Plant Floor Audit Software: Should You Build vs. Buy?
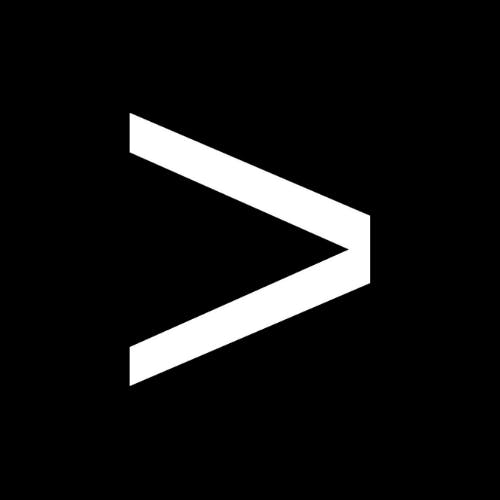
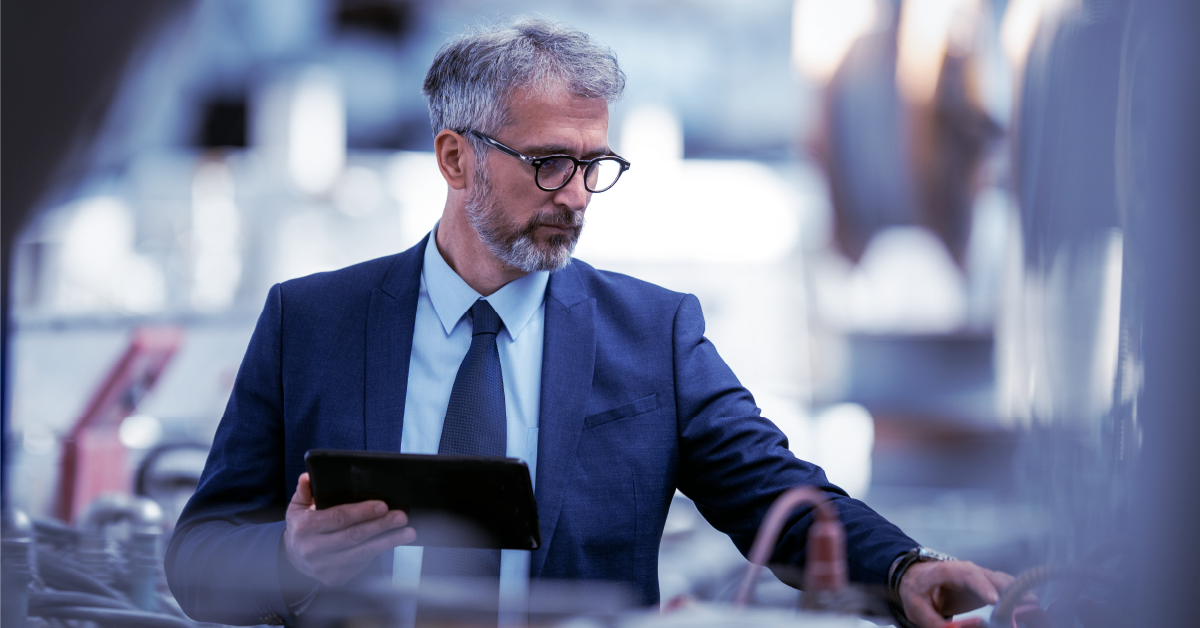
Spreadsheets and paper checklists are a common starting point when implementing plant floor audits.
What many find, however, is that the complexity of managing audits can get in the way of results.
Scheduling and manually entering findings takes hours. Updating checklists means recalling old versions and distributing new ones, making it hard to keep checklists fresh. Visibility into findings and follow-up is minimal, so that it’s unclear whether issues have been resolved.
Once plants realize they aren’t achieving value with this method, the next question becomes: should you build vs. buy a plant floor audit solution?
Below we compare the drawbacks and benefits of homegrown systems with an off-the-shelf solution, including which functions are most essential to success.
