Complete Guide To The Connected Worker Platform in Manufacturing: Uses, Benefits and Solutions
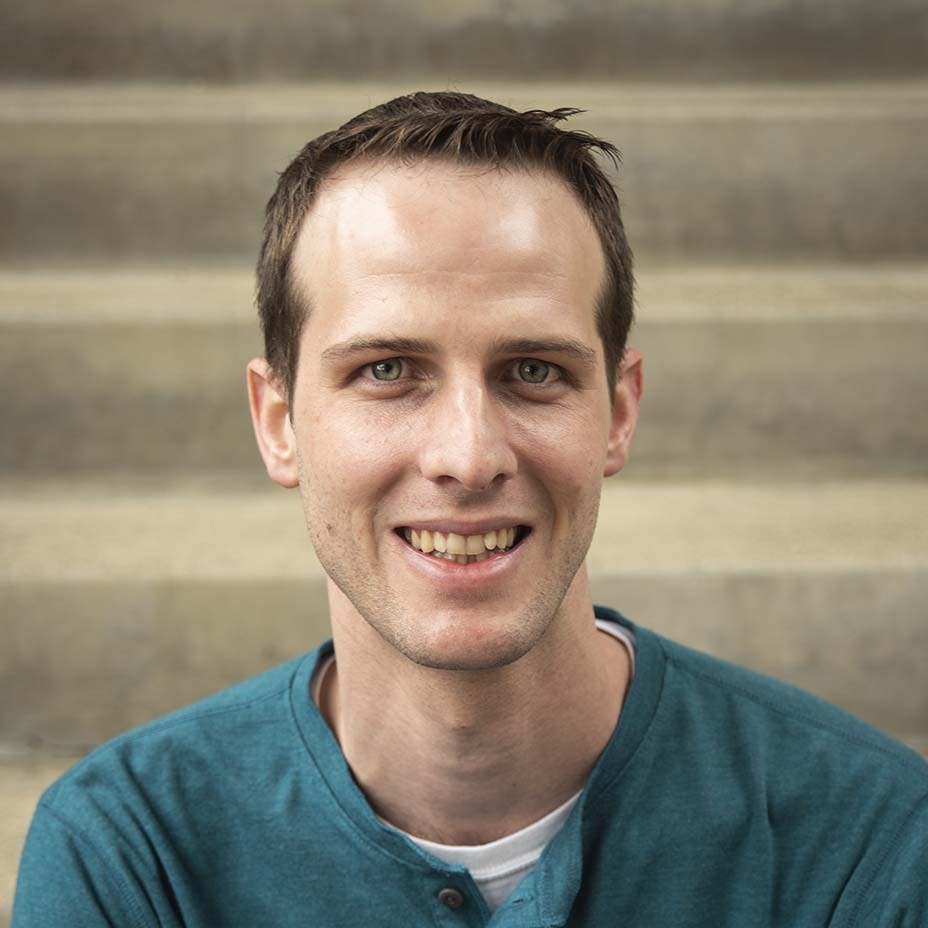
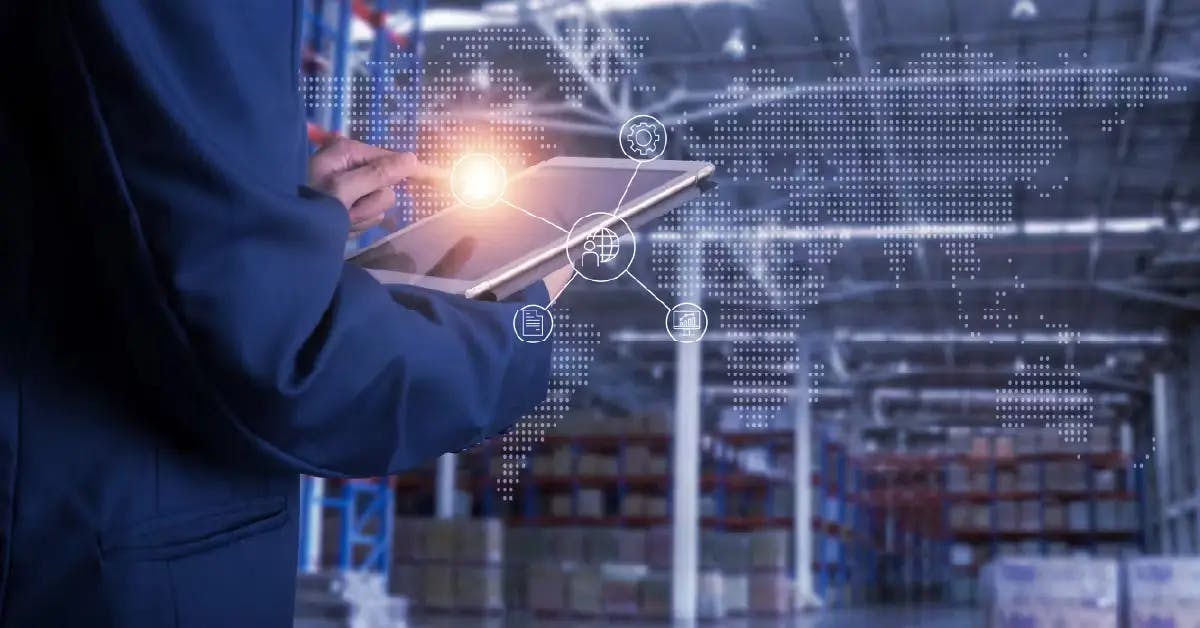
A supervisor gets a reminder on their smartphone with a digital link to their daily process audit checklist. An alert flashes on a workstation screen alerting an operator of a broken machine sensor. A worker needs additional screws at their station, prompting an instant message to the team lead for help.
