Gemba Walk Examples and Best Practices for Manufacturers
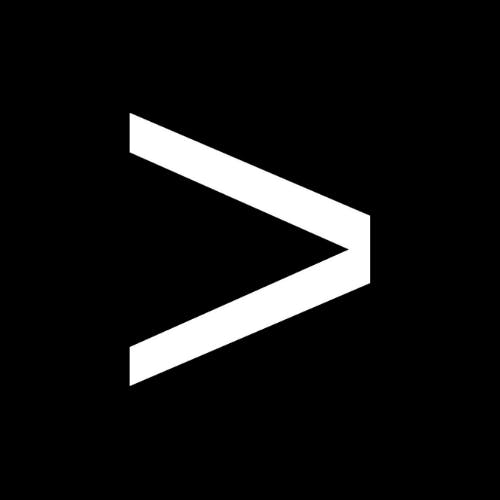
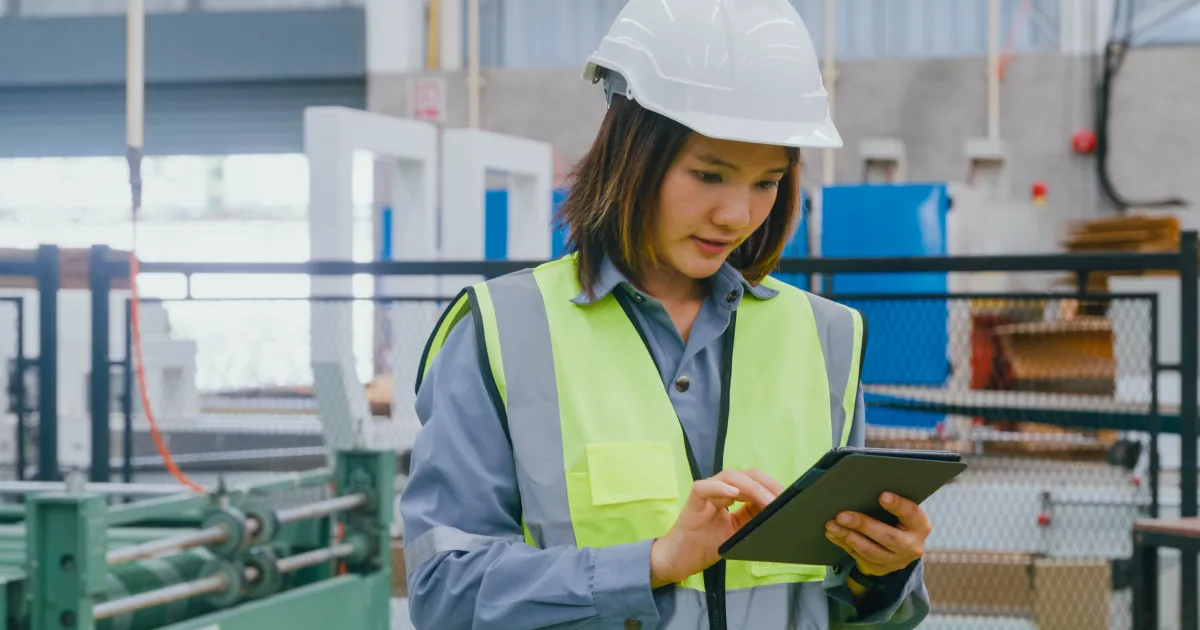
Whether you’re talking about problem-solving activities or continuous improvement projects such as Kaizen initiatives, there’s one phrase that you’ll hear often in manufacturing: go to the Gemba.
What this means is you have to go to the real place where work is done—or Gemba, in Japanese—to see firsthand what’s going on in the process.
This is the concept behind Gemba walks, a Lean tool that uses plant floor walkthroughs to observe processes and gain insights through conversations with frontline employees.
This article looks at Gemba walk examples in more detail, including:
- Gemba walk core principles and benefits
- How to structure effective Gemba walks
- How to create Gemba walk questions
Download your free Gemba Walk Checklist Template for help getting started with Gemba walks
What Is a Gemba Walk?
