The Digital Plant Floor Audits Business Case
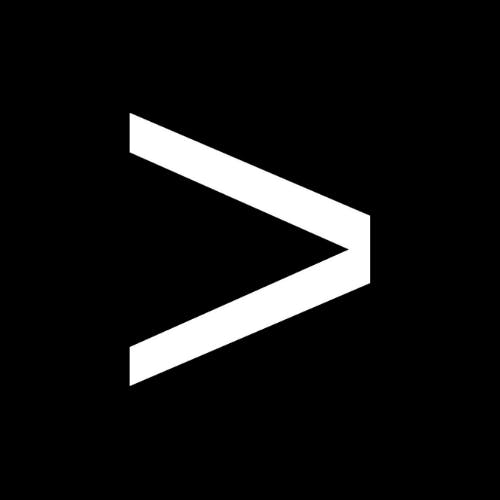
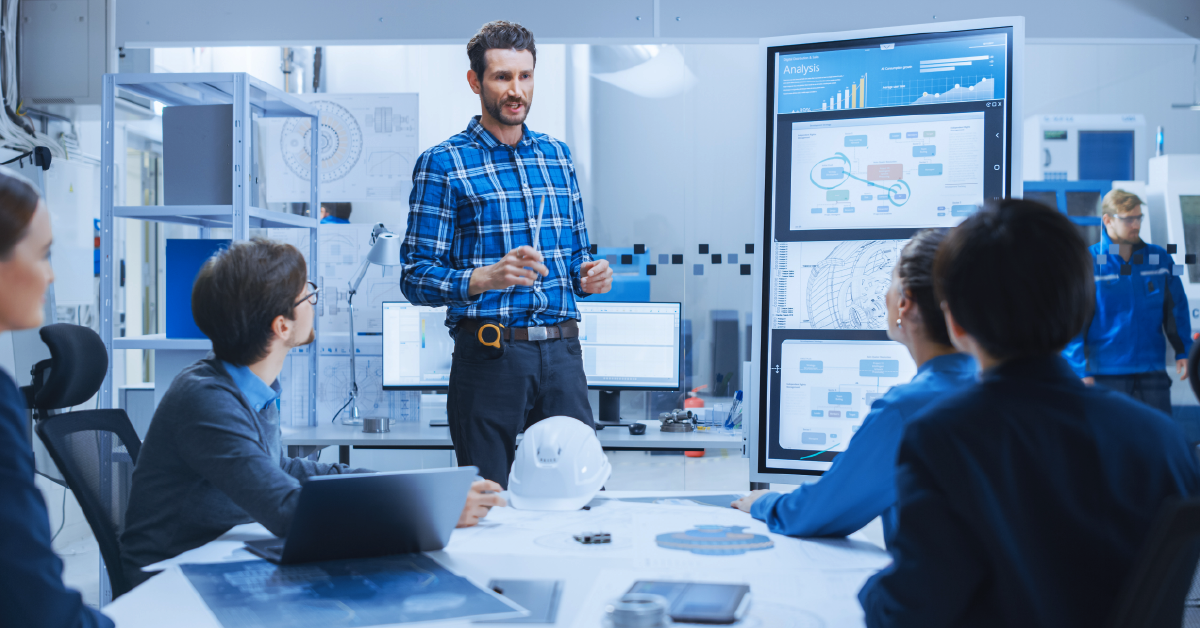
Customer expectations around quality and delivery have never been higher, at a time when plants must cope with labor shortages, supply chain issues and rising inflation.
Implementing new technology like plant floor audit software may seem low on the priority list, until you look at the potential returns.
Below we explore the business case for digital plant floor audits, including how they can save your plant millions in costs annually while creating a culture of excellence.
Download a free whitepaper for in-depth analysis on The Business Case for Layered Process Audit Software
Reducing Quality Costs
Reducing is one of the biggest reasons companies implement plant floor audit software. Scrap and rework costs companies up to , or $22 million for a company with $1 billion in annual revenue.
