A3 Continuous Improvement: Key Steps & Strategies
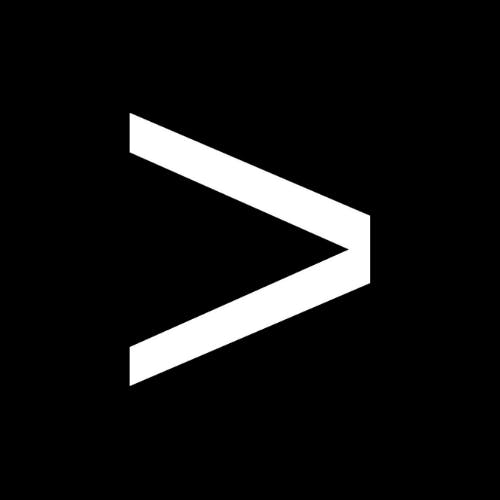
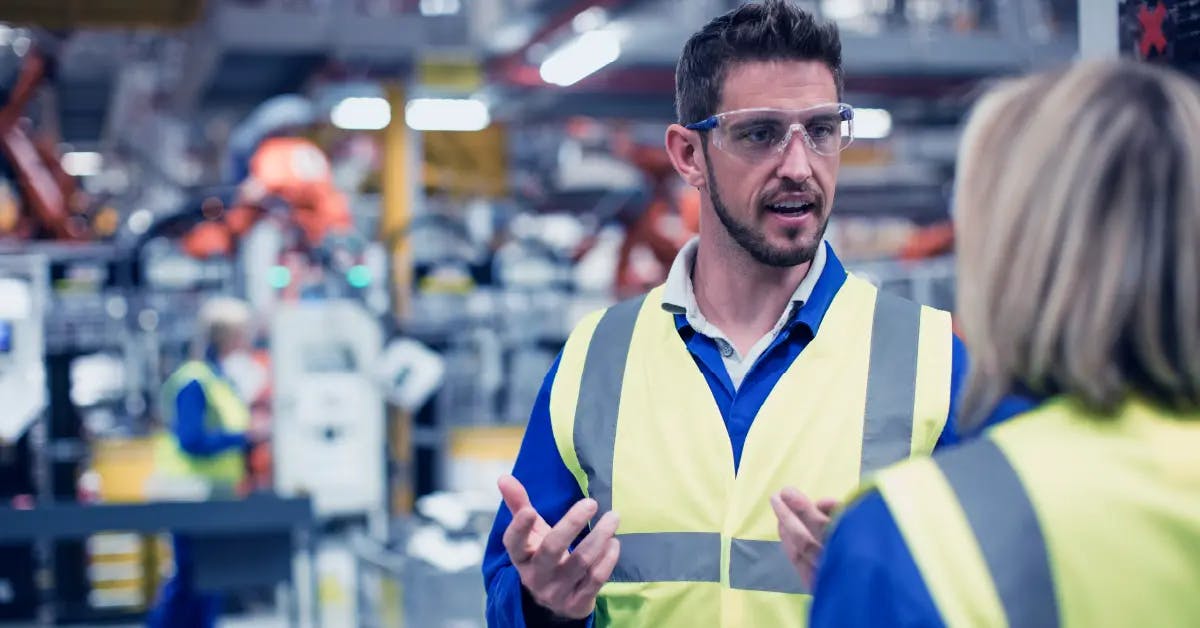
Problem-solving in manufacturing is a notoriously complex and time-consuming process, requiring input from multiple stakeholders and data sources. With so many individuals and data points involved, it’s easy to see why so many plants, despite ongoing process improvement efforts, have a growing backlog of corrective actions—and unresolved problems driving up complaints and costs. What’s needed is a simple and succinct way to view the status of problems and the plan for solving them at a glance. That’s where the A3 continuous improvement comes in, providing a structured problem-solving approach and report for keeping the process on track.
In this article, we cover:
- What the A3 method and why it’s important in manufacturing problem-solving
- Steps in the A3 process and what each part of the A3 report should cover
- The vital importance of countermeasures and follow-up
- Benefits of using the A3 problem-solving process
- Mistakes and pitfalls to avoid
Download a free Fishbone Diagram template to use in your next A3 report
Read how digital transformation drive continuous improvement in manufacturing
What Is the A3 Method?
The A3 method is a problem-solving tool developed at Toyota used to drive continuous improvement through a structured approach to problem-solving. A3 refers to the 11×17 size paper that the process is recorded on, which allows teams to capture the problem and proposed solution in a succinct one-page format.
Steps in the A3 Process
An A3 report helps document the thinking process around a given problem in manufacturing, and typically includes the following sections or steps:
- Problem description
- Background
- Current situation
- Root cause analysis
- Target condition
- Action plan and countermeasures
- Follow-up plan with a clear implementation plan
Problem Description
This section should provide a concise one- to two-sentence overview of the problem you’re trying to solve. The problem must be well-defined at this stage, setting the foundation for the entire problem-solving process.
Background and Context
Here you want to capture any relevant context around the problem, and why it’s significant, within the current state framework. This may include data or targets, as well as diagrams highlighting how the problem is impacting the plant.
Current Situation
In this section, include a short description of the current situation and how it’s contributing to the problem. Look to include information such as:
- Quantitative data and charts, for example, data on defect rates or percent on-time deliveries
- Process flow maps
- Images such as photos of defective parts
Root Cause Analysis
The A3 should document a summary of the root cause analysis process, embodying PDCA cycle principles. For example, you may include a Fishbone diagram showing the potential causes and sub-causes contributing to the problem. If your root cause analysis process was based on a 5 Whys, that should also be recorded on the A3.