A Gemba walk is a Lean tool that involves management walking the plant floor to observe processes firsthand. Conducting Gemba walks can help identify continuous improvement opportunities and aid in problem-solving activities, while helping to build a culture of quality. Gemba walks are based on three principles:
- Go see
- Ask why
- Show respect
Gemba Walk Principles
Go see, ask why and show respect: these essential principles should form the basis for every Gemba walk. How can you make sure you’re getting them right? Below, we look at each of these three principles in closer detail.
Go See
Gemba is a Japanese term translating to ‘the actual place,’ referring to the actual place where work is done. This concept is important because it underscores the fact that quality isn’t an activity that can just be done behind a desk.
Instead, management must be willing to go to the plant floor and see with their own eyes the details and challenges around how the work is done. Nothing can replace this in-person observation when it comes to solving problems, understanding processes and connecting with employees.
‘Go see’ also points to the idea that during Gemba walks, your role is not to critique employees, nor is it to issue on-the-spot corrections. Rather, your role is to gather information through observation and conversations with frontline employees and to work together on problem-solving.
Ask Why
The second principle of Gemba walks is to ask why. Gemba walks aren’t just about identifying problems or running through a list of checklist items. They’re about digging down to find out why things are done a certain way, so that effective solutions or improvements can be designed.
One helpful tool here is the 5 Whys method, which involves asking why five times in succession to peel back increasingly deeper layers of a problem.
This deeper understanding is essential to both process improvement and getting to the true root cause of problems. Asking why is also especially useful in uncovering hidden factory issues, which we discuss later in this article.
Show Respect
The final principle to follow when conducting Gemba walks is to show respect. In practical terms, this means:
- Setting the tone that you aren’t there to find mistakes, but to collaborate on solutions
- Engaging in interactive, solutions-focused conversations with operators
- Asking for employee input and feedback on their experience and what they think would make the process better
- Focusing on processes, not people, seeking first to understand
- Taking action based on operator input, whether it’s solving a problem shared during your discussions or using their feedback when developing solutions.
Showing respect is a critical part of gaining employee buy-in for your quality efforts. When people feel their input is valued—and that management will take action to solve problems—it demonstrates that quality actually does matter to leadership. Employees, in turn, are more likely to take ownership of quality issues they run across in their day-to-day jobs themselves.
Gemba Walk Benefits
While Gemba walks provide opportunities to promote continuous improvement, the biggest benefits are to your organizational quality culture as a whole.
Key benefits of Gemba walks include:
- Enhanced communication: Gemba walks provide a direct line of communication from frontline employees to management, while also opening up regular conversations about issues that are critical to quality.
- Management presence: Doing regular Gemba walks makes leadership a visible presence on the plant floor and demonstrates management’s commitment to quality.
- Improved morale: Making people feel valued and safe in their roles helps boost morale and create a culture of quality, one where people know that their work and their daily experiences matter to leaders.
- Accelerated problem-solving: Direct process observation and conversations with operators can often uncover new aspects of a problem that might not have been considered previously. Employing principles of lean manufacturing can optimize this approach. Management can provide guidance based on similar problems they have seen, while frontline employees may have valuable input in coming up with solutions to problems.
- Corrective action verification: Gemba walks give leaders the chance to check in on the status of previous problem-solving activities, verify they are still working and determine appropriate actions if they are not.
How to Structure and Plan Your Gemba Walk
Gemba walks are more freeform than structured checks such as layered process audits, giving plant managers the opportunity to ask open-ended questions and have more in-depth discussions. However, that doesn’t mean Gemba walks are completely unstructured, or that management is just wandering around during them.
Gemba Walk Themes
One way to give structure to your Gemba walks is to organize them around a specific theme that relates to your plant’s current quality initiatives or goals. These could include themes such as:
- A specific Lean project or Kaizen event
- Safety
- Productivity
- Tools and resources
- Continuous improvement
- 5S
Using a Mapped Route
Another common approach to structuring Gemba walks is to conduct them along a mapped route.
