3P Lean Manufacturing: What, When, and Why
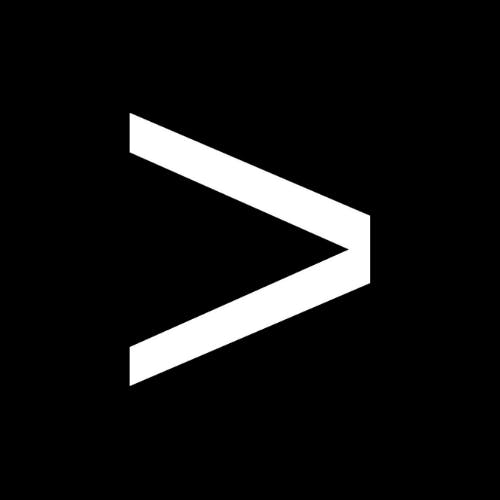
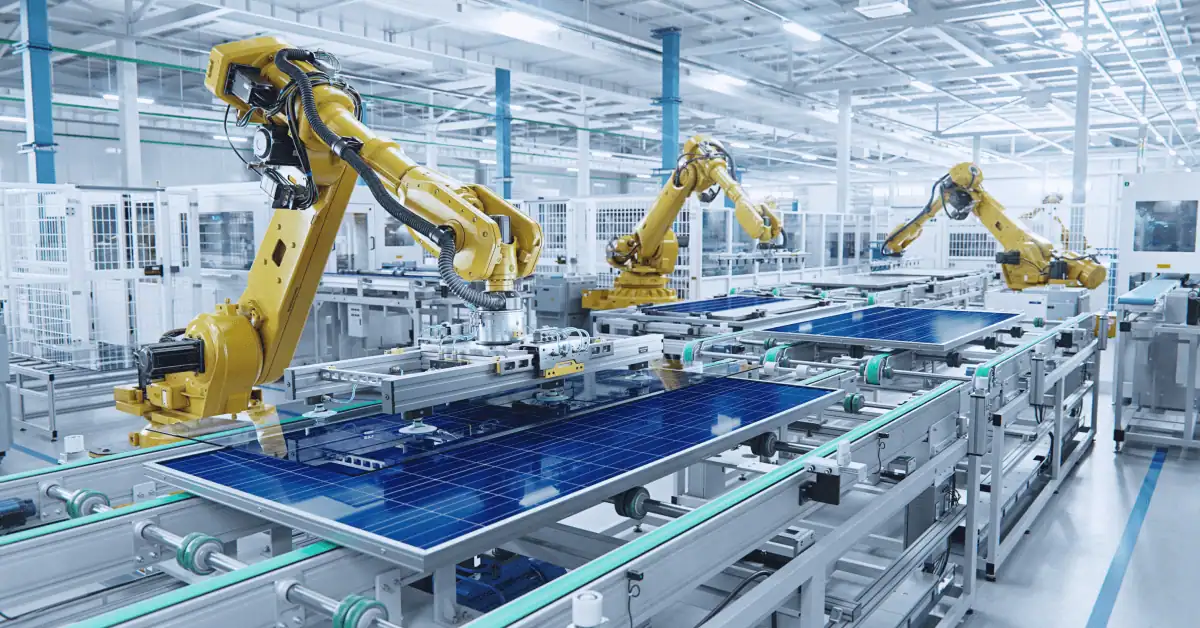
Kaizen, 5S, and value stream mapping (VSM) are lean manufacturing principles that help cross-functional teams reduce waste, strive for continuous improvement, and deliver the best quality products.
But how do you make sure you’re creating a good product from the outset? That’s where the 3P approach comes in.
Here are the basics of 3P lean manufacturing to help you determine when to use this lean tool in your operations.
What Is 3P in Lean Manufacturing?
The 3P methodology (also known as a 3P event) stands for Production Preparation Process. It was developed by Chihiro Nakao, the founder of Shingijutsu Consulting, who initially coined it “New Production Preparation” (NPP).
3P is an event-driven manufacturing process where a product’s design and the process for making it are developed simultaneously. The purpose of the 3P lean tool is to reduce — or eliminate — waste, improve production efficiency, and build the best-quality product from the very beginning.
