Essential Lean Management Tools for Manufacturers
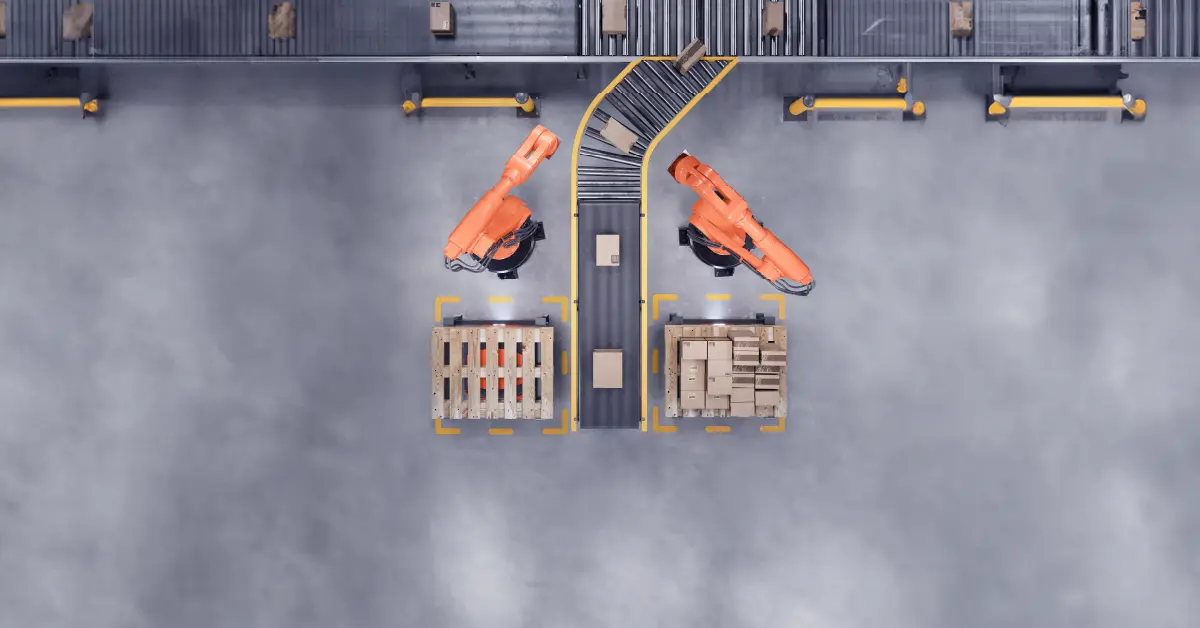
Lean management tools are widely prevalent today, nowhere more so than in manufacturing. Arising from the Toyota Production System (TPS) that revolutionized Japanese manufacturing in the 1950s, all lean management tools have a singular goal: eliminating waste and thus creating a leaner organization.
The guide below provides an overview of 26 top Lean management tools, including:
1. Plan-Do-Check-Act
2. Standardized work
3. Value stream mapping
4. Visual factory
5. 5S
6. Root cause analysis
7. A3 Problem-Solving
8. The three M’s
9. Just-in-time production
10. Takt time
11. Continuous flow
12. Jidoka
13. Heijunka
14. Kanban
15. Andon
16. Bottleneck analysis
17. Gemba
18. Hoshin Kanri
19. Kaizen
20. Poka-yoke
21. Single-minute exchange of die (SMED)
22. Six big losses
23. Total productive maintenance (TPM)
24. Overall equipment effectiveness (OEE)
25. SMART goals
26. Key performance indicators (KPIs)
Download your free Root Cause Analysis 101 Guidebook for an overview of common root cause analysis tools
1. Plan-Do-Check-Act
Lean manufacturing centres on the Plan-Do-Check-Act (PDCA) process developed by early founders of the quality management movement. PDCA is an iterative, closed-loop approach to continuous improvement focused on four steps:
- Plan: Documenting processes or objectives
- Do: Executing procedures or other actions such as problem-solving and plant floor audits and inspections
- Check: Measuring your results to see if you met your goals
- Act: Take additional measures based on whether you met your objectives, which feeds back into the beginning of the process at the Plan step, integrating lean Six Sigma methodologies.
