Lean Visual Management Board Basics
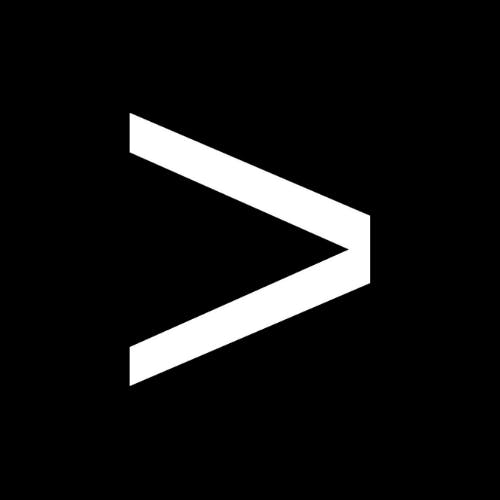
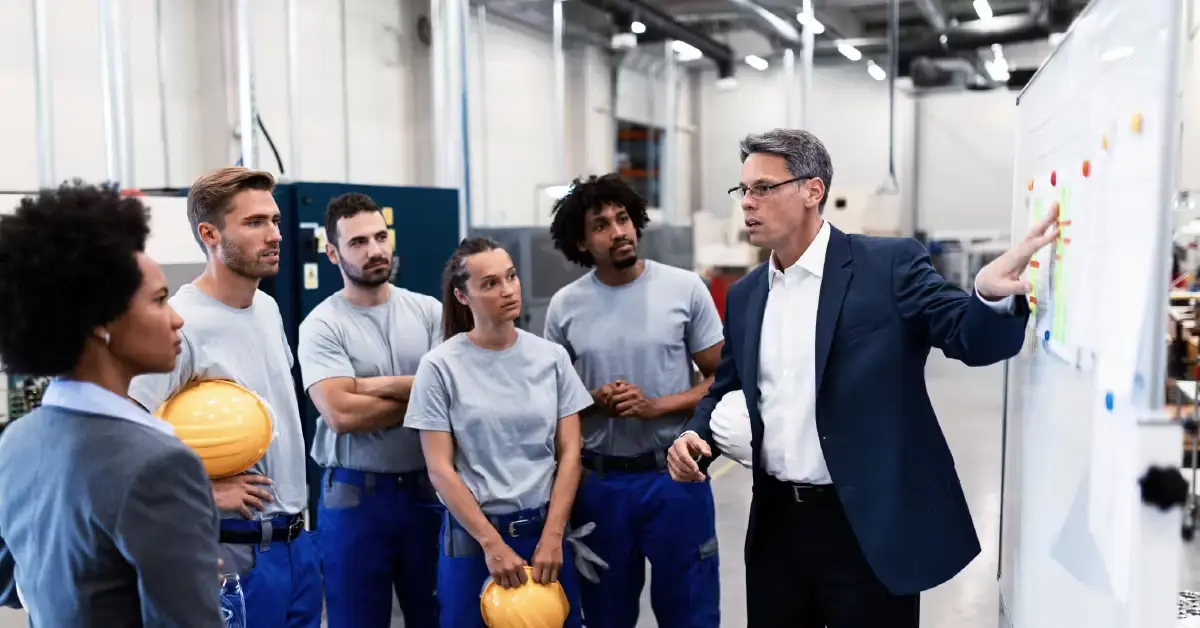
In the manufacturing industry, making problems visible is the first step to resolving them effectively.
Consider a scenario, for example, where an assembly line worker inspects finished parts and records the results on a computer spreadsheet. That data is later analyzed, with results reported back to the production team and management.
Now imagine that information is recorded live on a Lean visual management board in the work area, providing real-time feedback to operators doing the work.
Which scenario is more likely to help the team identify and correct the problem quickly? Obviously, it’s the second.
Visual management boards are a popular tool for communicating key information to workers, putting data front and center on the plant floor rather than hidden in spreadsheets. For those new to Lean visual management boards, this post provides a basic overview on best practices, how to use them and pitfalls to avoid.
Download your free Root Cause Analysis 101 Guidebook to learn about common root cause analysis tools
What is a Lean Visual Management Board?
A lean visual management board is a communication tool used in manufacturing to share information like key performance indicators (KPIs) and status of problem-solving initiatives. Visual management boards may be a physical white board or hanging poster, or may be a digital display. Manufacturers use lean visual management boards for a variety of processes such as quality, safety, production and more.
What Does a Visual Management Board Include?
A lean visual management board should provide a clear snapshot of information on the specific process, project or area of focus. While specific elements will depend on the goal of the visual control board, they often include:
- KPIs such as production targets, cycle times, defect rate or incidence rate
- Visuals such as charts, graphs and process flow maps
- Performance trends over time based on historical data
- Details of problem-solving steps such as Plan-Do-Check-Act or root cause analysis visuals like 5 Whys or fishbone diagrams
Learn More about Lean Management Tools
Benefits of Lean Visual Management Boards
Lean visual management boards are dynamic tools that offer manufacturers many benefits, including:
- Better Communication: Visual management boards provide a place where the entire team can see the status of ongoing issues. This improves communication among team members and different shifts, reducing the risk of miscommunication and errors.
- Timely monitoring: Visual management boards can enable real-time monitoring of process information such as safety performance, quality KPIs and production metrics. This allows teams to quickly identify and respond to problems as they arise during the process.
- Improved accountability and engagement: Making targets and responsibilities clearly visible ensures team members are accountable for their contributions to the process. It also gives them a greater sense of purpose and ownership over their work.