Download a whitepaper on The Business Case for Layered Process Audit Software
Building a Homegrown System
There are several reasons why manufacturers build plant floor audit systems in-house. Chief among these are cost and the ability to customize the system, as well as security concerns.
However, building your own plant floor audit software in-house also has several drawbacks, including:
- Internal resource constraints: Limited in-house resources can delay projects, especially in terms of allocating budget for what’s viewed as a niche project.
- Limited functionality: Internal teams may lack the expertise to build a solution that addresses the unique challenges of plant floor audits. This means you may have to adapt your processes to the software’s limitations, which hinders efficiency and continuous improvement.
- Hidden costs: While it may seem cheaper to build a system, total cost of ownership can be higher than software when accounting for labor, infrastructure and maintenance costs.
- Maintenance concerns: Pushing out updates and fixing bugs requires dedicated support. If this isn’t done in a timely manner, it can affect functionality—or whether people use the system at all.
- Potential loss of institutional knowledge: Should the program owner or architect leave the company, much of the development knowledge will go with them.
- Opportunity costs and risks: In the time it takes to build a system, companies may miss crucial opportunities to proactively prevent quality escapes and improve processes.
This last point is important given the potentially high cost of even a single quality escape and the resulting impact on customer relationships. It’s also critical in the context of reducing quality costs, considering the faster time-to-value with an off-the-shelf solution.
Buying Off-the-Shelf Plant Floor Audit Software
Of the companies that build their own audit system, a subset of those eventually purchase software due to the advantages it provides. Some of the biggest of these are:
- Accelerated quality cost reduction: Manufacturers have reported significant reductions in defects and complaints with solutions like EASE, including a 50% reduction in quality costs.
- Built-in expertise: A specialized plant floor audit solution comes with built-in best practices informed by years of expertise helping manufacturers achieve their continuous improvement goals. A vendor that works with a variety of customers can also bring fresh ideas and experienced support to streamline the implementation process.
- Transparent pricing: With plant floor audit software, you know what the cost will be up front, avoiding cost overruns and added costs for labor and maintenance.
- Specialized audit features: A purpose-built audit platform can provide sophisticated features like layered scheduling, question randomization and a sleek mobile audit app to increase engagement. Custom dashboards and reporting by layer, station, department or shift also help teams spot patterns and risks while making it easy to communicate performance results with the organization.
In terms of security, many plants also find software is more reliable than hosting servers onsite and provides enhanced security measures to keep data safe.
Finding the Right Solution for Your Plant
As you consider whether to build vs. buy, you’ll want to compare capabilities in several key areas:
- Audit administration
- Mobile audit functionality
- Reporting
Audit Administration
Some critical functions to consider here are the ability to:
- Create your annual audit schedule in just a few clicks
- Schedule audit frequency by layer of management, for example with layered process audits
- Easily add or remove different types of questions (e.g. pick list, multiple choice, yes/no) and tag them by category or location
- Rotate checklist questions and control the ratio of different categories included (e.g. quality, safety, 5S)
- Include visual standards in checklist questions for added clarity
- Send automatic reminders and track audit completion rates
Mobile Audits
A few of the most helpful functions in this area are the ability to:
- Access digital checklists on a smartphone or tablet from an email link
- Upload photos to the audit record to accelerate problem-solving
- Include conditional questions and failure categorization for deeper insights
- See recent findings for failed questions during the audit
- Document mitigations and launch additional action items for accountability and tracking
Reporting
In terms of reporting, you’ll want to make sure any solution you build or buy enables:
- Real-time access to audit findings
- Drill-down reporting into specific shifts, departments, production lines or audit layers
- Single and multi-site reporting
- Custom dashboards so leaders see the most relevant metrics to their roles
- Integration with business intelligence platforms for deeper analysis
While an in-house software build may seem attractive, it comes with significant downsides. Off-the-shelf solutions like EASE provide a faster path to quality improvement along with a high degree of customization and control. The result: you spend less time managing technology and more time generating insights that drive continuous improvement.