This process can be applied to quality problem-solving, for instance:
- Plan: Identify the problem, conduct root cause analysis and select countermeasures
- Do: Implement countermeasures and plant floor checks to ensure they are in place
- Check: Going back to the original problem to evaluate whether the countermeasure was effective
- Act: Adding new countermeasures or going back to root cause analysis if the problem wasn’t solved
2. Standardized Work
Standardized work is the foundation of Lean and the PDCA process, and the ultimate goal of continuous improvement. Without a standard to compare against, there can be no improvement. Standardized work is based on:
- The rate parts need to be manufactured (takt time)
- The precise sequence of steps the operator must follow
- Inventory units are required to keep operations running smoothly
This information is summarized in a standardized work chart, which is typically displayed alongside work instructions as visual management tools at the workstation. These should be continuously reviewed and updated in response to events such as process changes and quality escapes.
3. Value Stream Mapping
Value stream mapping helps visualize the entire production process from raw materials to product shipment. Value stream maps allow teams to:
- Visualize the flow of materials and information within the process
- See how different elements of the process interact
- Identify inefficiencies and non-value-added activities to eliminate
- Understand how solutions will impact the process
4. Visual Factory
Lean management tools heavily emphasizes visual management as a way to better communicate essential information to workers. Examples of visual factory tools include:
- Andon systems using colored lights to display the status of production lines
- Kanban cards used to remind people when to reorder materials
Markings on the plant floor delineating walkways, storage areas and safety zones - Shadow boards with tool-shaped outlines to show where tools are missing or out of place
- Visual management boards that display key performance indicators (KPIs) and problem-solving efforts in production areas
5. 5S
5S is a Lean management tool focused on keeping a clean, organized work station to ensure more efficient, high quality work. Translated from Japanese, 5S stands for:
- Sort (seiri): Eliminate all unnecessary items from the workstation.
- Set in order (seiton): Organize remaining essential materials, providing designated locations so everything is clearly labelled and where the operator needs it.
- Shine (seiso): Clean up the work area, including floors, walls, surfaces and equipment.
- Standardize (seiketsu): Create and follow a daily cleaning and maintenance schedule.
- Sustain (shitsuke): Instill the habit of following seiri, seiton, seiso, and seiketsu to hold gains in place, as a best practice in lean manufacturing.
6. Root Cause Analysis
Root cause analysis is a tool for understanding the underlying cause of problems so you can solve them effectively. Manufacturers use a variety of root cause analysis tools depending on the nature and context of the problem, including:
- 5 Whys
- Fishbone diagrams (a lean six sigma tool used to improve quality)
- Pareto charts
- Scatter diagrams
- Failure mode and effects analysis (FMEA)
7. A3 Problem-Solving
A3 is a Lean management tool that communicates the PDCA problem-solving process on a single sheet of paper. A3 is named for the oversized (A3) paper used in this process, with A3 reports typically covering:
- Problem description
- Background in applying lean manufacturing tools and methodologies
- Current state
- Root cause analysis
- Target state
- Action plan
- Follow-up
8. The Three Ms
The three Ms represent the three types of waste that Lean aims to eliminate. These are:
- Muda: Any activity that does not create value, such as moving materials multiple times between different steps in an assembly process
- Mura: Unevenness in operations or work pace, causing a mad rush at times and idling at others
- Muri: Overburden of equipment or people that causes them to work harder or faster than is appropriate for the equipment or process
Gain the knowledge to transform your processes with our comprehensive eBook on Root Cause Analysis. Access your copy and begin mastering the art of pinpointing and resolving core issues with precision!
9. Just-in-Time Production
Just-in-time production is a Lean concept that focuses on manufacturing parts based on current as opposed to projected demand. By only creating products on demand, manufacturers don’t need to store excess inventory onsite, reducing inventory costs and waste. It also creates a smoother workflow and improves productivity, since the team is only focused on work in progress and non-value-added activities are eliminated.
10. Takt Time
Takt time is a core pillar of the Toyota Production System. Closely related to Just-In-Time, takt time ensures a steady rate and continuous flow of production precisely matched to customer demand. The result is that the right amount of materials is at the right place at the right time in the production process, reducing waste and unevenness.
Takt is a German word translating to rhythm or pace. It is, in essence, the pulse of the plant. If a customer orders a product once every 60 seconds, then a product should be rolling off the line every 60 seconds. To calculate takt time, you divide the available daily production time by daily customer demand.
Let’s say, for instance, a plant runs eight hours (27,600 seconds) a day and customers order 300 finished products daily. Takt time is thus 92 seconds, which is the rate the plant must manufacture a single product to meet demand.
