Sustainable Manufacturing: Benefits, Challenges, and Strategies
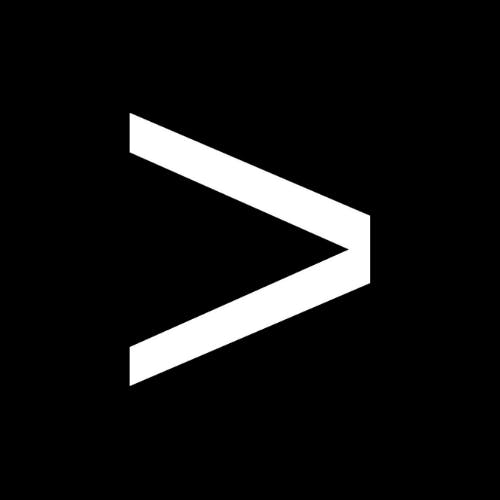
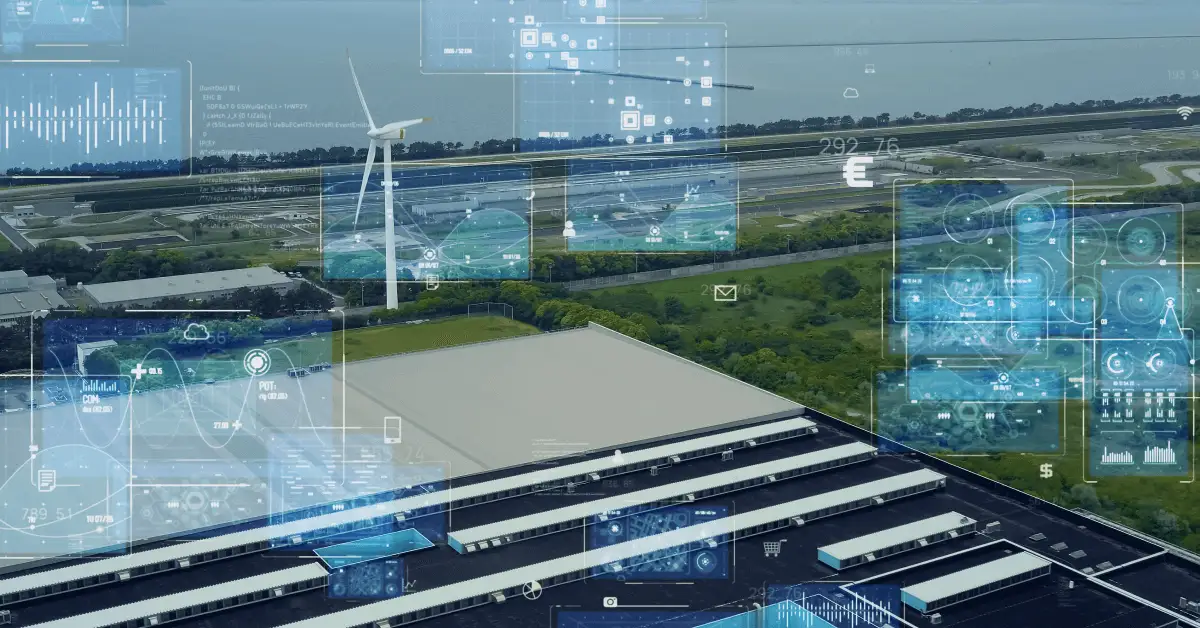
A survey by PricewaterhouseCoopers revealed that more than 80% of consumers today are willing to pay more for sustainable products, despite cost of living pressures.
Adopting sustainable manufacturing practices does more than just provide a competitive advantage, however. It also adds to the bottom line in other ways, from reducing operating costs to improving process efficiency and compliance — all while creating a company more resilient to disruption.
Below, we explore the basics of sustainable manufacturing, including benefits, challenges, and a cost-effective strategy any plant can use to improve sustainability without expensive technology.
Learn more about improving efficiency with our free eBook on The 5S of Lean Manufacturing Principles
What Is Sustainable Manufacturing?
Sustainable manufacturing is the process of creating products in a way that minimizes environmental impacts, conserves natural resources, and prioritizes employee and community safety.
Core components of sustainable manufacturing include:
- Energy efficiency and reduced resource consumption
- Minimizing waste and emissions
- Sustainable supply chain, material sourcing, and product design
- Proactive environmental, health, and safety (EHS) compliance
Benefits of Sustainable Manufacturing
Beyond environmental stewardship, implementing sustainable practices boosts a company’s bottom line in several ways:
- Lower resource and manufacturing costs
- Fewer regulatory violations
- Enhanced brand reputation and higher sales
- Easier access to capital
- Improved hiring and employee retention
Sustainable Manufacturing Practices and Technologies
Recent years have seen a proliferation of eco-friendly practices, technologies, and global standards focused on reducing manufacturing’s negative environmental impacts.
