Profiles in Quality: Kaoru Ishikawa
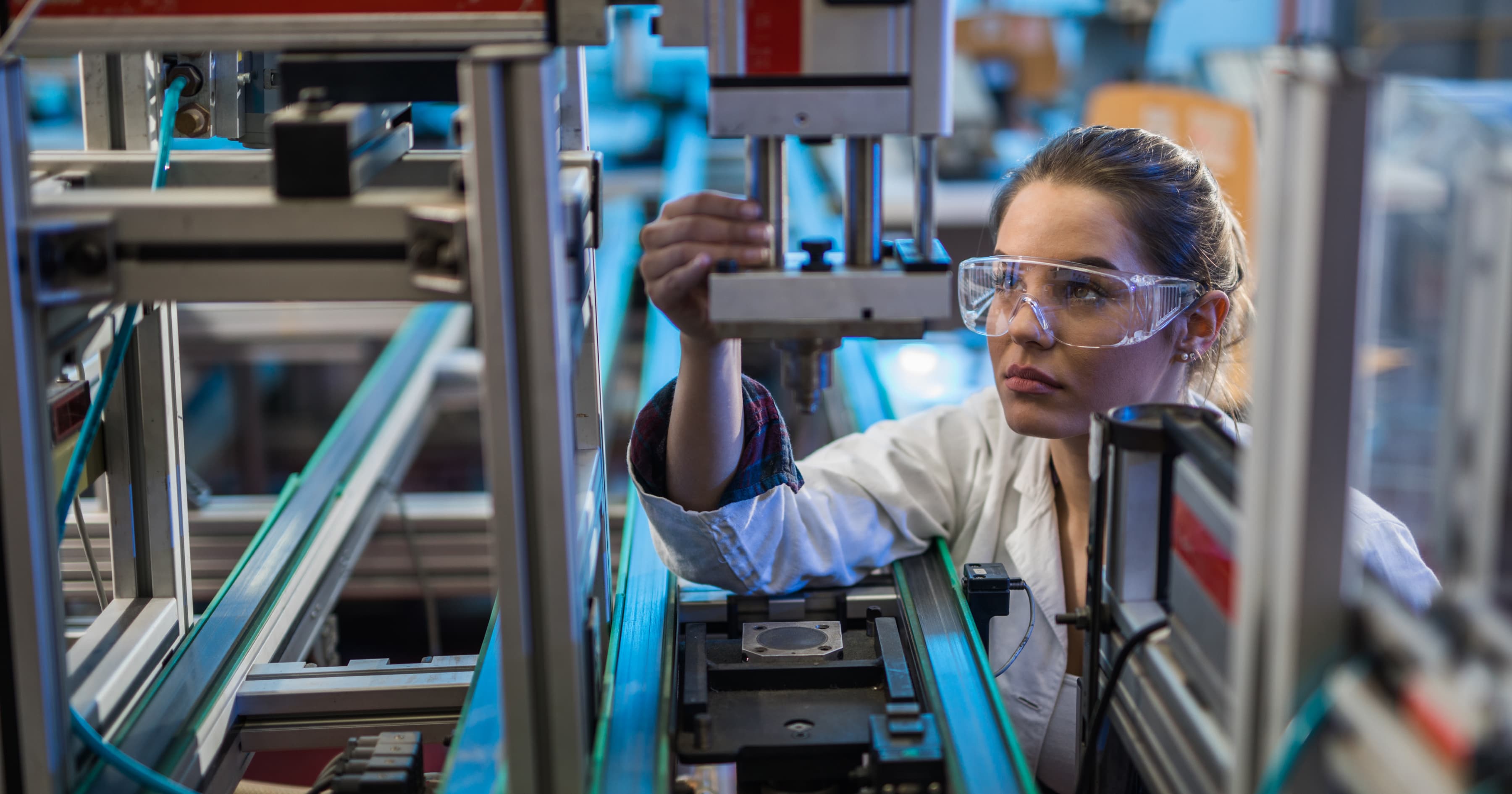
Kaoru Ishikawa, considered the father of Japanese quality, is perhaps most famous for his Ishikawa or fishbone diagram.
The fishbone diagram is innovative in its simplicity, helping teams explore quality problems (the fish head) by breaking it down into contributing factors (the fish bones).