11. Continuous Flow
Related to Just-in-time production, continuous flow is about producing one item at a time through a flow of steps as opposed to making products in batches. The idea of continuous flow is to create a streamlined, constant flow of products to:
- Increase throughput with minimal downtime
- Use lean strategies to reduce excess inventory, waste, and costs
- Level out production and identify defects more effectively
- Shorten lead times to improve customer satisfaction
12. Jidoka
Another core pillar of the Toyota Production System, Jidoka is a Japanese term that translates to autonomation, or intelligent automation. Jidoka enables machines to immediately stop when an abnormality is detected, which serves several purposes:
- The equipment detects bad parts without constant monitoring, allowing operators to work on more than one machine
- Quality is built into each step
- Root causes of problems are more visible since machines stop when problems first arise
13. Heijunka
Heijunka or production leveling is aimed at reducing unevenness and overburdening in the production process. The idea is to create a steady, efficient production schedule that meets demand while also minimizing waste.
Heijunka principles focus on:
- Using demand variation analysis to understand how customer demand fluctuates
- Producing smaller batches of product consistently rather than large batches in response to demand spikes
- Mixing the production of different product variants to prevent overproduction of any given product
- Balancing the workload among different work areas to prevent bottlenecks and overburdening
14. Kanban
A Kanban is a pull system that uses a series of cards to indicate when it’s time to resupply materials. Kanban reduces the need to maintain inventory onsite, which in turn reduces waste related to excess inventory and overproduction. Parts are delivered to the production line on an as-needed basis, rather than estimating needed stock levels.
15. Andon
Andon is a manufacturing signaling system that alerts operators and managers to production line problems using red, yellow and green lights:
- Greenlight: Production is normal.
- Yellow light: A problem has been detected requiring assistance.
- Red light: The production line has stopped.
An Andon system may be triggered automatically when equipment detects an issue, or it may be triggered by an operator pulling an Andon cord above the production line.
16. Bottleneck Analysis
Bottleneck analysis is a tool for identifying constraints that slow down the manufacturing process. By removing unnecessary bottlenecks through structured analysis, manufacturers can increase efficiency and throughput. Bottleneck analysis uses a variety of tools and techniques, including :
- Breaking the production process down into individual steps to visualize the flow of materials and information among them
- Collecting data on production rates, cycle time and throughput at each step, including any delays between them
- Identifying places that limit the production rate and create delays, such as workstations with long cycle times or a large queue of work
- Analyzing the cause of the bottleneck, whether it’s an equipment issue, resource constraint or other problem
- Implementing solutions addressing the root cause of the bottleneck, with continuous monitoring and adjustment to the process
Boost your quality control with our expert LPA Guide. Tap into the potential of Layered Process Audits—download your guide now!
17. Gemba
In Japanese, Gemba refers to the actual place where work is done, referring to the plant floor in manufacturing. In Lean, gemba walks are a practice for directly observing conditions on the plant floor to identify areas for improvement. Teams may also go to the gemba to write work instructions, or to follow the flow of a product from end to end to identify inefficiencies.
18. Hoshin Kanri
Hoshin Kanri or policy deployment is a seven-step planning method based on PDCA that aligns strategy, tactics and execution across the organization. Hoshin Kanri ensures everyone is working toward the same goal, eliminating waste associated with poor communication and inconsistent direction.
The seven steps are as follows:
1. Create the organizational vision, including current and future goals.
2. Establish long-term breakthrough objectives that will deliver a substantial change in performance.
3. Identify annual objectives that break down long-term goals into yearly targets.
4. Deploy objectives so that everyone in the organization understands their role in achieving strategic goals.
5. Implement annual objectives by coordinating action plans at all organizational levels.
6. Conduct monthly reviews to assess progress and make adjustments.
7. Conduct annual reviews to reflect on the year’s progress, evaluate strategy effectiveness and refine the next year’s Hoshin Kanri.
19. Kaizen
Loosely translated, kaizen is a Japanese term that means continuous improvement. Kaizen centres on incremental changes to processes that add up to bigger improvements over time. Kaizen emphasizes employee engagement, where the entire team is encouraged to contribute ideas and solutions.
Kaizen also aims for quick wins and is based on the PDCA process. Daily kaizen helps build a culture of continuous improvement, while kaizen events are quick-burst projects typically lasting three to five days. For example, if you’re launching layered process audits in your plant, you may hold a kaizen event to kickstart the process and get everyone up to speed quickly.