EHS Management Systems
ISO 14001 for Environmental Management Systems is a common starting point for companies looking to improve their environmental performance, covering elements like:
- EHS regulatory compliance
- Environmental impact and risk assessment
- Sustainable resource use and circular economy principles
Energy Efficiency
Companies looking to improve energy efficiency often turn to ISO 50001 for Energy Management, which provides a systematized framework for:
- Identifying and reducing energy waste
- Implementing systematic efficiency improvements
- Optimizing production scheduling to minimize energy spikes
Waste Reduction
Reducing waste of all kinds is critical to sustainability and achieving cost savings. A few of the bigger ways organizations are tackling waste in their operations include:
- Lean manufacturing: Implementing lean manufacturing practices can help identify inefficiencies in the production process, while also reducing product defects.
- Circular economy principles: Incorporating circular economy principles in areas such as supply chain, operations, logistics, and product design can have a significant impact on achieving waste reduction targets.
- Digital transformation: Deploying smart factory technologies that leverage tools like automation and predictive analytics can help further reduce inefficiency and waste.
Sustainable Product Design
Product design is a core element of sustainability. Life cycle assessments provide a comprehensive evaluation of a product’s environmental impact from cradle to grave, so companies can:
- Identify stages in the product life cycle with the greatest environmental impact
- Select more sustainable materials
- Optimize manufacturing processes to minimize waste and resource use
- Improve product durability and repairability
- Develop recycling and disposal strategies to recover materials and minimize negative environmental impacts
Supply Chain Sustainability
ISO 20400 for Sustainable Procurement can help manufacturers integrate sustainability into purchasing decisions to minimize environmental impact and promote social responsibility while ensuring economic viability.
Emerging technologies like digital supply networks (DSNs) are also helping companies improve supply chain sustainability by leveraging tools like AI, blockchain and IoT to optimize resource use and reduce emissions.
Emissions Reductions
Manufacturing industry is a heavy contributor to greenhouse gas emissions, but green manufacturing practices can help mitigate this impact. Some of the ways manufacturers are working to address the issue include:
- Transitioning to low-emission process methods
- Powering plants with renewable energy like solar and wind power
- Offsetting carbon emissions through reforestation or carbon capture initiatives
Challenges in Sustainable Manufacturing
Companies looking to capitalize on the potential benefits of sustainable manufacturing face a number of challenges today.
For starters, many manufacturers still lack a set of standardized metrics against which to measure and compare their sustainability performance. Sustainability reporting is becoming more prevalent, however, with organizations like the Global Reporting Initiative (GRI) providing a standardized framework for setting and tracking sustainability goals.
Supply chain complexity is another big hurdle. That’s because many raw materials originate from regions with minimal environmental and labor protections, making ethical sourcing a challenge. In addition, moving raw materials and components through complex supply chains also increases a product’s carbon footprint, making logistics a critical part of sustainability.
Finally, there is the cost associated with implementing sustainable technologies. Over one-third of executives surveyed in Fictiv’s Sustainability in Manufacturing Report, for example, say funding issues are standing in the way of meeting sustainability goals.
Tackling the Ultimate Waste
Sustainability in manufacturing isn’t just about energy use or material sourcing — it’s also about reducing waste at its source. Defects and process inefficiency are some of the most overlooked (and costly) forms of waste, yet they’re also areas where companies can make big improvements without hefty capital investments.
For example, if it takes one kilowatt-hour (kwh) to produce a part, making a bad part wastes not just materials but also:
- The 1 kwh it took the machine to produce the part
- The labor hours required to make and inspect the part
- The fuel and packaging used to ship defective parts and process returns
- The time and resources it takes to identify, contain, and correct the problem
So, even if you improved the machine’s energy efficiency by 25%, that will be quickly erased if you aren’t systematically preventing defects. Increasing your percentage of good parts, by comparison, delivers a bigger impact on reducing waste, emissions, and resource consumption than efficiency gains alone.
Using Manufacturing Process Audits to Support Sustainability
To be truly sustainable, manufacturers must eliminate waste at its source. This requires two key actions:
- Identifying sources of process variation
- Improving overall process efficiency
Process audits help companies achieve these objectives, allowing them to:
- Verify that operators are following SOPs on a daily basis
- Ensure all process inputs such as machine settings, materials, and preventive maintenance activities follow documented standards
- Uncover hidden inefficiencies through the process of observation and engaging with operators
Plant floor audit and inspection software like EASE simplifies this process so manufacturers can easily conduct frequent process audits without having to manage paper checklists or spreadsheets. Live data on process failures can alert managers to areas needing special attention, helping prevent defects while fostering continuous improvement and process optimization.
The key takeaway here is that true sustainability isn’t possible unless it’s rooted in a foundation of process efficiency. What’s more, no amount of technology can compensate for processes that are only loosely held in place. Achieving sustainability goals requires a holistic approach, one that leverages both emerging tools and time-tested strategies for ensuring process excellence.