How to Use LPAs to Drive a Plant Turnaround
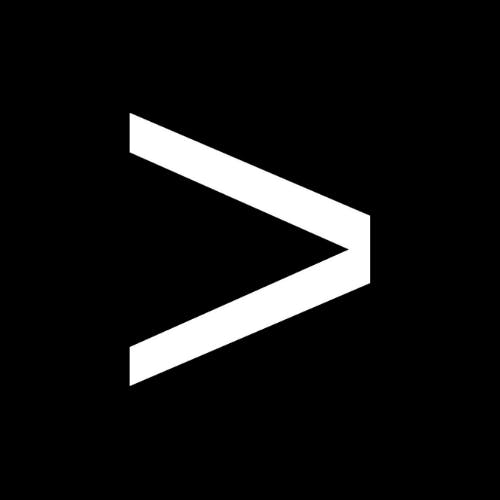
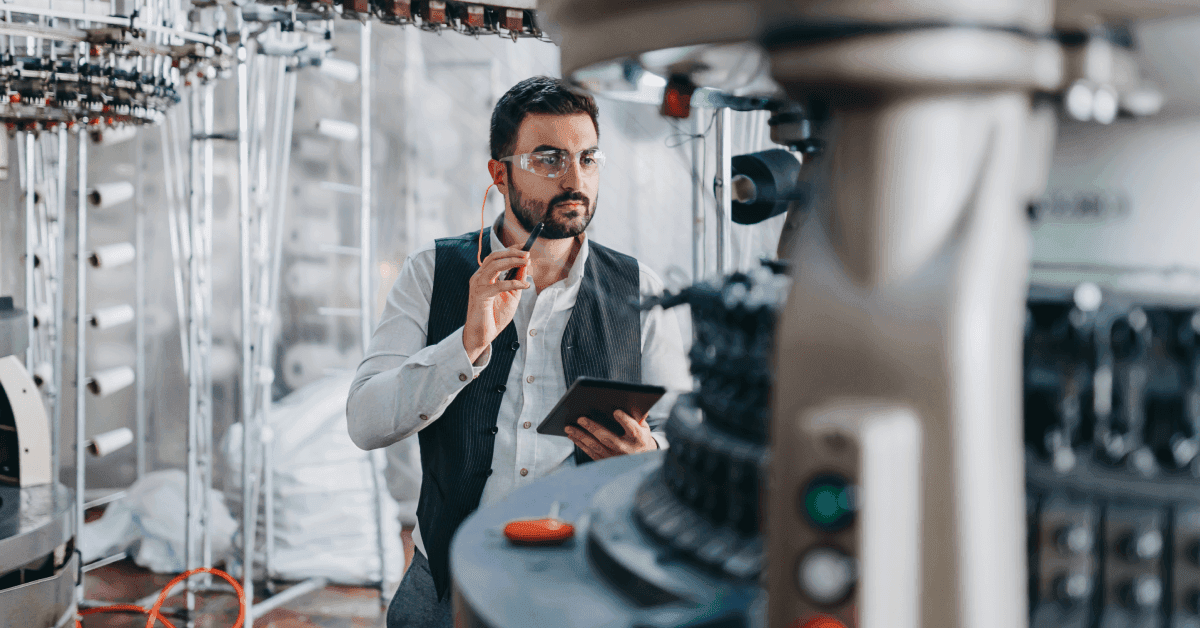
It starts with a late shipment. Production tries to catch up, but standards start slipping. Complaints inch upward. Quality issues that should have been fixed a month ago are showing up again. Only now, they’re more expensive.
All of it starts feeding into something bigger: a plant that’s not hitting its KPIs and no longer operating with control.
This “burning platform” moment is the point where process failures are costing real money, putting contracts at risk and leaving time for little else than firefighting.
One powerful strategy manufacturers have used to reverse course in these situations is layered process audits.
This article discusses how layered process audits can help manufacturers turn around struggling plants, and how one plant used digital audit software to harness their full potential.
Learn about reducing quality costs with our free eBook on Cost of Quality: The Hidden Truth About Your Ultimate Quality Metric
Addressing the Root Cause: Visibility and Process Drift
At the root of most quality problems is process variation, which happens due to a variety of reasons.
A machine’s performance degrades over time, impacting the product’s final quality. An operator follows the same procedure they’ve been doing for months, unaware of a new step added to a process.
Quality leaders know that reducing process variation is the key to process control and, in turn, hitting KPI targets. So why do underperforming plants often find themselves stuck? A variety of factors contribute to the issue:
- Lack of process discipline: Processes don’t follow documented standards, and hidden factory processes undermine quality.
- No daily process visibility: When leadership discovers problems, they’ve already existed for some time, making them harder to correct.
- Inconsistent follow-through: Plants may make gains, but an inability to sustain them over time means people backslide into old habits.
The only way plants can truly gain control over their processes? It’s by implementing a structured verification system that uncovers sources of process variation and closes the loop on problems.
Enter LPAs: The Turnaround Catalyst
Layered process audits (LPAs) involve a system of quick, frequent checks to ensure process inputs conform to plant standards. These checks are multi-layered, performed at varying frequencies by multiple levels of management.
For example, a shift supervisor might conduct an audit once per shift, while a quality engineer performs an audit weekly and the plant manager monthly.
What makes it possible to perform this volume of checks is the fact that checklists are short, designed to be completed in about 10 minutes. Questions may come from recent customer complaints, high-value steps in the SOP, or any process input that impacts quality.
The benefits are more than just theoretical — many plants have found that audit frequency correlates strongly with quality, driving improvements in metrics such as scrap, PPM and customer complaints.
Why do LPAs have such a big effect on manufacturing quality? There are several reasons:
- Prevention focus: LPAs shift the focus from trying to identify defective products during inspection to preventing them at a process level, giving teams time to prevent issues from snowballing.
- Plant floor visibility: The frequency of checks puts more eyes on every process, giving you more chances to catch process errors before they result in defective shipments.
- Sustained follow-through: LPAs prevent recurring problems by providing an additional check on the process after a customer complaint or corrective action.
- Cultural gains: LPAs help create a culture of quality by making quality a daily part of everyone’s job, increasing management’s presence on the plant floor and improving operator engagement.
How One Aerospace Manufacturer Used LPAs to Drive a Plant Turnaround
A leading global aerospace manufacturer had an ambitious goal to drive quality improvement across 21 plants globally. The company had identified internal audits, including LPAs, as a leading indicator of plant performance.
Their goal was to use LPAs as a way to standardize and hold in place best practices that came out of a previous successful plant turnaround. The question was how to scale LPAs across its plants without overwhelming the team with manual scheduling, checklist management and reporting.
One plant in particular was struggling to complete just a handful of audits per year. After implementing EASE LPAs, the plant was able to increase that to roughly 100 audits monthly, resulting in a 53% reduction in customer defects.
“In two plants now, we’ve been able to step in when leading indicators went down, before there was any change to lagging metrics like defects or complaints,” says the company’s director of quality.
EASE has helped them roll out LPAs to 21 plants in six countries, becoming an integral part of the company’s quality process.
“When you need to manage thousands of these audits — and feel confident that you can effectively harness the data — you can’t reasonably expect to do that in a paper system,” says the director of quality. “When you schedule, conduct and report on them electronically, all of those constraints disappear.”
Turning around an underperforming plant starts with getting back to basics: standardizing processes and holding the line on execution.
Digital LPAs offer a cost-effective and high-impact way to do just that, uncovering hidden risks, reinforcing process discipline, and closing the loop on problems to accelerate to your turnaround strategy.