20. Poka-Yoke
Poka-yoke or error-proofing is a tool aimed at incorporating defect detection and prevention into the work process itself. Poka yoke as a process analysis tool looks at where problems can occur, and then designing the process to prevent them from happening.
For example, manufacturers may use poka yoke devices such as sensors to detect abnormal conditions in the process to trigger a shut down. A red rabbit test involves running a known defective part through the poka yoke device to verify that it’s working.
21. Single-Minute Exchange of Die (SMED)
Single-Minute Exchange of Die (SMED) is a Lean tool for minimizing changeover time, ideally less than 10 minutes. This is achieved primarily by converting as many changeover steps as possible to external setups that can be completed while the machine is still running. From there, remaining setup steps are simplified and streamlined, reducing the number of steps overall.
By reducing setup time to single digits, SMED helps plants:
- Minimize downtime and associated costs
- Produce smaller lots by enabling frequent product changes and thus flexible scheduling and increased customer responsiveness
- Reduce inventory levels and costs
22. Six Big Losses
The Six Big Losses refer to the most prevalent causes of manufacturing waste and productivity loss, which include:
- Equipment breakdowns
- Machine setups and adjustments
- Minor stoppages
- Lower operating speeds
- Increased scrap
- Rework
Preventing these losses are a key focus of total productive maintenance (TPM) and measuring overall equipment effectiveness (OEE).
23. Total Productive Maintenance (TPM)
Total productive maintenance (TPM) focuses on reducing equipment downtime and increasing productivity by sharing maintenance responsibilities across the entire team. Rather than making maintenance the responsibility of the maintenance department, everyone from managers to operators to quality engages in TPM.
Key aspects of TPM include:
- Autonomous maintenance, where operators are responsible for routine upkeep such as cleaning, lubricating and inspecting machines
- Preventive maintenance aimed at preventing equipment breakdowns through scheduled maintenance and part replacement to identify potential issues
- Corrective maintenance to restore function after unexpected breakdowns
- Maintenance prevention through use of equipment that requires less maintenance, such as using equipment with a corrosion-resistant coating
24. Overall Equipment Effectiveness (OEE)
Overall equipment effectiveness (OEE) is a TPM metric that describes how effectively machines are running, and is based on three metrics:
- Availability rate: The percentage of time equipment is running as scheduled, which is reduced by downtime related to maintenance, changeovers and breakdowns.
- Performance rate: The percentage of time machines are running at optimal speed, which is reduced by slower cycle times and minor stoppages.
- Quality rate: The proportion of good products produced in comparison to total manufactured, which is reduced by scrap and rework.
OEE is thus calculated by multiplying availability, performance and quality rates.
Example:
Availability: 92%
Performance: 95%
Quality: 98%
0.92 x 0.95 x 0.98 = .856 or 85.6% OEE
25. SMART Goals
Lean and other process improvement frameworks emphasize that effective goal-setting requires that goals be SMART, an acronym for:
- Specific: Goals should clarify what you’re trying to achieve, who should be involved, why it is important and how it will be accomplished.
- Measurable: Quantifying your goal is essential to measuring progress and evaluating success.
- Attainable: Goals should be realistic if you expect to keep your team motivated.
- Relevant: Goals should be aligned with the organization’s larger objectives and mission, ensuring you focus on what truly matters.
- Time-bound: Your goal should include a timeframe for completion to keep the process on track.
26. Key Performance Indicators (KPIs)
Key performance indicators (KPIs) are metrics that allow you to track progress toward strategic goals. KPIs should be chosen carefully and communicated across the organization so that everyone is united around common goals.
KPIs fall into one of two categories:
- Lagging indicators that are results-oriented and describe past performance, such as scrap rate and OEE
- Leading indicators that are process-oriented and correlate with lagging indicators, such as the number of audits performed over a given period or corrective action closure time
While these Lean tools are powerful on their own, it’s important to remember that Lean is more than just a collection of tools. Rather, it is a way of operating a business—and sustaining success—across all levels of the organization. Lean tools help improve efficiency and productivity by reducing waste, but without a Lean mindset, the company won’t reach its full potential.
Lean training and experience with the PDCA process can help lay the groundwork while communicating goals and benefits is key to gaining organizational buy-in.