While this practical tool is what he’s most remembered for, Ishikawa championed a number of ideas that reshaped quality and manufacturing as a whole in post-WWII Japan.
Working alongside other founding fathers of quality like W. Edwards Deming and Joseph Juran, his work served as the foundation of quality management as we know it today. Even more indicative of his enduring legacy, his ideas continue to hold true even in the face of widespread technological change.
Download your free Root Cause Analysis 101 Guidebook to learn more about how to use a fishbone diagram
A Foundation in Science and Engineering
Ishikawa was born in Tokyo in 1915, the eldest of eight sons. He graduated with a doctorate in Applied Chemistry from Tokyo Imperial University in 1939, afterward working as a naval technical engineer until 1941.
He then worked at the Nissan Liquid Fuel Company from 1941 until 1947, when he joined the faculty of the University of Tokyo as an engineering professor. It was there he began studying statistical methods, which coalesced with his industry experience to lay the seeds for sweeping changes in Japanese manufacturing quality.
At the time, products manufactured in Japan were widely viewed as cheap and of poor quality. But with the advent of new ideas and Ishikawa’s dedication to systematic quality improvement, all of that was about to change.
Leading the Quality Revolution
Ishikawa joined the Japanese Union of Scientists and Engineers (JUSE) in 1949. In 1951, W. Edwards Deming was invited by JUSE to deliver a series of lectures on statistical process control, and in 1954 the organization also invited Joseph Juran to speak on his theories and methods.
During this time, Ishikawa met Deming and Juran, collaborating with them and building on their early ideas. His expansion of those ideas resulted in a uniquely Japanese approach to Total Quality Management (TQM), one emphasizing a focus on quality not just across the organization but also across the entire product lifecycle.
The work of all three men paved the way for a transformation in quality over the following decades of Japan’s post-war reconstruction and economic growth. There’s no question that the Japanese Economic Miracle was driven in large part by this revolution in quality, ultimately propelling the country into one of the world’s leading economies.
Contributions to Quality
Ishikawa believed, as did Deming and Juran, that everyone in the organization should be involved in quality—not just the quality department. Some of his biggest contributions to the field of quality reflect this core idea, which we discuss in more detail below.
Fishbone Diagram
Also called a fishbone diagram or cause-and-effect diagram, the Ishikawa diagram represents one of Ishikawa’s most enduring contributions. Ishikawa presented the first iteration of his famous diagram in 1945, and today it remains one of the 7 Basic Quality Tools.
Ishikawa developed this tool as a practical way to foster collaboration and systematic problem-solving, where cross-functional teams work together to explore the contributing factors of a problem.
Quality Circles
Ishikawa introduced the concept of quality control (QC) circles in 1962, which built upon an idea first described by Deming in the 1950s. QC circles are groups that meet regularly to analyze and develop solutions to problems in areas such as product and process design, safety and organizational culture. The QC circle movement created by Ishikawa eventually spread from Japan to reach more than 50 countries.
Ishikawa emphasized support from top management and the involvement of all employees, who should be trained on basic quality and problem-solving. He championed the idea that quality issues are addressed most effectively when you empower frontline workers to address problems within their own work processes.
Quality Philosophy
Ishikawa was a strong proponent of treating the next operation or process step as the customer, analyzing those processes and performance data from the customer perspective. Systematic application of basic quality tools, he believed, was the key to continuous improvement.
As he put it, “Ninety percent of all problems can be solved by using the techniques of data stratification, histograms and control charts. Among the causes of nonconformance, only one-fifth or less are attributable to the workers.”
Throughout the course of his trailblazing career, Ishikawa wrote hundreds of articles and dozens of books on quality control. He also received numerous awards, such as the Deming Prize and Shewhart Medal. His work included traveling worldwide to teach the holistic approach of Japanese TQM, as well as establishing International Academy of Quality (IAQ) and what would later become the International Conference on Quality (ICQ).
While groundbreaking at the time, Ishikawa’s human-centered approach to quality is now firmly cemented in the fabric of modern quality philosophy. Even today, amid unprecedented technological change, his ideas provide a guiding star for those companies truly dedicated to continuous improvement.