Let’s say, for example, you have a staff meeting or a fast response meeting at the start of the first shift. After the meeting, the plant manager and team would go on a short walk along one of a dozen pre-mapped routes. For instance, one day you might visit stamping, then the next day doing a walkthrough of welding, and so on.
Some plants choose to schedule them in advance, or you might opt to select the route you’ll follow randomly each day, such as picking them out of a hat.
Gemba Walks and Problem-Solving
Many plants use Gemba walks as a follow-up tool around problem-solving. Here leadership identifies an open 8D investigation or quality issue and then visits the specific work center to put eyes on it.
Creating Your Gemba Walk Questions
Whether you’re focusing on a specific theme, work area or mapped route, it’s helpful to prepare a Gemba walk checklist in advance to guide your conversations. Your Gemba walk questions should be aimed at generating discussion and feedback from operators, focusing on areas such as safety, quality, delivery and materials.
Below are some potential Gemba walk questions you might include on your checklist:
- Have you noticed any safety issues recently?
- Have you noticed any recent quality issues at this station?
- Are you having to do anything unusual?
- Have you seen any unexpected changes in parts lately?
- Is there anything that’s making it harder to produce good parts?
- Are your daily boards such as those for tracking productivity and scrap all up-to-date?
- Are you hitting your hourly delivery rate, and if not, what’s getting in the way?
- Is the machine running the way it’s supposed to?
- Have there been any major downtime or scrap events?
- Have there been any recent material outages?
- Have you seen any problems with supplied materials that we should know about?
When using them to follow up on problem-solving, Gemba walk questions to ask at the workstation may include:
- Where are we in the problem-solving process?
- What is the current scrap rate?
- How often are you seeing the defect in question?
- Are containment activities working?
Follow-Up Is Vital
Documenting your observations and following up on any issues raised by operators are essential to success with Gemba walks. Remember, the third principle of Gemba walks is to show respect. If you don’t go back to correct problems or make use of operator feedback, what message does that send? Clearly, it’s not one of respect.
Conversely, when people see their contributions making a difference to quality, that demonstrates to them that their input truly is valued. That, in turn, will make them more likely to open up about other issues they see, such as ways to improve the process or workplace hazards they notice.
Measuring the Success of Your Gemba Walks
Running a Gemba Walk is only the first step—understanding its impact is essential for driving continuous improvement. By tracking key metrics and avoiding common pitfalls, you ensure that your walks lead to real, measurable results.
Key Metrics to Track
- Reduction in safety incidents
- Improved process efficiency
- Employee engagement and feedback
- Resolution rates of identified issues
Common Mistakes to Avoid
- Focusing only on short-term fixes
- Not following up on walk findings
- Failing to involve the right team members in the review process
Continuous Improvement Tips
Use each walk as a learning opportunity. Apply the insights gathered to adjust processes, involve your teams in discussions, and refine your approach over time. This creates a feedback loop that strengthens both operations and culture.
How Often Should You Do Gemba Walks?
The frequency at which plants conduct Gemba walks varies widely from plant to plant. Some sites may do them just once a week, or even every other week. This is more often the case when the walks are longer, say 30 minutes or more.
Quality consultant Richard Nave of The Luminous Group, however, takes the opposite approach.
“I recommend doing a 10-minute walk daily rather than a 30-minute walk once a week,” he says. He notes that if you’re only doing them once a week, an employee who’s not working that day might not see the plant manager on the shop floor for two weeks. “If you go daily—even if you don’t visit that specific employee’s workstation—they will see you on the plant floor.”
He adds that the increased frequency adds value to Gemba walks, in the same way that the increased frequency of checks in layered process audits is what makes them so powerful.