Many plants have seen marked reductions in scrap and quality costs as a result of deploying plant floor audit software. Automotive supplier Valeo Wipers reduced quality costs 50% as a result of implementing digital plant floor audits. Another automotive manufacturer saw a 73% reduction in internal PPM after implementing EASE, which led to a decrease in scrap rates.
Improving KPIs
Compared with traditional paper-and-spreadsheet audits or even internally built solutions, dedicated plant floor audit software is at quickly making process issues visible that hurt overall equipment efficiency (OEE), cycle time, yield and on-time delivery. This increased visibility is largely the result of:
- Real-time reporting: Management can view audit findings in real time to see where process failures are occurring, respond faster to issues and ensure work is being performed to standard.
- Higher audit completion: Streamlined scheduling, tracking and notifications all help increase audit completion rates, making it simple to perform a larger volume of checks with fewer resources. More audits completed means more data—and more opportunities to catch hidden factory issues that impact plant KPIs.
- Broader coverage of standards: Custom question libraries, rotating checklists and the ability to easily add new questions to audit checklists mean better coverage of standards. This in turn means more issues are caught before they affect customers and plant productivity overall.
- Closed–loop issue tracking: Closed-loop issue management ensures problems that affect productivity don’t fall through the cracks. Being able to consistently find and fix problems faster also helps prevent unplanned downtime.
Accelerating Issue Resolution
Finding and fixing problems quickly is crucial to plant performance. Once a problem is discovered, management needs a way to ensure it gets resolved, and doesn’t just fall off the radar.
Digital plant floor audits provide a more efficient way to track and resolve issues found at any level, allowing teams to:
- Log nonconformances in real-time, as well as any on-the-spot mitigations
- Upload photos of nonconformances to the audit record to streamline root cause analysis
- Create action items for mitigation plans
- Assign action items and due dates to employees
- Easily track all open issues to identify bottlenecks and other problems
The result is faster resolution of issues and thus fewer impacts to safety, quality and productivity. As an example, the automotive manufacturer mentioned above was able to reduce overdue corrective actions by 94% with digital plant floor audits.
Conversely, paper-based audits require manual entry of findings and data analysis, slowing down the process while providing less detail to aid in root cause analysis. With no way to track action items and due dates, corrective action can easily be delayed, allowing problems to get bigger—and costlier—due to the slowdown.
Plant floor audit software also provides a distinct advantage over manual tracking when it comes to identifying systemic plant issues. Imagine, for instance, a plant that receives an OSHA finding over a machine that isn’t properly grounded. With digital plant floor audits, teams can immediately add a question to check grounding on all machines to identify other noncompliant equipment. That means identifying potential issues in hours rather than days (or longer) to redistribute new paper checklists.
Ensuring Adherence to Standards
The hidden factory is a major problem in plants, with even small deviations from standards having the potential to create significant issues. One example is when operators rework parts at their work stations, creating an opportunity for costly quality escapes when they aren’t at work for any reason.
Digital plant floor audits help identify hidden factory issues by increasing visibility into standard adherence and proactively identifying process deviations. Here the major advantage is having a robust, dynamic question library that allows you to:
- Create questions specific to the work cell to ensure preventative and detection elements are working
- Add visual standards to questions to eliminate confusion and ambiguity
- Randomize checklist questions to eliminate pencil-whipping
- Use custom question tags to cover key areas like quality, safety, 5S and more
- Verify corrective actions are held in place
Simplified administration and reporting also enable frequent checks, increasing the likelihood that problems will be caught while freeing up as many as two full-time employees for more value-added work.
Creating a Culture of Excellence
Many plant leaders aspire to create a culture of safety and quality while maximizing productivity but have difficulty actually making it happen on a practical level. Digital plant floor audits provide a framework for a culture of excellence, ensuring operators are following standards and problems are resolved effectively. This, in turn, drives KPI improvement and a sense of shared ownership in quality and plant performance.
Ultimately, plant floor audit software is critical to helping leaders keep their finger on the pulse of the plant. Armed with more data and more eyes on their processes, plants can ensure continuous improvement to drive down costs while increasing customer satisfaction.