5 Lean Manufacturing Principles Explained
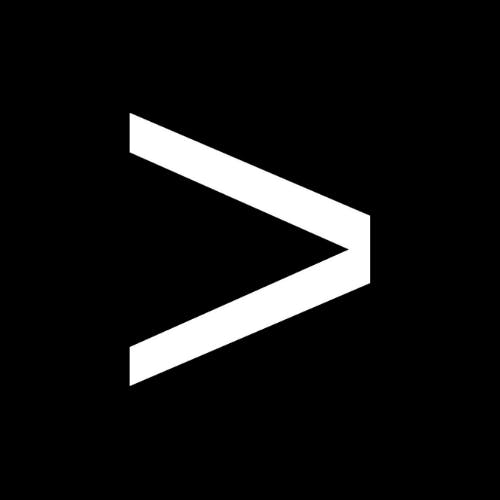
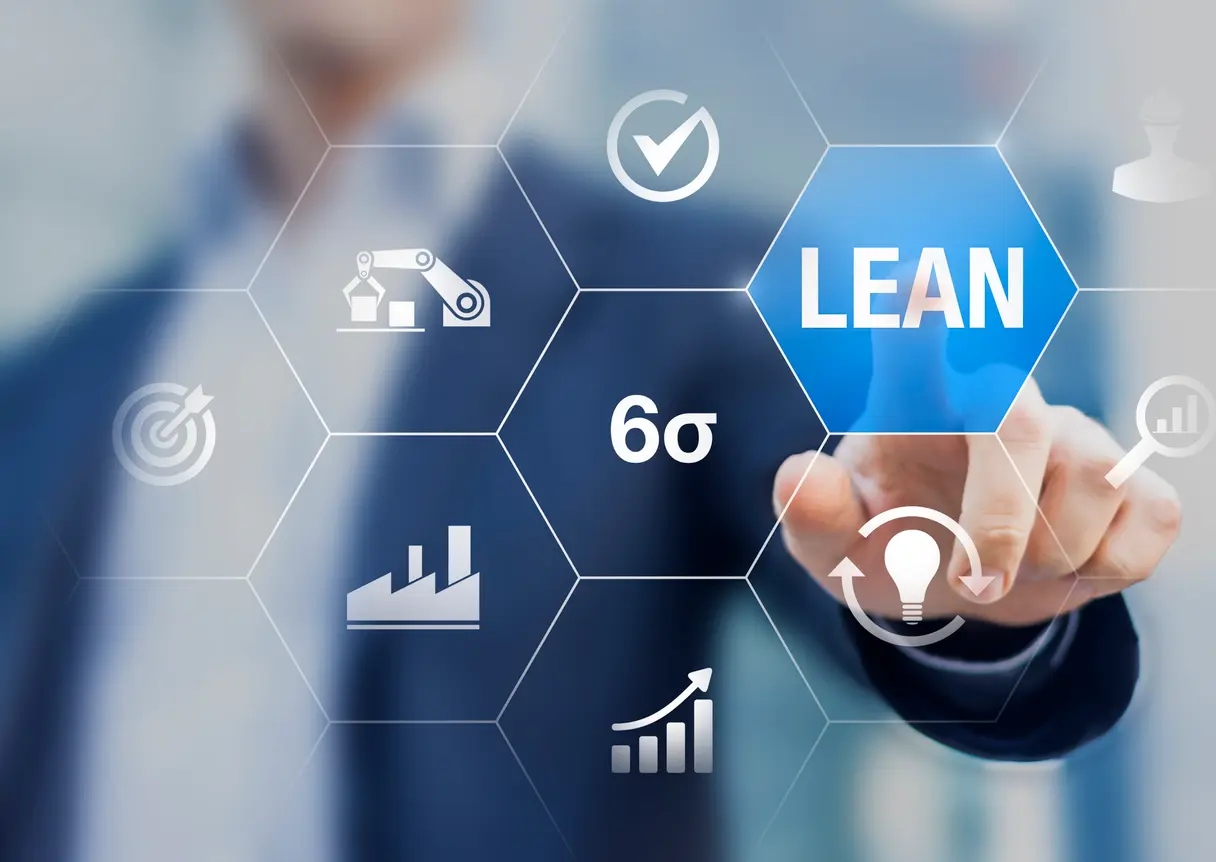
In supply chain management, how do manufacturers maximize their output, keep their costs low, and deliver the highest possible value to their customers all at the same time?
This is the end goal for lean manufacturing. It was developed by Toyota after WWII and later became known as the Toyota Production System, or TPS. Then, as now, lean manufacturing seeks to:
- Reduce waste and rework
- Reduce manufacturing costs
- Speed up production and changeover time
- Improve overall efficiency
- Increase profits
In this article, we’re going to look at what lean experts James Womack and Daniel Jones have identified as the five principles of lean manufacturing and shine a spotlight on the last principle, which is to seek perfection through continuous improvement.
The 5 Core Lean Manufacturing Principles
The American Society of Quality (ASQ) defines lean manufacturing as “the elimination of all non-value-adding activities and waste from the business.” The goal of the lean manufacturing process is to improve efficiency by eliminating waste, cutting costs, and improving process flow.
Let’s dive into the five principles of lean:
#1: Identify Value
In this first key lean principle, manufacturers need to identify what the customer values and what they’re willing to pay for it. Additionally, manufacturers also need to understand what features their customers want and which ones don’t offer any additional worth.
Identifying customers’ priorities allows manufacturers to redesign products so they better represent what their customers are looking for and therefore reduce waste.
