Control Plan Update: AIAG Stresses Critical Role of LPAs
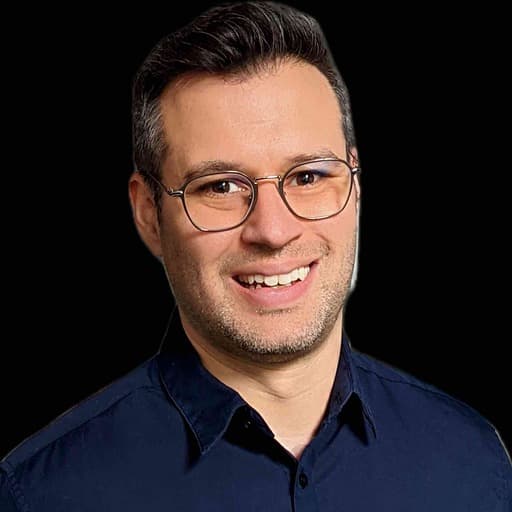
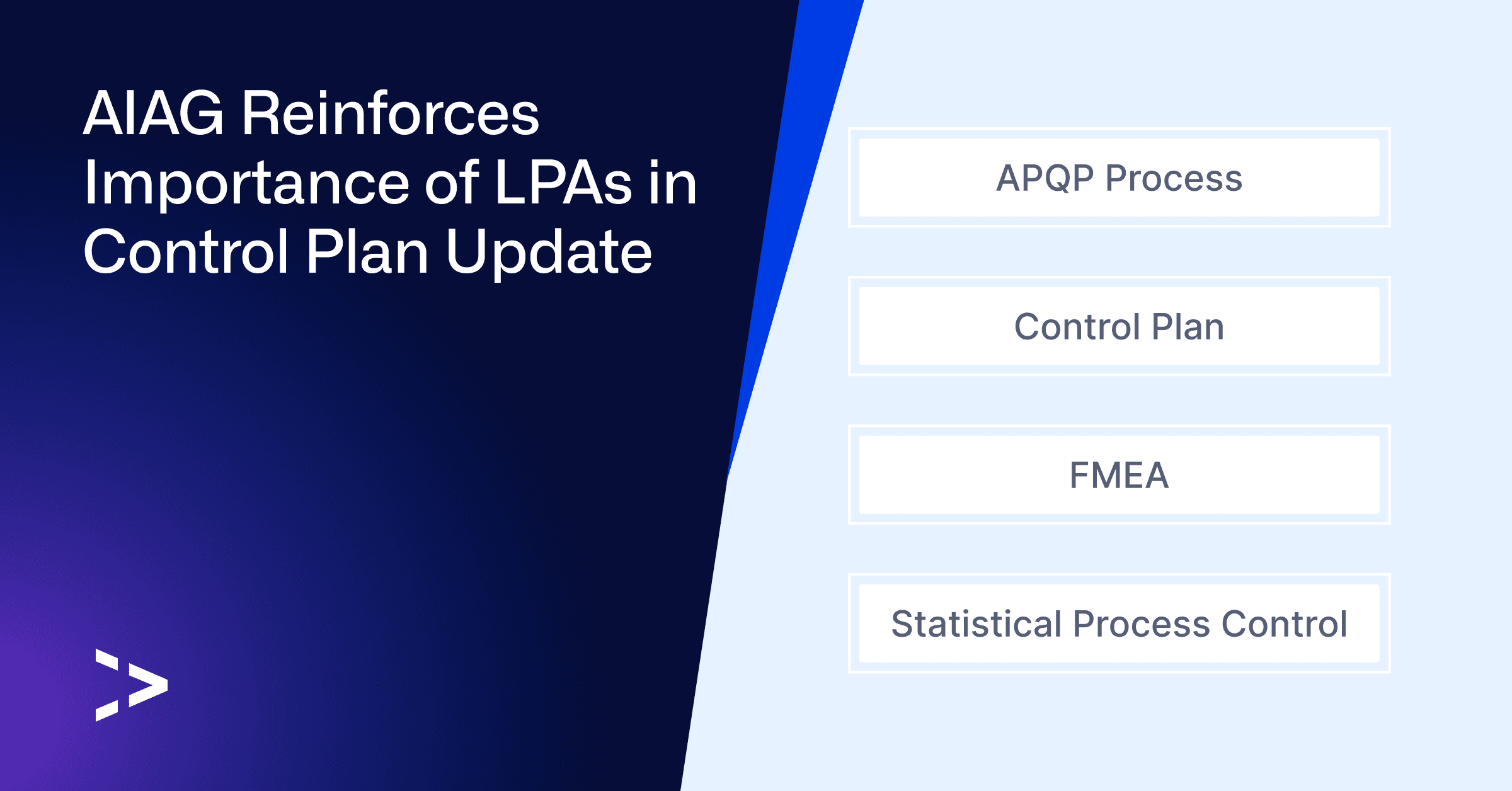
The Automotive Industry Action Group (AIAG) last year released its sixth quality core tool, the Control Plan: an important step-by-step manual used in automotive manufacturing to ensure product quality and consistency.
