How Quality Managers Can Have a Successful First 90 Days
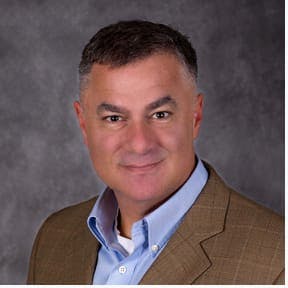
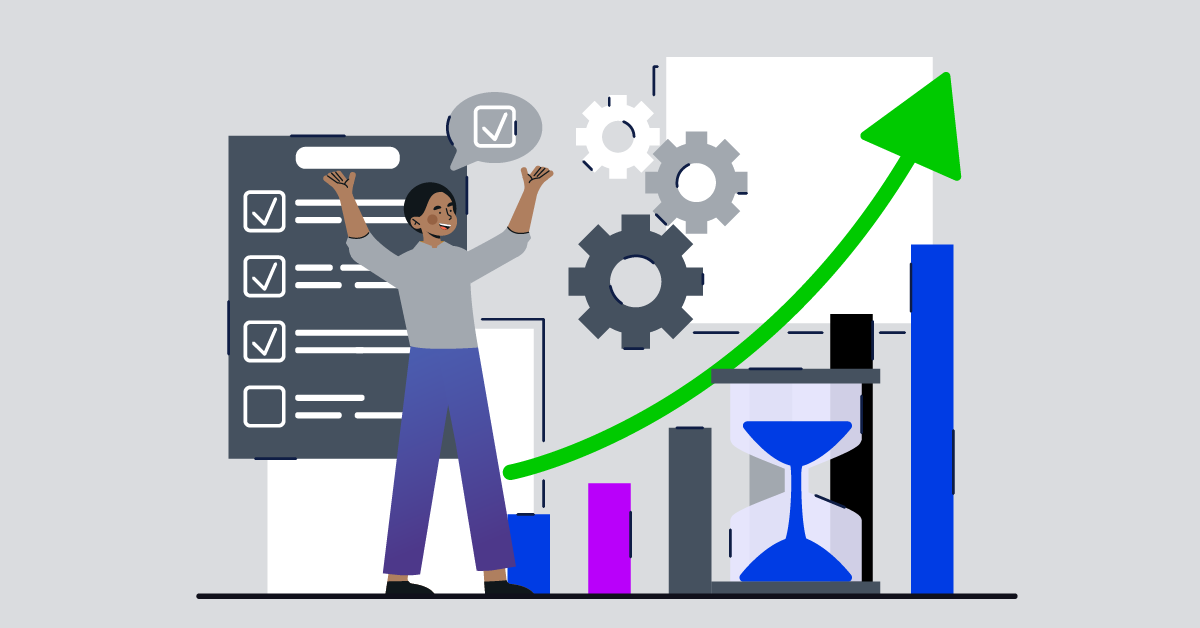
If you’re starting a new position as a quality manager, you’re probably thinking about what to prioritize in your first days and weeks on the job.
There’s no question that people will want your help putting out fires, but doing so could distract you from what’s most important.
Some quality managers also think they need to make a big splash when they start, but this is also a flawed approach.
To help set your priorities, we at The Luminous Group have compiled a list of the top actions to focus on in your first 90 days. We’ll talk about who you need to connect with, crucial information to get and the goals that will help you drive meaningful change.
Read our success story on how a Fortune 500 automotive supplier reduced PPM 73% with EASE
Learn Your Plant’s Processes
One of your top priorities when starting a new role as a quality manager is to understand the key processes at your plant.
In fact, we recommend quality managers go out and work some of the equipment, whether it’s for four hours or even a whole shift. That’s valuable time spent and valuable relationships created with operators.
Instead of just walking by a stamping press, for example, helping do a mold change on the machine will give you a better understanding of the process. You’ll walk away with key information on what’s going on at the plant, and who you can talk to when you need fast information.
What’s more, you’ll show that you’re willing to roll up your sleeves and work—and that you’re not just a “suit” who sits in the office.
Visit Your Key Customers
As quality manager, it’s difficult to be in the middle. It’s important to remember that you’re not just a bridge between the plant manager and the quality team. You also need to be the bridge between plant operations and customers.
With that in mind, it’s critical to go visit your top three to five key customers, looking to answer questions such as:
- What’s their view on your plant’s quality performance?
- What do they need from you?
- If you could do one thing for the customer, what would it be?
The main goal here is to establish a relationship with your top customers and identify changes that could improve your standing.
Spend Time with Your Peers
Making connections with other leaders in the plant is another top priority when getting started in terms of identifying gaps to address.
For example, what does engineering need from the quality department? What about logistics, human resources and finance?
More than just sitting in a meeting together, you have to spend time one-on-one with managers of other departments. If you take the time to establish these relationships, you’ll gain valuable insights into areas where the quality department isn’t meeting expectations. This information can then help determine your strategic goals moving forward.
Connect with the Quality Team
In addition to building relationships with other managers, it’s crucial to connect with members of your own quality team. Spend time going through the last annual review for each employee, from quality engineers to technicians, auditors, inspectors and more. Then meet with them one-one-one to find out things like:
- Are they happy in their role?
- Do they feel supported?
- Are they in a position where they feel successful?
- Do they have the tools they need?
- What else do they need from you?
For example, if your department is responsible for layered process audits (LPAs), do you have someone in the department who really understands them? Or does the team need more training? Does the team have the tools they need to execute failure mode and effects analysis (FMEA), control plans, LPAs and gage R&R?
Look also to identify the strengths of individual quality engineers, whether it’s relating to customers, problem-solving or gage design. This will help you delegate tasks while leveraging everyone’s strengths as efficiently as possible.
Assess Your Systems
The final goal we recommend for quality managers in their first 90 days is evaluating systems. Specifically, you should assess whether you have strong systems in place for processes such as:
- First piece inspection
- LPAs
- Advanced product quality planning (APQP)
- Launching new products
- Approving and releasing gages to the plant floor
Ultimately, you’re looking to find out whether these systems are strong and being followed, or whether they’re nonexistent and need to be created.
When you walk in the door on your first day, you can practically guarantee people will want to draw you into fixing day-to-day problems. Quality managers that get pulled into firefighting, however, aren’t effective in their job—that’s the role to delegate to a strong quality engineer.
Anything you do to make a splash is also likely to be seen as a flavor-of-the-month initiative. To create real quality improvement at the plant level, you need to seek first to understand rather than trying to make people understand you.
Achieving these goals starts with figuring out where your gaps are, then laying out plans to address systemic, long-term problems. In the end, this measured approach is more proactive and more strategic, increasing your odds of success.