Target Condition
Here the goal is to identify what the desired future state is after the problem has been solved. This may cover:
- Quantitative goals such as a target PPM or improvement in on-time delivery
- Diagrams or process flow maps showing what the future process or desired state looks like
- Photos of correctly manufactured parts
Countermeasures and Action Plan
This is one of the most important parts of the A3 report, which should detail:
- Proposed countermeasures
- Action items and who is responsible for each
- Timelines or due dates
- Key outcomes and expected results
- Other areas in the plant where the solution should be applied
Follow-up Plan
Follow-up is also a critical part of the A3 process. In this section, you want to include:
- Verification steps you will take, for example adding a new layered process audit question to check the process
- Any incomplete countermeasures
- Any new problems identified throughout the process
- Results achieved once the process is complete
The Importance of Countermeasures and Follow-Up
The A3 process is built around the Plan-Do-Check-Act cycle, which is designed to continuously improve quality over time. While most of the A3 process falls under the Plan step, countermeasures and follow-up comprise the Do, Check and Act steps.
Countermeasures or corrective actions should be validated to ensure that they actually solve the problem at hand. Many times, teams think they have identified the root cause of a problem, when in reality they have only identified a symptom. In these instances, it makes sense to go back to the 5 Why, for example, and dig even deeper into the underlying factors of the issue.
Verification, such as with regular plant floor checks, looks at whether the problem is still occurring. It also helps evaluate whether corrections are being held in place.
The issue here is that without regular follow-up, people are likely to backslide into familiar habits, erasing the gains made through the A3 process. For instance, let’s say an A3 report results in a new step added to an assembly process to prevent a defect in the field. Checking the process each shift makes sure all operators are performing the new step, and haven’t forgotten or are unaware of the new process.
Transform your approach to quality! Download your free copy now and take the first step towards a more profitable and sustainable manufacturing process.
Benefits of A3 Problem-Solving
There are numerous benefits to using the A3 process as part of your problem-solving and continuous improvement efforts. Below we discuss some of the most important of these, and how they contribute to organizational effectiveness.
Communicating with Your Team
A3 reports are frequently used in meetings where teams track the status of specific problems in a plant. A3 reports, exemplifying A3 thinking, are presented on a flip chart or a projector screen, with owners taking turns to speak briefly on elements such as:
- How they’ve defined the problem
- What the solution is that they are working on
- Any issues they’ve encountered, follow-up items or lessons learned
A3 reports can also be posted in relevant work areas so that other team members are aware of problems and their role in helping eliminate them. Teams can also share completed A3 reports with senior management to communicate the results of ongoing problem-solving initiatives in the plant.
Developing Problem-Solving Skills
A3 continuous improvement is a way of thinking, with the A3 report providing a visual representation of the thinking process. The act of creating an A3 report itself helps document and formalize actions around the Plan-Do-Check-Act process, further strengthening skills in this area.
It also forces people, through A3 thinking, to distil a problem solving summary into a single sheet of paper, so that they must carefully think through and neatly summarize each element of the process.
Creating a Repository of Solutions
By keeping A3 reports in one place, plants can develop a repository of past solutions that teams can refer to when they run into similar problems. This helps reduce duplication of effort in terms of root cause analysis and countermeasures and leverage existing solutions and learnings.
Companies may maintain a binder or database of previous A3 reports with a way to find specific types of problems. For example, if there’s an issue with burrs on stampings, people should be able to search the system to find all A3s dealing with that issue.
Visual Communication
One of the key strengths of A3 reports are that they are a highly visual tool. Emphasizing photos, diagrams and process flow maps helps teams visualize and therefore better understand problems and their solutions.
Building a Culture of Continuous Improvement
The A3 process draws together multiple stakeholders and teams around a common problem-solving goal. As teams work together to share data, ideas and results, the result is an overall improvement in quality culture and collaboration.
Mistakes to Avoid with the A3 Process
In pursuing A3 continuous improvement, plants should avoid several key mistakes, emphasizing the importance of lean thinking and PDCA cycle fidelity. Chief among these is not updating them frequently, leading to outdated A3 reports that are confusing and don’t reflect updated knowledge about the process.
Lack of management involvement can also torpedo the A3 process, sending a message that the problem at hand isn’t a priority for leadership. What results is less buy-in, less input and lower chances of a good result overall. Leadership has several key roles here:
- Regular communication: Management should act as mentors and coaches in reviewing A3 reports and communicating the results to affected parties.
- Identifying resources needed: Leadership should help pinpoint bottlenecks and identify where additional resources are needed to keep the process moving forward, aligning with principles of lean thinking.
- Connecting the dots: Management plays an important role in asking where else the problem may be at play to leverage the results of problem-solving efforts.
Finally, it’s important to remember that A3 reports themselves don’t solve problems. Engineering must apply problem-solving tools to do that—an A3 is just the communication tool where you collect the information.
A3 continuous improvement is more than just a report or problem-solving process. It’s also a way of thinking, helping teams analyze problems in a structured manner while also helping them communicate more effectively. As a management discipline, A3 promotes mentorship and coaching, aligning teams around the Plan-Do-Check-Act process to build a successful problem-solving mindset.