Control plans aren’t unique to the auto industry; in fact, it’s a major reference document for most manufacturers regardless of sector. The control plan is a key output of the broader Advanced Product Quality Planning (APQP) process, which aggregates common product development activities into one framework.
In automotive, all the major OEMs require implementing APQP, and suppliers use APQP to bring new products and processes to successful validation and drive continuous improvement.
Included in the AIAG Control Plan manual is a section (chapter 4.3) on layered process audits (LPAs) and its effective use as verification of control, with instructions on how to use LPAs.
AIAG already has recommendations specifically for LPAs in its comprehensive CQI-8 guidelines. However, by specifically calling out LPAs in the broader Control Plan manual, we believe the industry is doubling down on the importance of using high-frequency layered audits to provide ongoing process verification.
Get everything you need to know about layered process edits in our newly revised Ultimate Guide to LPAs
AIAG’s Six Quality Core Tools
AIAG’s Control Plan publication is the newest of its six quality core tools, which the organization describes as “the building blocks of an effective quality management system” and are required by most automotive manufacturers and suppliers. These practices are designed to improve sustainable, quality performance in the automotive supply chain and include
- Advanced Product Quality Planning (APQP): A framework for planning and executing product development processes, such as design reviews, process flow diagrams, and control plans to ensure their products meet quality standards.
- Control Plan (CP): A critical part of APQP that documents key requirements, process parameters, inspection methods, and reaction plans to maintain quality throughout production. The goal is to ensure consistency and minimize variation.
- Failure Modes and Effects Analysis (FMEA): A systematic method for identifying potential failure modes in a product or process and assessing their impact to prioritize corrective action. For example, identifying potential points of failure in an engine component and implementing design changes to mitigate those risks.
- Measurement Systems Analysis (MSA): Techniques for evaluating the accuracy and precision of measurement systems to ensure reliable data collection. An example would be conducting a gauge repeatability and reproducibility study to verify the consistency of measurement tools used in production.
- Statistical Process Control (SPC): The use of statistical methods such as process capability or sampling to monitor and control a process to ensure it operates at its full potential. For instance, using control charts to track the diameter of a machined part to ensure it stays within specified limits.
- Production Part Approval Process (PPAP): A standardized methodology for demonstrating that a supplier’s production process can consistently produce parts that meet all customer requirements. This includes submitting samples and documentation to the customer for approval before full-scale production begins.