Gemba Walks vs. Layered Process Audits
Layered process audits are a high frequency auditing technique that share several similarities with Gemba walks, including their focus on:
- Engaging operators to garner their feedback, perspective and ideas
- Showing respect and recognizing people for doing things right
- Asking why to uncover what’s really behind process non-conformance
What makes layered process audits different, however, is that they are more structured, requiring participation from multiple ‘layers’ or groups who perform quick, frequent plant floor checks. These checks often complement Gemba walks to further improve processes and audits can optimize operational efficiency. Layered process audits take place every day, sometimes as often as every shift, which helps better prevent process nonconformances that lead to defects and complaints.
Manufacturers with robust layered process audit programs have seen sharp reductions in defects and quality costs, as well as the benefits to quality culture that come from enhanced communication and engagement.
If your organization is already doing Gemba walks, they can provide an ideal starting point for launching a layered process audit program. Managers will already be in the habit of walking around and engaging operators to get their insights, who will also be more accustomed to sharing them.
If your plant already does layered process audits, Gemba walks also can be helpful for analyzing process improvements and verifying that quality gains are held in place.
Gemba Walk Examples
Now that we’ve covered the basics of how Gemba walks work, let’s take a closer look at some Gemba walk examples and how plants can use them to drive continuous improvement.
Uncovering the Hidden Factory
Gemba walks are an ideal opportunity to identify hidden factory issues that might otherwise go unnoticed in your plant. The hidden factory refers to all the processes that are not formalized in any documentation, and yet may still have a significant impact on quality and safety. Direct observation and conversations with operators can help uncover these processes to determine why they are used and what needs to changed.
One plant, for instance, was molding a coolant recovery bottle with a tab on the bottom used to locate the bottle on the vehicle fender when installed. An injector pin in the mold broke so that the tab wasn’t getting ejected uniformly, and would instead come out bent from the warm plastic mold. The operator knew this was happening, and was using his thumb to bend the tab back straight.
In this case, the hidden factory process was actually helping ensure conformance of parts. The problem was that when this particular operator wasn’t working, the person who replaced him wasn’t bending the tabs back. The result: multiple boxes of bottles with bent tabs were sent to customers, requiring significant resources to correct on the part of the supplier.
How could a Gemba walk have helped avoid this issue?
If you had asked the operator whether anything had changed recently, he would have reported that the tabs were coming out crooked and needed to be bent back into position.
Leveraging Operator Insights
An automotive manufacturing plant had installed a screw dispensing machine as a poka yoke at a workstation to ensure precisely four screws were used in the assembly. The goal was that by dispensing the four screws into a tray, the operator wouldn’t inadvertently miss a screw.
The only problem: the tray underneath the machine was too flat, allowing screws to slide off onto the floor. That meant the operator needed to hit the button again to dispense four more screws, leaving many screws in the tray and several on the floor. In other words, it defeated the whole purpose of the poka yoke.
A Gemba walk focused on 5S could help reveal the problem by identifying that there were loose components on the floor of the work area. In this case, the operator suggested that they install a deeper dish rather than a plate under the screw dispenser, allowing operators to use the machine as intended.
Helping Operators Work Safer
Imagine a work cell that requires a hand drill as part of the assembly process. During a Gemba walk, the team notices an extension cord that is a trip hazard in the workstation.
Rather than pointing fingers, the plant manager has a conversation with the operator. During that exchange, he learns that the operator was originally supposed to use a battery drill, but preferred the corded drill because it was lighter.
Based on that feedback, the team decides to add an overhead balancer to the work cell to hold the weight of the battery drill, making it easier for operators to use. In this example, going to the Gemba and talking to the operator was the catalyst for developing an effective solution. Operators feel heard and valued, and they know that management cares about them.
Ultimately, this is the principal goal of Gemba walks. Rather than a tool to drive a specific quality outcome, they are a strategy for building a culture of quality. What they say to employees is that you’re coming to visit their workstations because you care about them. The result is improved visibility and communication about quality issues, and a leadership team that is a visible presence on the plant floor—all essential ingredients of quality culture.
The best practices discussed here can help get you started with Gemba walks, but you don’t have to make it complicated. Instead of getting bogged down in the details, the key is to get out on the plant floor and be consistent. In this way, Gemba walks are a little like yoga: getting started is 5% learning and 95% doing.