- Accelerated problem-solving: Process data stored in spreadsheets isn’t helpful for making real-time corrections. Visual management boards enable faster correction of problems on the plant floor, leading to fewer downstream defects and quality issues.
Types of Lean Visual Management Boards
Manufacturers use a variety of visual management boards on the plant floor to communicate real-time production, safety and quality information to workers. Types of lean visual management boards include:
- Production control boards
- Quality control boards
- Safety tracking boards
- Inventory management boards
Below we discuss each of these in further detail, and how manufacturers use them to promote better decision-making and problem-solving.
Production Control Boards
A production status board gives teams an overview of key production metrics, such as:
- Production targets
- Actual output
- Cycle time
By putting this information in view of workers, employees can easily see what they need to do and whether they’re hitting their targets. Management can also quickly assess production status, identify bottlenecks and take action to address any delays or production issues.
Quality Control Boards
Quality control boards help manufacturers communicate a wide range of quality data, helping maintain a high level of process and product quality. Quality control boards may show KPIs on first-time quality, scrap rates or customer returns. Real-time information on product defects and inspection results can also help workers pinpoint and resolve problems faster to minimize quality escapes.
Other types of quality control boards include:
- Layered process audit (LPA) boards: Organizations that conduct LPAs to maintain process adherence may use LPA boards to manage these frequent audits and communicate results. An LPA board may display information on scheduled vs. completed audits, audit completion rate and audit findings.
- Kamishibai boards: Some companies use Kamishibai boards to manage checks such as 5S audits or LPAs. Kamishibai boards display colour-coded T-cards that make it easy to see whether a scheduled check has been completed, as well as instructions for performing the audit.
Improve productivity with LPAs
Fast Response Boards
Fast response boards are used to coordinate quick action around high-priority quality issues such as A3 problem-solving efforts. During daily or pre-shift meetings, team members get together got-to assess whether they are hitting key metrics and any obstacles that need to be resolved.
While most visual management boards are aimed at operators, fast response boards are aimed at one level above operators, including supervisors, technicians and set-up people.
Safety Information Boards
A safety information board displays critical communications about safety procedures and performance. In addition to safety guidelines and procedures, safety information boards may display key information related to safety performance, such as:
- Number of incidents
- Number of days since the last incident
- Near-miss data
Inventory Management Boards
One key tenet of digital lean manufacturing is optimizing inventory levels. Inventory management boards help track the flow of raw materials through work-in-progress and finished goods. Inventory management boards may use visual cues like colour-coded Kanban cards to make it easy to see:
- Current inventory levels
- Reorder points
- Lead times
- When to reorder materials
Getting the Most from Your Visual Management Board
Lean visual management boards are typically large, displayed prominently in work areas where people can easily see them. Just as important, visual management boards should have clear targets—and people should immediately be able to tell if the team is hitting them.
Below are some additional tips to consider to help you get the most from your visual management board:
- Update them regularly: It’s critical to ensure that information on the board is up-to-date. There should be specific responsibilities assigned to update the board on a defined schedule.
- Use simple visuals: Avoid excess detail and color, using color-coding, graphs and charts to communicate essential information quickly and clearly.
- Standardize symbols and colors: Using a standardized set of symbols and colors ensures consistency, which in turn helps people better understand vital information.
- Define your goal: What is your objective for the visual board? Defining a clear purpose is key to making sure the data you present it meaningful to the team.
- Evaluate effectiveness: You should regularly review the board and make adjustments based on team feedback on whether the board is effective and how to make it so.
- Recognize good work: Leaders should use visual management boards to celebrate improvement and milestones.
- Ensure accountability: Visual management boards can be used to track tasks and hold team members accountable in a visible way. Updating the board should also be a shared responsibility, promoting shared ownership over tracking progress and monitoring performance.
Common Mistakes with Visual Management Boards
There are several critical pitfalls to avoid when using visual management boards in your plant. The most important to watch out for is failing to update them regularly. When visual management boards contain outdated information, they can confuse people. Eventually workers may learn to ignore them, and overall buy-in for quality efforts suffers as employees don’t see it as a priority for management.
The second major mistake, related to the first, is lack of leadership involvement in the process. What problems does the board reveal? What is being done to understand and resolve them? Management must be closely involved in identifying issues and addressing bottlenecks in the process, as well as assessing where similar problems might also be occurring.
Other mistakes to avoid include:
- Cluttered boards: Overly complicated boards with excess information can lead to overwhelm. Focus on key metrics and standardized visuals to ensure clarity.
- Inadequate training: Employees need training on how to read and interact with visual management boards.
- Poor placement: Boards should be highly visible close to where the relevant team works, as opposed to hidden in a hallway.
Generating Data for Visual Management Boards
Keeping visual management boards updated with current data is essential to continuous improvement. Companies can draw on a variety of data to populate the boards, including:
- Plant floor audit and inspection data
- Safety performance data related to incidents, near-misses and observations
- Corrective actions, customer complaints and problem-solving activities
Digital audit and inspection software like EASE, for instance, can be used to populate visual management boards with data from audits like LPAs, showing audit completion rates and process failures by work area. This can help keep teams focused on completing their scheduled audits and inspections, while also making visible process issues that can lead to defects, scrap and complaints.
Lean visual management boards are powerful tools for promoting continuous improvement in areas like quality and safety. By making data visible, they improve communication and problem-solving, putting data in the hands of those who arguably need it most: frontline workers. Getting it right means making boards clear and updating them frequently, involving leadership in the process to gain buy-in and accelerate the resolution of issues.