Questions to Ask When Benchmarking Your Layered Process Audit Program
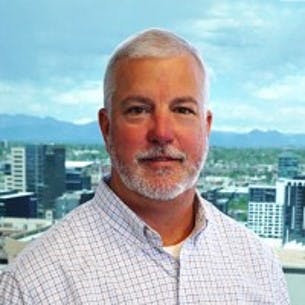
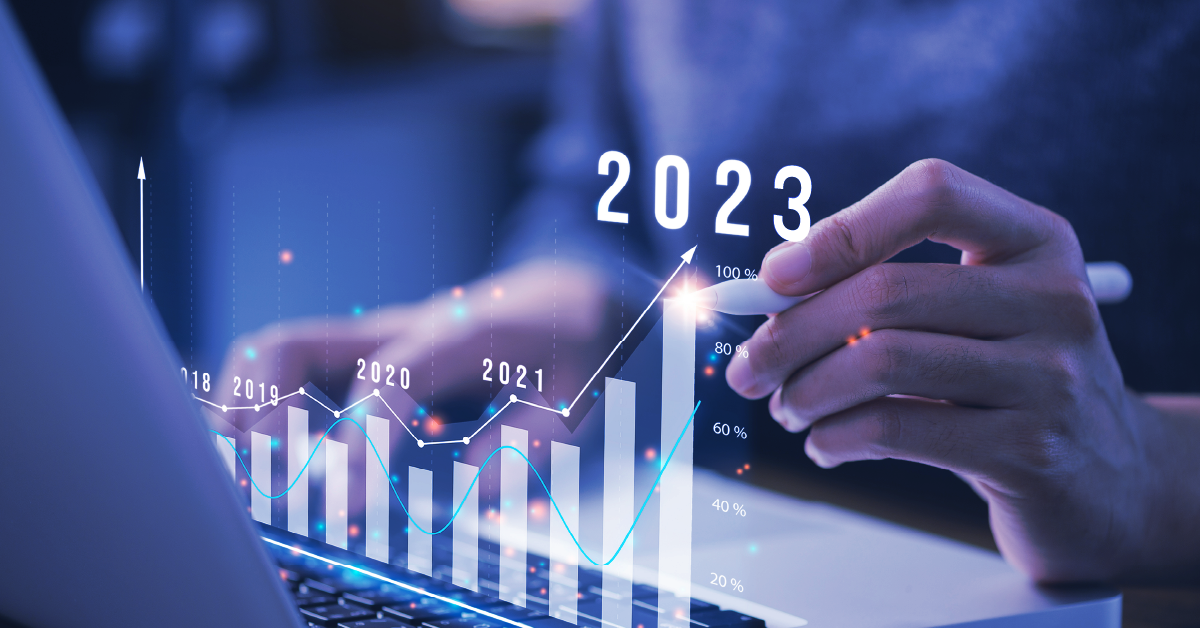
As a best practice, you should review your layered process audit program every three to six months to evaluate the overall health of your program. While these fast, frequent audits can have a significant impact on KPIs like scrap and defects, that can only happen with a healthy LPA system.
To help manufacturers know what to look for during these periodic reviews, we’re examining five questions to ask when benchmarking your LPA program. Plants will likely want to select a few of these to monitor at a high level, tracking any major swings to assess what might be behind them.
Request a personalized EASE demo today to learn how our solution can help you benchmark your plant floor audit programs
What’s Your Audit Completion Rate?
One metric that every plant should be tracking is its audit completion rate. It’s the clearest indicator of LPA system health, and for automotive manufacturers, it may relate directly to customer requirements.
Plants should aim for at least a 90% audit completion rate. When the audit completion rate is between 80-90%, the LPA team should investigate whether a certain layer or work area isn’t performing their audits. When the audit completion rate falls below 80%, that’s when management needs to step in.
Note that a 100% audit completion rate isn’t necessarily a good thing. In fact, it’s more likely to indicate pencil-whipping where people are just passing questions without actual verification.
How Many Open Findings Do You Have?
The number of open findings will vary according to the size of the plant, but you want to make sure that over time this metric doesn’t move by more than 10% in either direction.
If the number of open findings jumps, that means people aren’t closing findings and you may have lingering problems. If it goes down sharply, that could mean people aren’t reporting findings. In some cases, you might find a corrective action resolved a group of findings. However, you need to look deeper to see if a specific work area started reporting zero findings or whether another issue may be at play.
What’s Your Question Failure Rate?
This metric looks at how often a question fails. The Luminous Group recommends a positive or yes answer rate of 90%, with a fail rate of about 10%. If a question is confusing or otherwise ineffective, this should be caught when its failure rate is 10-20%. If a question fails more than 20% of the time, management needs to get involved as it may indicate a recurring or systemic quality issue.
One way to dig deeper here is to look at the failure rate by layer. If layer 2 audits have a higher failure rate for a particular question compared with layer 1 audits, that’s a problem. What it shows is that supervisors or team leads aren’t reporting issues and that they’re only being found by higher layers such as quality engineers. In general, the question failure rate should be lower at higher layers.
Note that if auditors are finding and correcting problems on the spot, it’s not helpful if they don’t document the problem in the LPA system. For instance, it might be that a work area needs hoses run overhead instead of on the floor or needs retractable extension cords to prevent trip hazards. Reporting issues is key to helping management understand what operators need to do their jobs.
How Many Audits Include at Least One Finding?
Another question to ask when benchmarking your LPA program is what the percentage is of audits with at least one finding. Experts at EASE believe every audit should have at least one finding.
Where Are Your KPIs Trending?
LPAs can help reduce scrap, defects, and complaints, and while there are no hard and fast rules, these KPIs should make sense within the context of your LPA metrics.
For example, as you improve your LPA system over time, your scrap rate should trend downwards, as should complaints and cost of poor quality. It’s worth noting, however, that the number of findings should still be level as you update your question library to reflect emerging risks. Overall, the system will positively impact KPIs even though the number of findings remains consistent.
How Long Do Audits Take?
One final metric worth measuring is the average time to complete audits, making sure that they take about ten to 15 minutes to complete. If audits are taking too long, that could mean you need to reevaluate your questions. If they are being done too quickly, it might indicate pencil-whipping.
Benchmarking your LPA system health is important to ensure you’re getting value for the time you put into the audits. Plants should choose a few key metrics to track at a high level, monitoring for changes similar to how they use control charts to maintain process control.
LPA software like EASE can simplify the reporting process and track metrics on interactive dashboards. This makes it easier to spot trends, record corrections and assign mitigation action items, so plants can spend more time fixing problems than managing the LPA system itself.