The above are all examples of how the spread of connected worker technology is changing the face of manufacturing today. In fact, more than half of manufacturers have implemented connected frontline worker solutions, with another 20% planning to do so in the coming year, according to LNS Research.
Here we provide an overview of connected worker solution, covering topics such as:
- What is a connected worker?
- Uses and benefits in manufacturing
- Technologies for connecting workers
- Implementation considerations
Learn more about Manufacturing Quality Trends to Watch in 2023
What Is a Connected Worker?
A connected worker is empowered with digital tools to access information, communicate in real time, and automate plant floor processes. Common tools used in manufacturing include mobile devices, cloud applications, and Industrial Internet of Things (IIoT) sensors applied to areas such as:
- Safety
- Quality management
- Maintenance and asset management
- Operations
- Employee training and workforce development
- Continuous improvement programs
Benefits of Connected Workers in Manufacturing
According to LNS Research, 80% of industrial transformation leaders have achieved quantifiable value from connected worker platforms. What are some of the benefits manufacturers are seeing in their plants?
Easy Access to Mission-Critical Information
Connected worker platforms put information like training materials, work instructions, and troubleshooting guides at the operator’s fingertips. This can result in:
- Accelerated onboarding and time to productivity: Making training resources available at the workstation reduces shadow days and onboarding costs, helping operators become productive faster.
- Reduced equipment downtime: On-demand troubleshooting resources and the ability to get answers on the plant floor helps resolve issues faster and minimize costly downtime.
- Reduced defects and costs: Plant floor knowledge management tools can help remind operators of critical-to-quality job steps and known mistakes to avoid.
Real-Time Communication and Collaboration
Real-time communication—both to and from frontline workers—is the hallmark of connected workers. Examples include:
- Sending a quality alert to employee smartphones at the beginning of a shift
- Allowing operators to video chat with engineering when troubleshooting process or machine issues
- The ability for employees to request additional components or flag maintenance issues, reducing quality issues downstream
- Using layered process audits to link quality, operations, and engineering, which are traditionally siloed in manufacturing
The ability to collaborate more effectively has the potential to unlock significant value for manufacturers, specifically in multi-step processes such as maintenance and root cause analysis. According to McKinsey, digital transformation of these two processes alone can add $180 million to the bottom line for a company with $10 billion in revenue.
Fewer Production Defects
Connected worker solutions improve visibility into manufacturing processes to reduce production errors, defects, and costs. This is achieved through:
- Standardizing processes using tools like frontline knowledge management and mobile plant floor checks to identify process non-conformances
- Ensuring operators have the materials and support they need to do their jobs right
- Providing feedback on whether operators execute processes correctly, for instance with process audits or error-proofing tools like pick-to-light systems that ensure operators choose the right parts in the right sequence
Process Data Insights
Manufacturers have vast troves of process data available to them, but in many cases don’t use this data to drive decision-making. Connected worker platforms help harness process data, turning it into insights and leading indicators to guide action.
For example, one automotive plant was experiencing a large number of failures due to broken sensors on an axle carrier. Each time an axle failed, operators would load it onto a cart for offline testing, creating additional steps while the carrier continued erroneously failing conforming axles.
Looking at the data, they found that one carrier was responsible for 95% of test failures. Connected worker technology can help close the loop by:
- Automatically identifying the problem by tracking individual carrier data
- Instructing the operator to tag the carrier and move it offline if it failed three of the previous five axles
- Notifying maintenance which carrier needs work done on its test mechanism, even identifying the sensor needing replacement
This not only simplifies asset management but also makes the manufacturing process more efficient by reducing unnecessary labor. Reporting the right data to operators is the critical link, without which the problem would continue undetected.