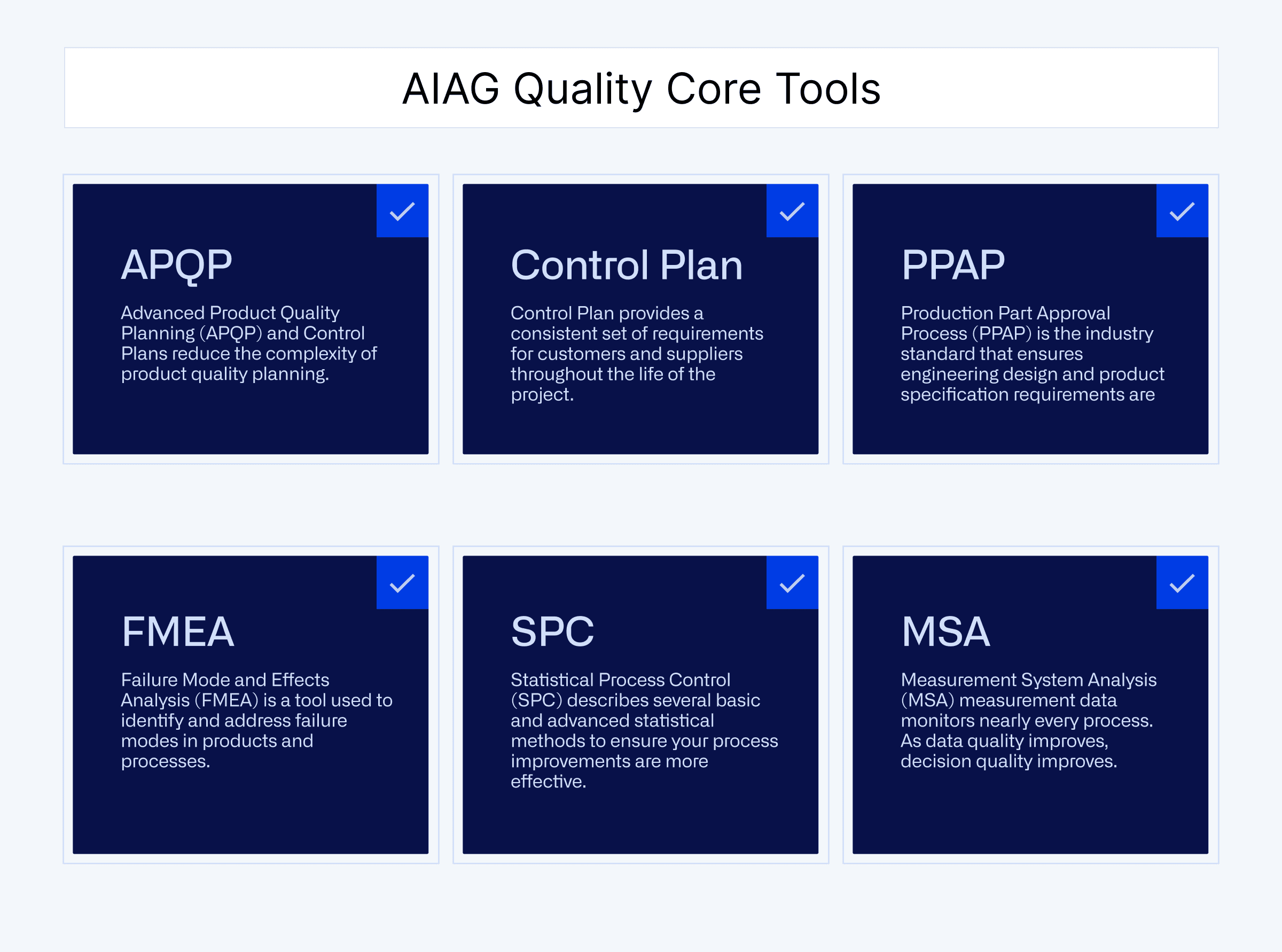
Control Plans and LPAs
The AIAG Control Plan — or any control plan, for that matter — and LPAs together create a comprehensive quality management approach that ensures processes are followed correctly, and that potential issues are identified and addressed promptly.
While it’s ideal for the AIAG Control Plan and LPAs to work together, there is not a prescribed way for them to do so. The Control Plan manual does include best practices for integrating LPAs, making it easier for organizations to improve quality and consistency. The AIAG Control Plan also emphasizes the use of reverse FMEA, which enhances the effectiveness of LPAs by identifying potential failure points and their possible impacts. This integration of the two systems ensures that robust controls help prevent issues before they occur.
To further streamline the integration between control plans and LPAs, specialized software tools and mobile-friendly apps can play a crucial role. These tools can automate on-the-floor data collection, analysis, and reporting, bridging the gap between the control plan and LPAs. By leveraging software, organizations can ensure that all aspects are proactively managed and monitored, facilitating continuous improvement and maintaining high standards of quality.
Where to Learn More About Control Plans
AIAG places a strong emphasis on certifications to ensure quality management and continuous process improvement as the needs of the automotive industry evolve. To that end, it offers training courses and certifications related to its new Control Plan and updated APQP manuals.
At Ease.io, we understand the importance of staying current with industry standards. Both our software platform and global customer success team are here to help automotive manufacturers implement these new guidelines, automate their quality processes, and maintain compliance with the latest AIAG updates.
The latest AIAG updates represent a major milestone in not just automotive, but quality management in general. By integrating LPAs and leveraging new technologies, manufacturers can ensure higher quality standards and drive continuous improvement in their processes.