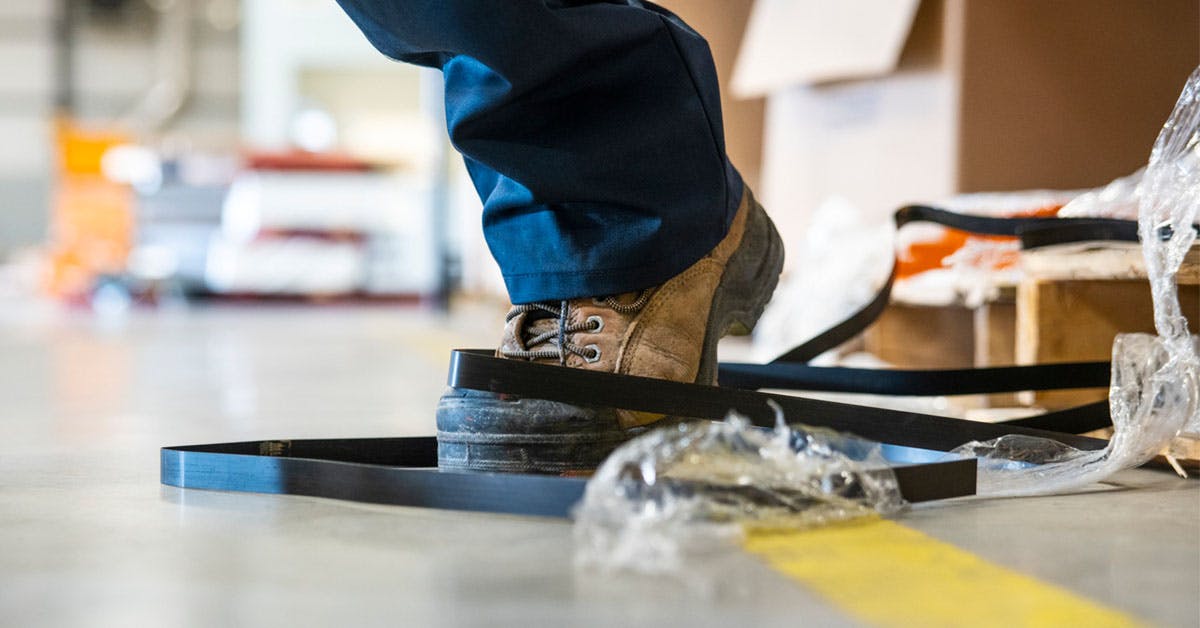
Behavior-based safety (BBS) is an approach to building a culture of safety that focuses on individual actions and changing habits.
The goal: reducing workplace injuries—which totaled 4.6 million in 2018 in the U.S. alone—by getting employees to take personal ownership of safety.
At the core of behavior-based safety is observing employees and providing respectful feedback when you see someone acting unsafely. Observation and feedback go hand-in-hand with layered process audits (LPAs), making BBS questions an ideal addition to LPA checklists. Let’s look at how and why to integrate BBS with LPAs, some sample questions and how to avoid a blaming approach.
Learn more about how LPAs work with our free eBook on Improving Production Quality with LPAs
Why Add Behavior-Based Safety Questions to LPAs
Layered process audits involve frequent audits of processes with a high probability or severity of problems. Sustaining a large number of audits—which is crucial to generating the data needed to spot underlying trends—means keeping audits quick. Ideally, these audits should take around 10 minutes.
LPAs often incorporate safety elements in checklists. For companies that use BBS, it makes sense to add BBS questions to your LPA question library, so you can collect ongoing data related to leading indicators such as:
- Personal protective equipment (PPE) usage
- Number of near-misses (accidents that almost happened but didn’t)
- Hazard reporting
- Safety participation
Behavior-Based Safety Questions for Your LPA Checklists
One best practice for LPA questions is to write them in yes/no format. “Yes” should indicate compliance, while “no” should require mitigation or corrective action.
The following are examples of BBS questions that meet these criteria, helping identify where safety risks might be lurking:
- Can the operator describe what steps of their job are critical to safety?
- Can the operator identify the hazards associated with the job as described in the job hazard analysis (JHA) or job safety analysis (JSA) form?
- Is the operator wearing the PPE listed in the work instructions?
- Can the operator describe how to report a hazard, near-miss or injury?
- Can the operator identify the exit route they should use during an emergency?
- If there has been an injury in the department, can the operator describe the cause and corrective actions associated with the incident?
- Are entrances and exits free of blockages?
- Is the work area clean and tidy?
If any of the above questions are answered with a ‘no,’ it’s important to look deeper and ask why. There may be a reason behind worker behavior that needs to be addressed. For example, lack of communication about safety issues could be why an operator is unaware of a recent injury in the department.
Questions to Differentiate Between Operator Error and Process Issues
One criticism of BBS is that it amounts to blaming the operator, which is a sure-fire way to hurt morale and get people to stop sharing observations.
The key comes down to identifying the correct root cause. If any question results in a no, you’ll want to dig deeper into why the condition occurred rather than just ascribing it to worker error.
LPA questions to help identify when process issues are contributing to safety problems include:
- Are machine guards present? Station setup is critical to identifying process errors that lead to safety incidents.
- Does the worker have tools available to assist with heavy lifting? Ergonomic injuries account for $1 of every $3 spent on workers’ compensation. It’s not always about how employees move, however. Sometimes they don’t have the right equipment.
- Is preventive maintenance up-to-date? Equipment can be a factor in safety incidents. You may want to require the auditor to take a photo to document evidence, rather than just asking whether preventive maintenance has been done.
- Can you verify there are no exposed or daisy-chained electrical wires? If there are exposed wires, are there enough electrical sockets to do the job?
- Are fire extinguishers, emergency eyewash stations, etc. working? If not, why not? Can you verify when they were last checked?
- Is the area free of slip, trip and fall hazards? Uneven flooring or other issues like a need for extension cords can contribute to falls, which are a top cause of workplace injuries.
Wrapping Up with Leading Questions
Some companies end LPAs with leading questions designed to get operators to open up and share issues they see. This feedback is also critical to BBS, so it’s worth asking leading safety questions and capturing responses in the notes field of your paper checklist or mobile audit software.
These questions could include topics such as:
- Is your PPE comfortable, or does it get in the way?
- Are there any hazards you’ve noticed that aren’t being addressed?
- What gets in the way of being able to do your job safely?
- What’s the one thing that needs to be done that would make your work safer?
- Do you feel like management is consistent about following up on safety problems?
If you want to build a true culture of safety, you must discuss the answers to these questions in management reviews and then implement solutions. If you don’t, people will see that you’re just paying lip service to safety, and they won’t bother sharing what’s on their minds.
BBS and LPAs share many similarities in terms of their approaches, creating an opportunity for manufacturers to integrate safety observations into these high-frequency audits. Focusing on employee behavior as well as the reasons behind it are essential, as is closing the loop on any identified problems.