Workforce Engagement
Connected worker solutions promote employee engagement in many ways, helping to both support an older workforce and attract the next generation of manufacturing workers. Enhanced communication and skills reinforcement also create a culture of engagement, contributing to improved retention and lower turnover.
How does this work?
- Supporting older workers: Older employees may be very familiar with one job and not necessarily used to job rotation. Rather than expecting them to memorize ten new steps immediately, a connected worker platform can provide procedure checklists with differing levels of detail based on the worker’s certification level.
- Attracting younger workers: People entering the workforce today are digital natives accustomed to using technology in every area of their lives. Attracting these workers means giving them the technology to work efficiently, do their jobs well and make a positive contribution to quality.
- Improving retention and reducing turnover: Connected worker platforms make it easier to communicate issues and ensure they’re resolved, making workers feel valued and less likely to quit. They also give operators confidence that they’re doing their jobs right, a key part of engaging and retaining workers.
Improved Safety
Companies that implement connected worker solutions in their plant can use them to improve safety outcomes in a variety of ways, including:
- Reinforcing safety standards: Using plant floor checks to reinforce standards and verify controls and personal protective equipment (PPE) usage keep them top of mind for frontline workers.
- Responsive reporting: The ability to document hazards, near-misses and incidents on the spot improves data capture, while effective issue management accelerates resolution to reduce risk.
- Ensuring training compliance: The ability to track training completion and certifications digitally helps management identify training gaps and ensure workers have the required training for their station.
Download Our Free Digital Safety Inspection Whitepaper
Technologies Behind Connected Worker Solutions
Several technology options exist for manufacturers considering a connected worker solution in their plant. Below we discuss some of the main types of connected worker solutions, including:
- Platforms and interfaces
- Cloud and edge computing
- Smart sensors and IT devices
- Wearables and mobile devices
Platforms and Interfaces
LNS Research defines four main categories of connected worker platforms:
- Operations collaboration and execution: Making up the lion’s share of connected workforce platforms deployed in manufacturing, this category focuses on digitized work instructions, data integration across multiple systems, and collaboration across different operations.
- Augmented reality: The next most common platform in use today adds contextual content and real-time frontline support to digital work instructions.
- Specialty platforms: On top of the above capabilities, specialty platforms offer tailored options that may include pre-configured support for specific use cases, remote support, and advanced analytics.
- Niche platforms: These platforms are targeted to specific use cases and domains, such as remote support and dynamic training solutions.
Cloud and Edge Computing
Cloud software and edge computing are two tools that have played a pivotal role in the emergence of connected worker technology. Edge computing focuses on processing data at the edge of computing networks where it’s used. In manufacturing, edge brings computing to the Gemba, or where the work is done.
In a similar vein, cloud computing is changing manufacturing by allowing data to be collected from and transmitted directly to the plant floor. Mobile audit and inspection apps, for example, allow teams to conduct audits, capture findings and launch resolutions via mobile devices.
Smart Sensors and IT Devices
Smart sensors provide built-in data processing and communication to deliver real-time plant floor insights for improving quality, safety, and efficiency. Applications in manufacturing include uses such as:
- Defect detection
- Equipment condition monitoring
- Environmental monitoring
- Asset and inventory tracking
The axle carrier example above is an example of smart sensors combined with edge and cloud computing. Here sensors analyze data at the point of manufacture, communicating actionable insights directly to operators rather than trying to assess the problem in retrospect.
Wearable Devices
Wearable devices and sensors have a variety of uses in manufacturing, providing feedback, guidance, and alerts to help workers perform safe, high-quality work. Barcode scanners are one such example, helping ensure frontline workers are using the right materials while allowing for real-time inventory management.
The most pervasive use of wearable devices is in safety applications. Smart helmets are an example, providing live monitoring for workers in hazardous environments for parameters such as:
- Location
- Vital signs
- Chemical exposure
- Radiation exposure
Embracing Industry 4.0 with a Connected Worker Platform for Digital Transformation
Connected worker solution is a rapidly growing driver of digital transformation. Those actively engaged in deploying these solutions are in position to build more responsive, agile operations. Those that aren’t, however, will only fall behind.
At the same time, companies shouldn’t implement new technology just for the sake of it. Instead, you need defined objectives and metrics for determining success. Lack of defined standards is also a barrier to forward progress, as no amount of technology can fix plant problems without a solid foundation in the basics.
With established standards in place, however, and a clear view of your goals, connected workforce technology can provide a path to continuous improvement and operational excellence.