#2: Map the Value Stream
With your end goal fully fleshed out from the first principle, you can now draw and analyze the steps to get there. Value stream mapping brings together all the steps it takes to bring a product from raw material to the end customer; this includes determining which activities are worth the effort and which ones are holding you back.
Anything that doesn’t bring your product or service closer to the goals you’ve identified is considered waste. These activities might lead to longer waiting times, excess inventory, redundant inspections, etc.
Once you’ve established where the waste lies, you can begin to map out a value stream without it. The future scenario should improve flow and efficiency, and bring you closer to meeting the customer’s expectations.
Just remember that if it doesn’t ultimately add value for the customer, then it doesn’t belong in your value stream.
#3: Create Flow
Creating flow means ensuring a smooth and uninterrupted production process. Now that waste has been removed from the value stream, you can start introducing flow to strike the perfect balance between production and demand.
To do that, manufacturers can reorganize their workflows to level out employee workloads; break down standardized work steps into smaller actions; train their employees with more adaptive skills; and rearrange employee workspaces to maximize efficiency and reduce unnecessary movements.
One of the biggest manufacturing wastes is caused by having too much or too little inventory, both of which can disrupt the flow of production.
Creating flow is similar to Toyota’s Just in Time (JIT) manufacturing principle, where production is based on an accurate forecast of demand and supply, which significantly lowers waste and inventory costs.
#4: Establish Pull
Rather than pushing products through the production line, the pull system is triggered by real customer demand.
In this system, a customer order is pulled from the shipping department, which then signals the need for new items to be manufactured and additional supplies to be ordered. Implementing lean tools like Kanban ensures that just enough resources are called in at the right time to avoid excessive inventory or high levels of work-in-progress (WIP).
Benefits of establishing pull:
- Less inventory and lower storage costs
- Better quality control
- Less waste
- Improved workflow efficiency
#5: Seek Perfection
Finally, the last of the five lean principles is seeking perfection through continuous improvement. While it’s an easy principle to understand, it’s one of the most difficult to implement.
Seeking perfection through continuous improvement implies that processes and standard operating procedures (SOPs) are subject to change based on feedback from employees and data collected from various sources. The more data manufacturers can analyze, the more streamlined their manufacturing processes will be.
By definition, seeking perfection means that attaining it is never the goal; the real objective is to always look for ways to improve manufacturing so that the most value is eked out of every activity.
Let’s take a deeper look at how to apply lean principle number five.
How to Seek Perfection through Continuous Improvement
If the last of the five key principles is the “ongoing effort to improve products, services or processes,” we can’t just employ these lean concepts and say we’re done. The lean approach to manufacturing is long-term and requires your organization’s ongoing effort to be successful.
A common continuous improvement cycle is the Plan, Do, Check, Act (PDCA) method.
Plan: Change Your Mindset
Mindset change means that the many groups that make up a production facility must change their ways of looking at what they do. These groups include suppliers, design and production engineers, controllers, part fabricators, assembly, shipping, HR, and management. All of these groups must be on the same page about lean manufacturing.
Of these groups, management must take the lead for all change activities. Managers must be familiar with lean manufacturing principles and take advantage of the current thought on the subject, including the 7 Wastes, JIT, and other basic ideas. Then, they can accurately pass along information to instill lean systems proficiently in the above groups. Methods of transferring information include traditional training, education, and incentives.
Do: Implement Lean Thinking and Standard Work Instructions
Employees, machines, and tools are the key elements of any shop. To employ lean thinking, utilize the 5S plan for manufacturing (sort, set in order, shine, standardize, and sustain) and Total Productive Maintenance (TPM).
The results yield:
- Better flow
- Reduced maintenance bottlenecks and machine downtimes
- More organized and proactive repairs
- Increased awareness of safety and waste
Machining and parts assembly should follow the most logical process sequence, basing the rhythm on takt time and production rates. Together, these help ensure synchronization and best flow. Placing employees with multiple skills on the line helps overcome fluctuation in production. For more information on improving the process check out the 5s manufacturing checklist.
Check: Verify the Process
Conducting Layered Process Audits (LPAs) is a good way to determine what is happening after a change in mindset and experimenting with changes on the shop floor. The auditors in the LPA process include personnel on many levels, which provides a complete audit.
What’s more, because you receive input from many people, managers, supervisors, and production workers, LPAs provide varying viewpoints. The audits and the feedback you receive allow you to formulate a thorough view of all of the activities in your facility.
Conducting Gemba walks is an inexpensive and efficient way to see firsthand what processes work and which don’t. Rather than sitting at your desk and using graphs, statistics, and charts to try to improve things, you can proceed to the factory to observe processes and interact with shop personnel.
Act: Make the Principles of Lean Permanent
Now that you’ve laid the groundwork, take permanent action:
- Make the lean principles you studied and passed on to the groups in your facility a permanent way of looking at the entire enterprise and its partners.
- Make the lean improvements on the shop floor permanent. This includes any change in production time, changeover time, transportation, repairs, safety, and waste reduction.
- Make LPAs permanent. This involves using the structured LPA teams you established to conduct continuous audits, ensuring ongoing monitoring of shop activities to drive improvement.
Final Thoughts on Lean Principles
Perhaps the biggest challenge after your facility becomes lean is making sure it stays lean. This requires ongoing monitoring and analysis. But as we’ve seen, this is fundamental to the lean process.
If we employ basic lean knowledge and principles at the start, we can have a facility that not only is lean but also continues to seek out methods to become even leaner.