Learn the top 26 lean management tools and techniques for continuous improvement
3P vs Kaizen vs VSM
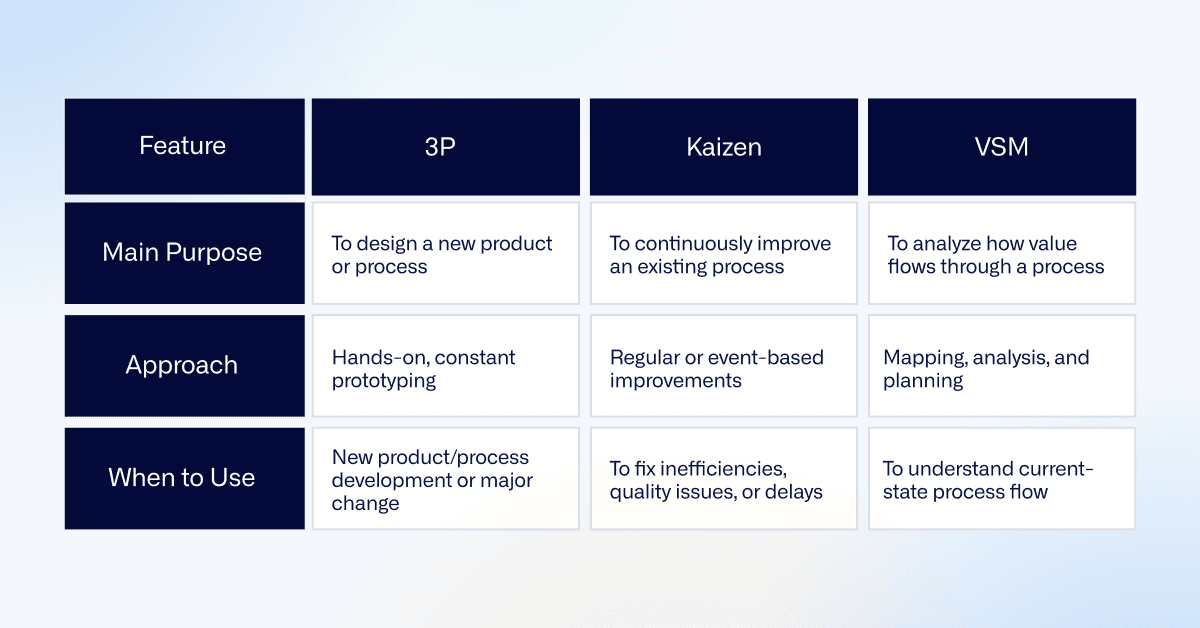
When to Use the 3P Methodology
When is it appropriate to use the 3P lean method?
When Designing a New Product
The 3P model works best when you’re developing a new product from scratch, as it sets your company up to create an efficient system of production with waste minimization and high value in mind.
When Developing a New Production Process (or Dramatically Redesigning an Existing One)
In the case of greenfield projects, or processes being developed without prior infrastructure, 3P can help teams design efficient workflows with baked-in lean principles.
3P is also useful when overhauling existing processes that need more effective workflows to fix efficacy and quality issues.
When in the Planning Stage of a New Facility
Building or acquiring a facility requires a new layout with new equipment. In this case, 3P helps teams design the most optimized setup using lean best practices, e.g., maximizing the space and process flow, reducing unnecessary movement, and enhancing worker productivity.
Phases of the 3P Process
Now that we’ve established various use cases, what are the steps of 3P?
By addressing the production, preparation, and process of manufacturing before getting started, you’ll guarantee a smooth and efficient project that results in the best quality product and meets customer needs.
Let’s take a closer look at how this all comes together:
Production
This first phase includes both the product and its production system; in other words, designing both – product or process steps for how it’s made. At this stage, the aim is to design a product that can be made properly, quickly, and effectively. This lays the groundwork for all other steps.
Preparation
Now that you’ve designed and tested the product and its process, the next step is to prepare for manufacturing. This includes everything from planning and tool setup to material flow. It’s important not to rush through this step, as it establishes the foundation for optimal production.
Process
This phase concerns itself with developing manufacturing standard operating procedures (SOPs) once the processes have been ironed out and refined. The main purpose of this phase is to design manufacturing steps that can be repeated when production is in full swing, and that all material handling and waste elimination have been considered.
Advantages and Disadvantages of the 3P Method
The 3P method is the ideal tool for cross-collaborative problem-solving and innovation. That being said, it isn’t always the most appropriate lean manufacturing tool to use, and it does come with its own limitations.
Let’s take a look at the benefits of 3P as well as some of its challenges.
Benefits of 3P Lean Manufacturing
- Product Design Built Into the Process: There’s nothing like a blank whiteboard to get the juices flowing, which is what 3P allows. By starting from the beginning, teams can apply lean principles to streamline manufacturing processes and develop the best possible products for customers.
- Eliminate Waste and Lower Costs: All that product and process design leads to avoiding waste. Simpler designs with fewer parts are easier and less expensive to make and ultimately lowers manufacturing costs, which can be passed through to your customers.
- Cross-Functional Collaboration: The brightest minds from across departments are involved in this multi-day 3P event. What better way to create than to bring a diversity of talents, skill sets, and experience to the table?
Disadvantages of 3P Lean Manufacturing
- Potential Inefficiencies: It sounds counterintuitive, but there is a risk of introducing a new inefficiency when starting from scratch. Since everything is new and untested, it’s always a possibility that unforeseen issues can arise. Testing and prototyping early and often will help, but it may also take time to fix these issues.
- Resource-Intensive Process: 3P demands a lot of time and effort from your team members, not to mention the financial investment. Implementing 3P is best handled by teams who already have experience with lean methods, as they’ll be better equipped to get started.
- More Complex Coordination: The collaborative nature of 3P events is a benefit as well as a challenge. If you can imagine how difficult it is fitting in a regular business meeting with various department heads, you can see how coordinating a 3P is even more complex and likely needs to be scheduled well in advance.
Production, Preparation, Process: Is This the Method You’re Looking For?
3P is more than just a lean management tool. It’s a philosophy of efficiency, teamwork, and quality that touches every level of an organization. Is it right for you? Take a look at our list of the top 26 lean tools for continuous improvement.